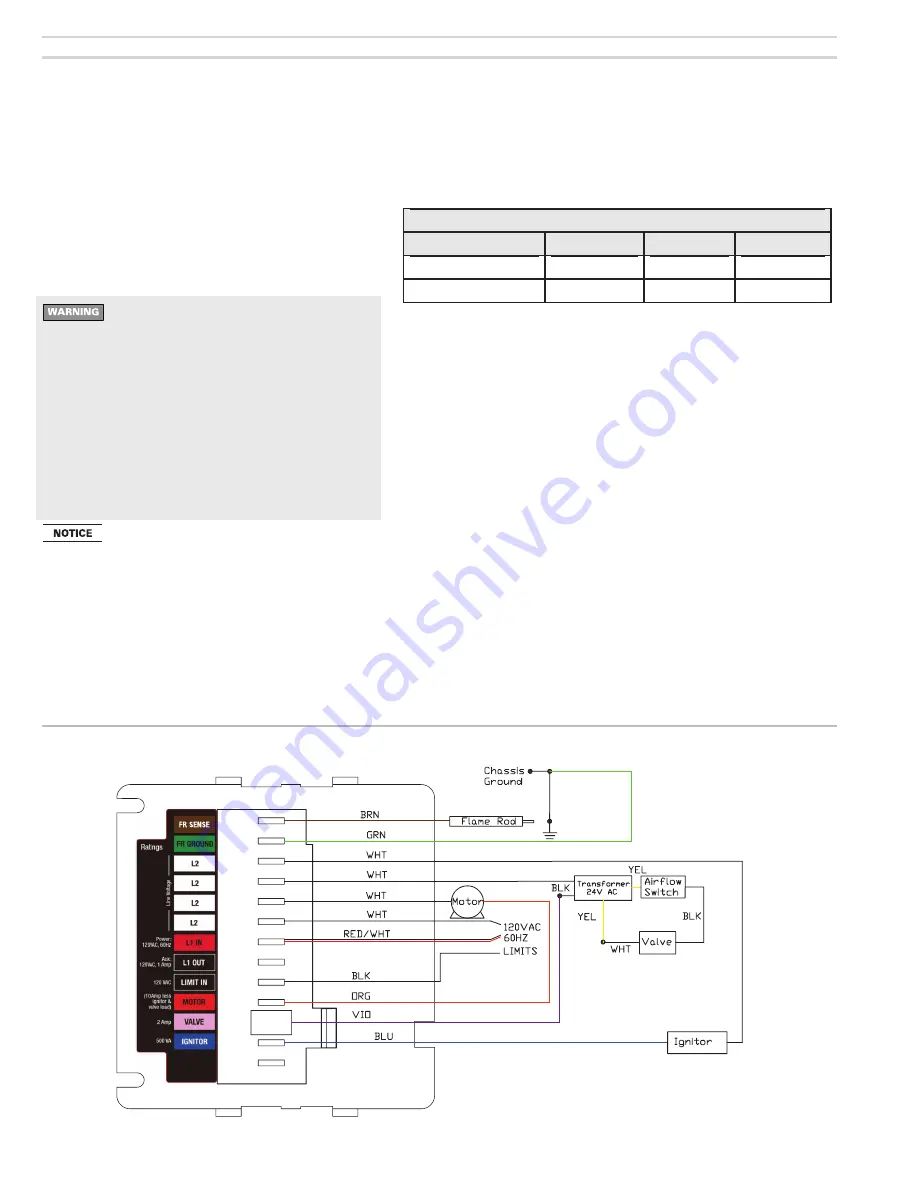
Model EZGas Pro gas burner — Instruction manual
MNEZGas 011917
– 10 –
Where appliance instructions differ from this manual, follow the appliance instructions.
3. Wire burner
Figure 7
Wiring diagram — EZGas Pro burner with 60200FR primary control — typical wiring to appliance
Verify power supply
1. The burner requires a 120
vac
/60
hz
/single-phase power supply, with at least a 5-amp
fuse. The current draw will be (when equipped with Carlin motor and Carlin 41800
electronic ignitor):
2. The 120
vac
power connections to the black and red/white wires of the 60200FR
must be the same polarity
fromthesamepowersource
. DO NOT attempt to supply
separate power sources. Check the power from the heat exchanger with a voltmeter.
Verify that the supply to the black and red/white wires are from the 120
vac
HOT side
and that the power is no less than 102
vac
nor more than 132
vac
. Also verify that the
voltage between neutral and ground does not exceed 3
vac
.
Checking burner flame signal
The 60200FR uses flame rectification to detect the flame. Because the grounded
metal surface area near the flame rod is much larger than the surface of the flame
rod, current flows through the flame more easily in one direction than the other. This
causes an AC voltage applied to the flame rod to result in a DC current. (Note that, if
the flame rod should touch a grounded metal part, the current would be AC, not DC,
and the control would not sense flame and go into a lockout condition).
The minimum flame signal needed to satisfy the 60200FR sensing circuit is
0.8 microamps. The control will register flame failure at any lower signal. When the
EZGas is properly set up. the flame signal strength is typically 2 microamps or greater.
Code compliance
The burner/appliance installation must comply with
codes listed on page 2 and any other locally appli-
cable codes.
General wiring requirements
Readandfollowtheguidelinesbelow.
Failure to comply
could result in severe personal injury, death or substantial
property damage.
Electricalshockhazard
— Disconnect electrical supply
to the burner before attempting to service.
Electrically ground burner
— The burner must be
grounded in accordance with local codes or, in the ab-
sence of local codes, with the National Electrical Code,
ANSI/NFPA 70 (in Canada, per Canadian Electrical Code,
CSA C22.1/CSA C22.2).
Labelallwires
before removing for servicing. Wiring er-
rors could result in unsafe appliance/burner operation.
Read appliance manufacturer’s instructions completely
before wiring burner.
The 60200FR control requires a constant 120
vac
power
source from the appliance as well as power from the
appliance limit circuit. See Figure 7.
Check polarity
carefully. If hot and neutral wires are reversed at
appliance power source, the control will lockout on
flame failure.
If replacing any of the wire supplied with the burner, use
minimum #18 AWG 125°C or better.
Approximate amp draw of EZGas Pro burners
Motor-->
1/15 HP
1/7 HP
1/6 HP
During ignition
2.5 AMPS
2.8 AMPS
3.0 AMPS
Steady operation
2.0 AMPS
2.3 AMPS
2.5 AMPS