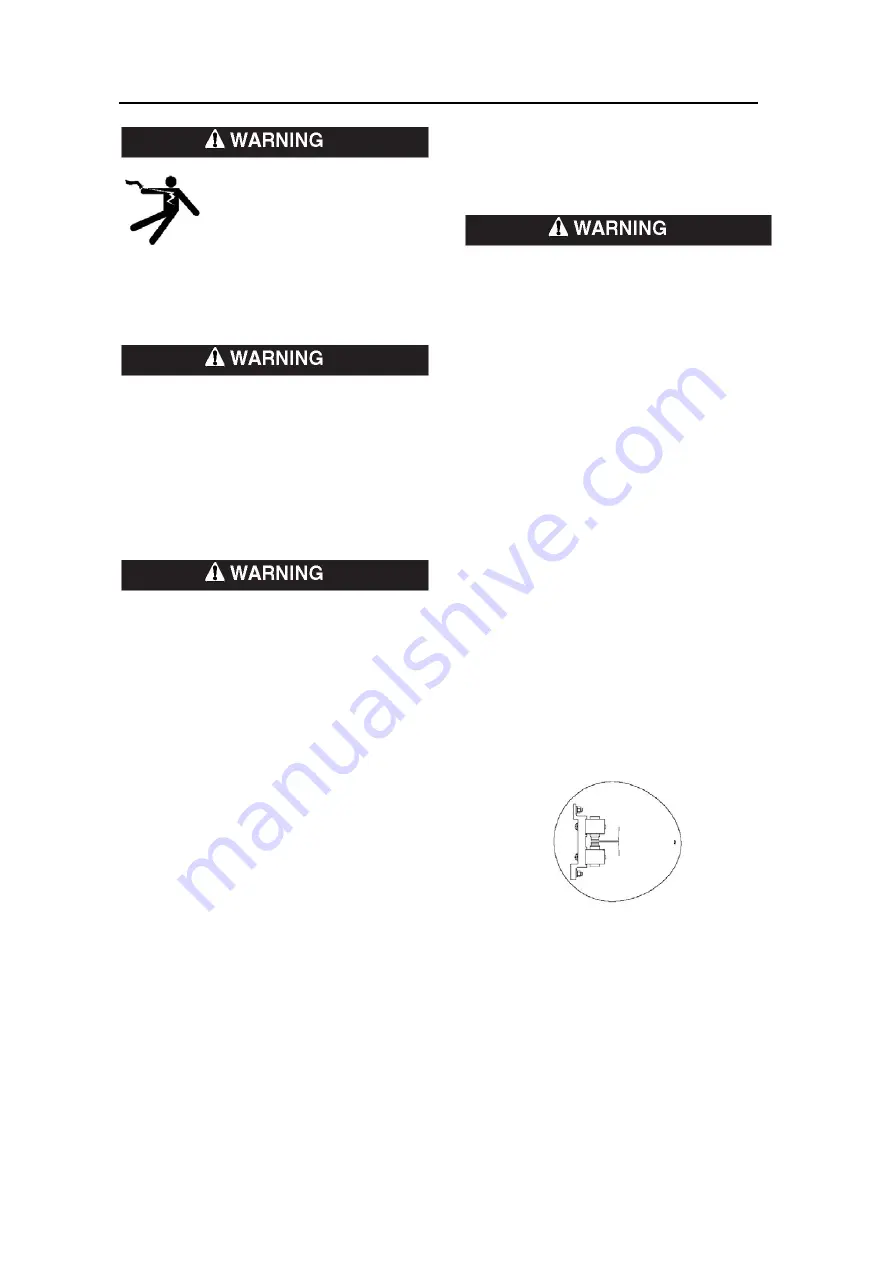
C-1 MAINTENANCE C-1
SAFETY PRECAUTIONS
ELECTRIC SHOCK can kill.
●
Only qualified personnel
should per-form this
maintenance.
●
Turn the input power OFF at
the disconnect switch or fuse
box before working on this equipment.
●
Do not touch electrically hot parts.
INPUT FILTER CAPACITOR
DISCHARGE PROCEDURE
The machine has internal capacitors which are
charged to a high voltage during power-on
conditions. This voltage is dangerous and must
be discharged before the machine can be
serviced. Discharging is done automatically by
the machine each time the power is switched off.
However, you must allow the machine to sit for
at least 5 minutes to allow time for the process
to take place.
To avoid receiving a high frequency shock, keep
the TIG torch and cables in good condition.
ROUTINE AND PERIODIC MAINTENANCE
1 Disconnect power supply lines to machine before
performing periodic maintenance.
2. Periodically clean the inside of the machine with
a low pressure air system. Be sure to clean the
following components thoroughly.
Main Transformer
Electrode/Gas Output Receptacle
Polarity Switch
Rectifier Assembly
Arc Starter/Spark Gap Assembly
PC Boards
Fan Blades
3 Inspect welder output and control cables for
fraying, cuts, and bare spots.
4 Keep TIG torch and cables in good condition.
5 Clean air louvers to ensure proper air flow and
cooling.
6 The fan motor has sealed ball bearings which
require no maintenance.
7
SPARK GAP ADJUSTMENT
The spark gap .020(.5mm) is set at the factory to a
gap of 0.015 inches (0.4mm) See Figure D.1. This
setting is adequate for most applications. Where
less high frequency is desired, the setting can be
reduced to 0.015 inches (0.4mm).
Use extreme caution when working with circuit
of the high frequency. The high voltages
developed can be lethal. Turn the input power
off using the disconnect switch or fuse box
before working inside machine. This is
particularly important when working on the
secondary circuit of the high voltage
transformer (T3) because the output voltage is
dangerously high.
Refer to figure D.1. Note in highly dirty
environments where there is an abundance of
conductive contaminants, use a low pressure air
stream or a firm piece of paper to clean the spark
gap. Do not disturb the factory setting.
To check the spark gap:
-Turn off input power as specified above.
-Remove the right side panel from the machine, the
spark gap box is located on the lower right side.
-Check the spark gap with a feeler gauge. If
adjustment is needed:
-Adjust the gap by loosening the head screw in one
of the aluminum blocks, near the front of the unit
and tighten the screw in the new position.
If the gap is correct:
-Replace the wraparound.
8 Inspect gas hose and inlet fitting for cracks or
leaks.
9 Replace any unreadable labels or decals.
10 Verify that the machine and welding circuit is
properly grounded.
FIGURE D.1 SPARK GAP
FAN MOTOR OR FAN BLADE REPLACEMENT
When installing a new fan blade or fan motor be
sure to maintain proper shaft spacing.
0.5mm
Summary of Contents for PowerMaster205
Page 27: ...B 13 OPERATION B 13...
Page 28: ...B 14 OPERATION B 14...
Page 29: ...B 15 OPERATION B 15...
Page 33: ...B 19 OPERATION B 19...
Page 34: ...B 20 OPERATION B 20...
Page 35: ...B 21 OPERATION B 21...
Page 36: ...B 22 OPERATION B 22...