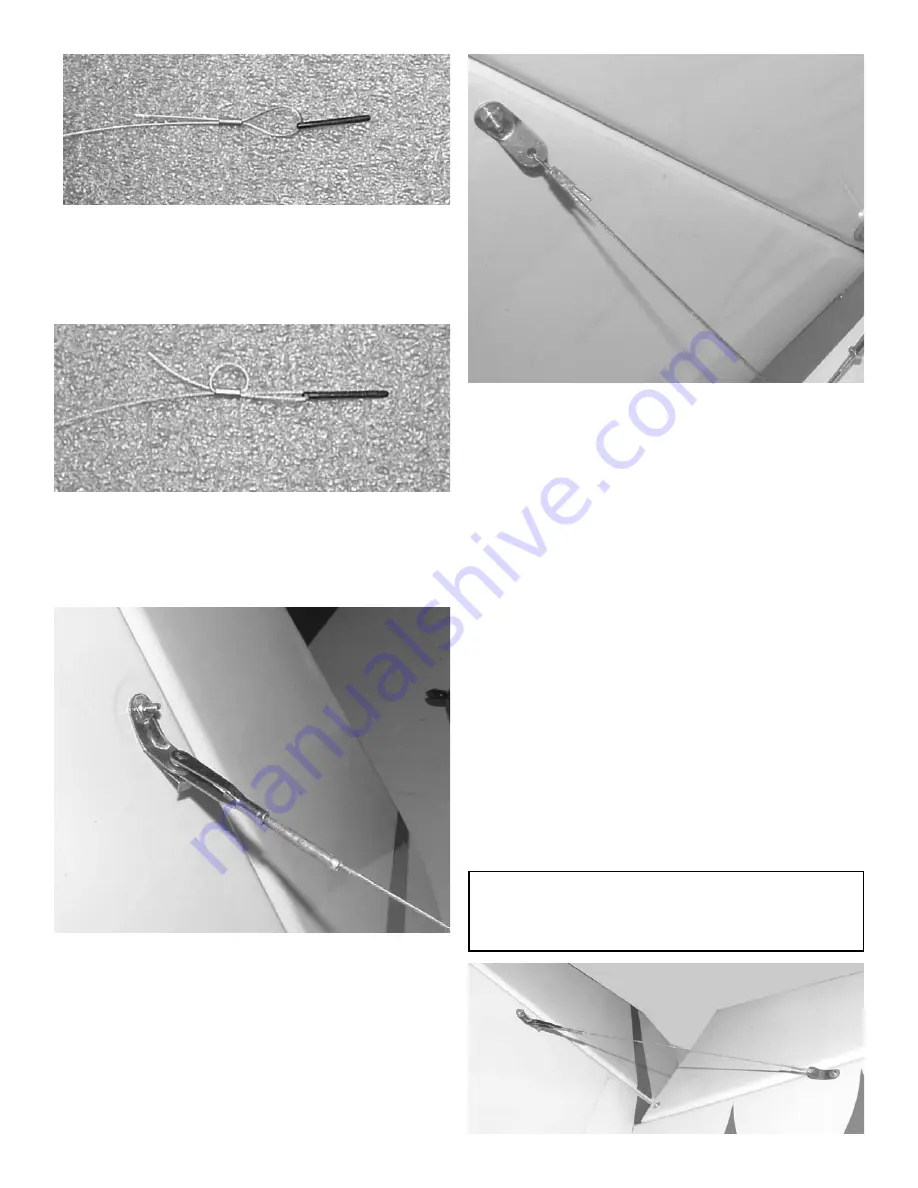
19
6.
Loop the end of the cable back though the
brass tube.
Use pliers and crimp the brass tubing onto the
cable to secure it.
5.
Insert the cable through the 1/16 OD x 1/4”
brass tubing.
Next thread the cable though the hole at the
end of the 2-56 threaded rods and pass it back
through the brass tube.
7.
Screw a golden clevis on the rigging coupler.
and attach it to the bracket at the fin.
Pull the cable to the bracket on the stab and
cut 2” past the hole.
6.
After all four flying wires are in place, adjust
the tension by disconnecting the clevis and
turning.
8.
Pass the cable through the brass tube,
through the bracket on the stab and back
through the brass tube.
Pull the cable tight, but be careful not to put
pressure on the stab or fin. we want the cable
to just be snug at this point and we will adjust
the tension after all four are in place.
Loop the cable back through the brass tube
again and crimp.
Use pliers and crimp the brass tubing onto the
cable to secure it.
8.
Pass the cable through the brass tube, through
the bracket on the stab and back through the
brass tube. Pull the cable tight, but be careful
not to put pressure on the stab or fin. we want
the cable to just be snug at this point and we
will adjust the tension after all four are in place.
Loop the cable back through the brass tube
again and crimp.
Repeat for the other four cables.
The wires should just be snug with no slop,
don’t distort the flying surfaces with
too much tension.