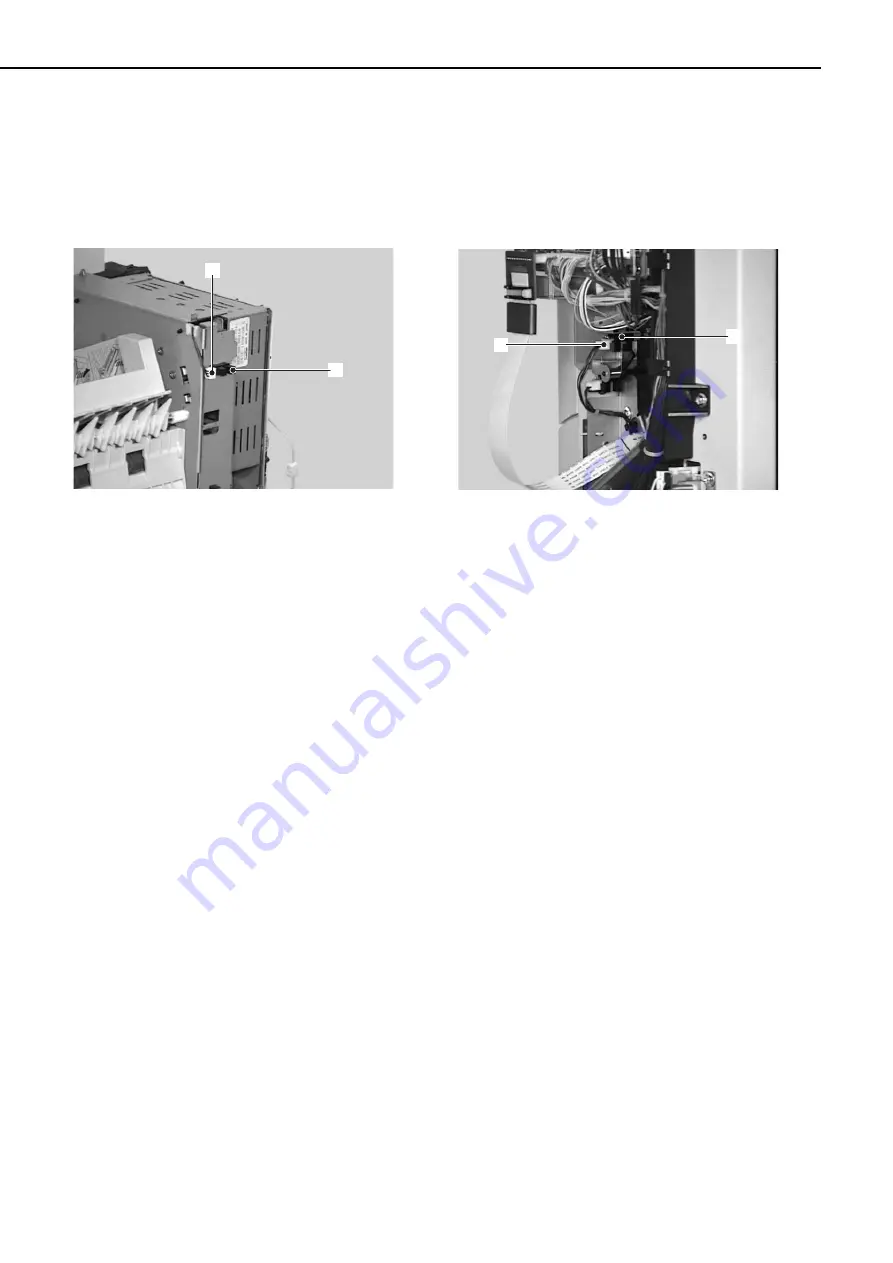
B. Entrance Paper Sensor
1) Following the right top cover removal
procedure described on Page 3-3,
remove the right top cover.
2) Disconnect the connector, and then
remove the entrance paper sensor.
➀
Connector
➁
Entrance paper sensor
Figure 3-6-2
C. Reversing Paper Sensor
1) Following the rear cover removal proce-
dure described on Page 3-4, remove the
rear cover.
2) Disconnect the connector, and then
remove the reversing paper sensor.
➀
Connector
➁
Reversing paper sensor
Figure 3-6-3
3 - 16
CHAPTER 3
➁
➀
➀
➁
Summary of Contents for STAPLER STACKER SS-72
Page 8: ......
Page 24: ......
Page 26: ......
Page 58: ......
Page 67: ...IV MAIN PARTS A Locations Stapler Figure 3 4 1 3 9 CHAPTER 3 ...
Page 92: ......
Page 94: ......
Page 101: ...This page intentionally left blank 4 7 CHAPTER 4 ...
Page 116: ...This page intentionally left blank 4 22 CHAPTER 4 ...
Page 121: ...APPENDIX I GENERAL CIRCUIT DIAGRAM A 1 II LIST OF SIGNALS A 3 ...
Page 122: ......
Page 124: ......
Page 128: ......