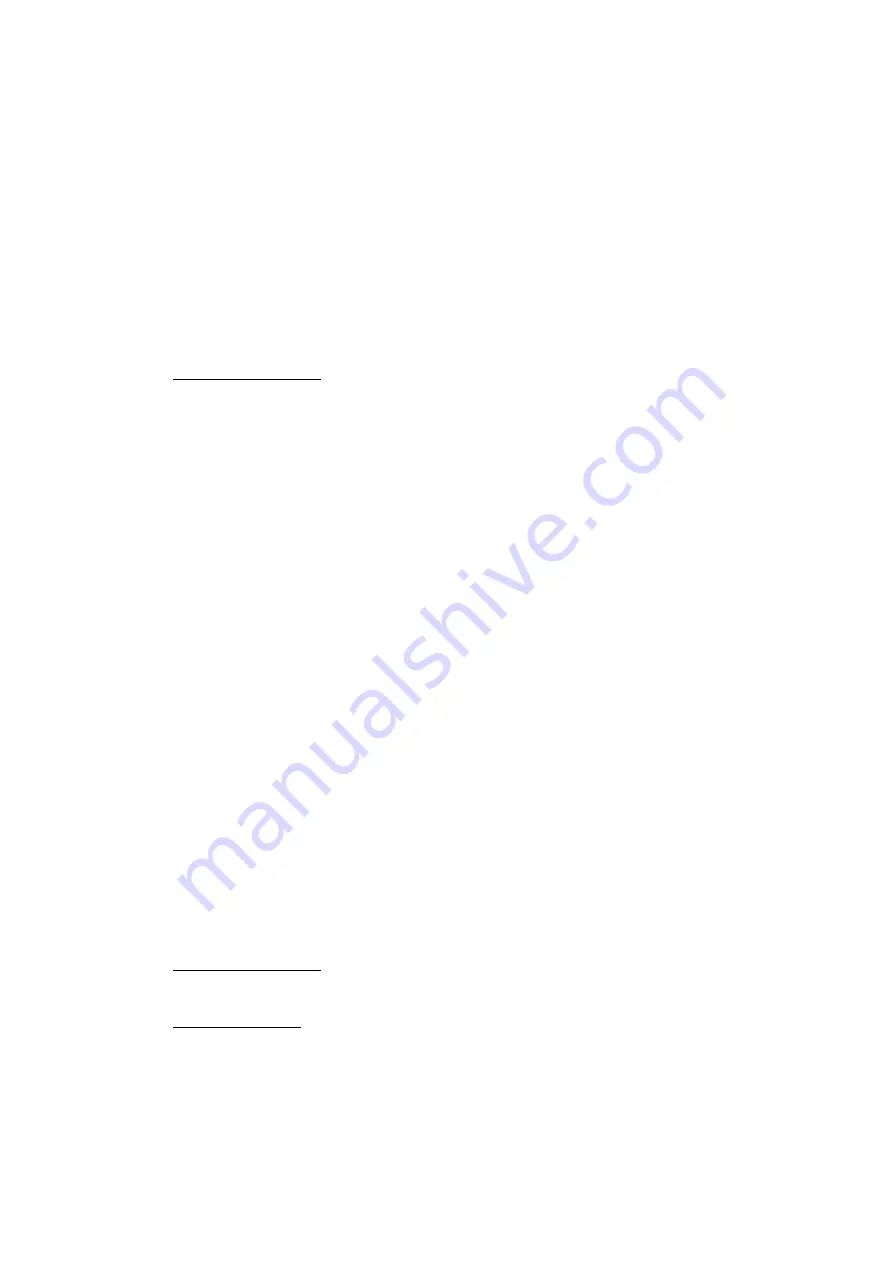
CAPRONI VIZZOLA
C 22 J
7-7
-
The seven AUDIO CONTROL SWITCHES are labelled respectively COM 1, COM 2, NAV
1, NAV 2, ADF, DME, and MKR. They are two position toggle switches with the
positions center-OFF, and down-PHONE. The PHONE position routes the
corresponding audio signal to the pilot’s headphones.
-
The MARKER switch allows to select sensitivity between LOW and HIGH position.
Setting the switch to the spring-loaded TEST position the three MARKER LIGHTS are
lit at full intensity and the audio channel is tested (if the relevant MKR switch is set
to PHONE). This position is used for a preflight test of the MARKER LIGTHTS
operation.
-
The Marker lights are labelled O, M, and I respectively. They provide the pilots with
a visual indication of marker beacon passage.
7.1.20.
COMM 1 Equipment
The VHF-251E communications transceiver is designed to provide maximum ease of
operation; it is equipped with the following displays and controls located on its control
panel: Frequency Selector, Mode Selector, Volume/Test Knob, Frequency Display and
Transmit indicator.
-
The FREQUENCY SELECTORS consist of two concentric knobs used to select
communications frequencies. The inner knob selects kHz and the outer knob selects
MHz frequencies. There are no end stops, therefore frequencies may be selected
turning the knobs in either direction.
-
The MODE SELECTOR knob is located, on the lower left side of the control panel and
is labelled: STORE-SELECT-RECALL. It is used to control the single channel memory.
When in SELECT position, a desired frequency may be may be selected by the
FREQUENCY SELECTORS. Turning the knob momentarily to the STORE position, the
selected frequency is stored in in the memory replacing the previously stored
frequency. The knob is spring loaded. The RECALL position allows operation of the
transceiver on the previously stored frequency. When the knob is in the SELECT
position, any of the 720 channels within frequency range, can be selected for
operation via the FRQUENCY SELECTOR.
-
The VOLUME/TEST Knob is a rotary control concentric to the MODE SELCRTOR Knob.
In The fully counter-clockwise position the transceiver is switched OFF. Rotating
clockwise increases the radio volume.
-
The FREQUENCY DISPLAY is a five-digit electronic indicator that displays the
frequency to which the transceiver is tuned, regardless or the position of the MODE
SELCTOR.
-
The TRANSMIT INDICATOR is a lamp labelled XMIT which monitors the radio
frequency output during transmission.
7.1.21.
COMM 2 equipment
See 7.1.20.
7.1.22.
NAV 1 equipment
The Collins VIR 351 has a capability of 200 channels on the VHF frequency range, from 108.00
thru 117.95 MHz in 50 kHz steps, 160 channels being VOR channels and the remaining 40
being LOC channels. The NAV 1 receiver is also capable of tuning the COLLING GLS 350 E
glideslope receiver. Both the NAV 1 and NAV 2 are capable of tuning the OLLINS TCR 451