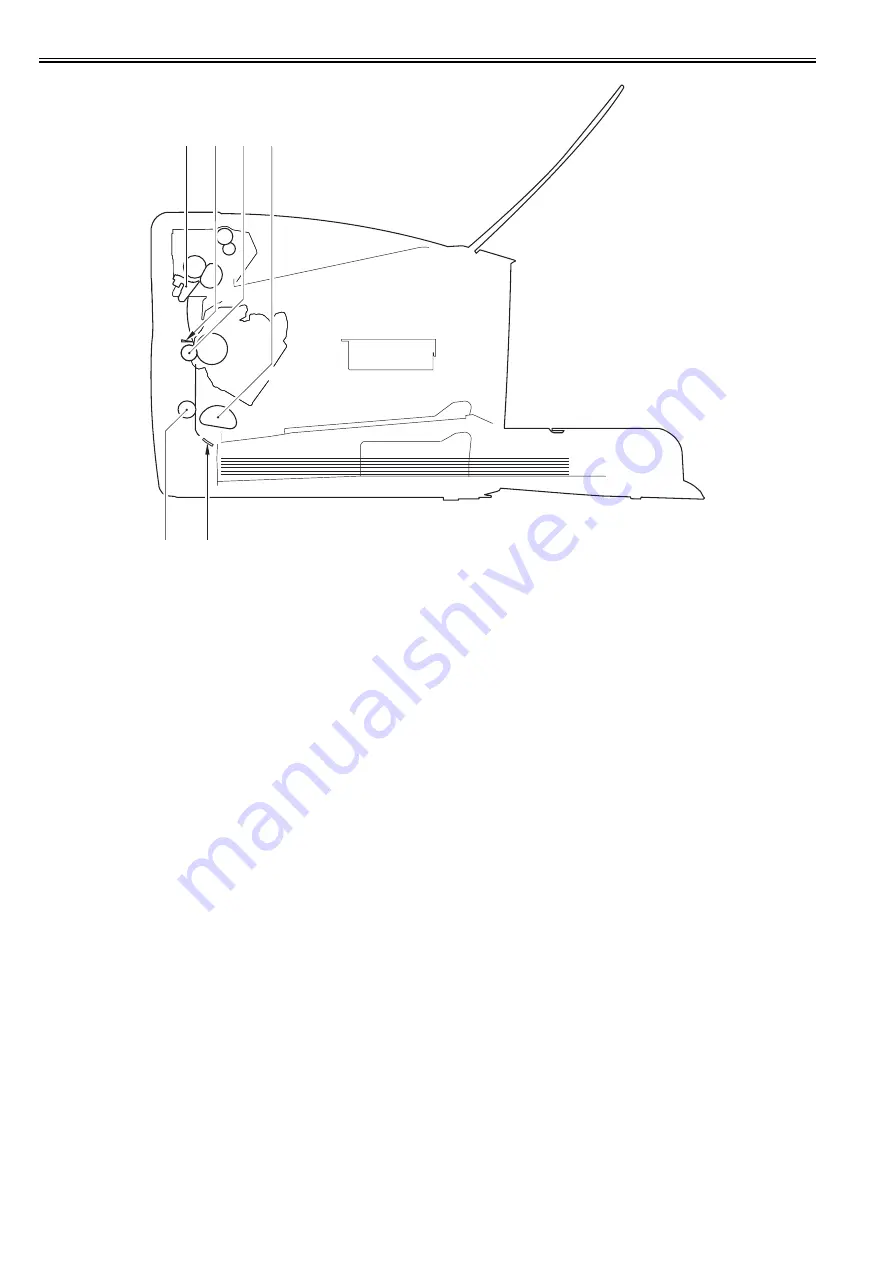
Chapter 4
4-2
F-4-1
T-4-1
Follow the procedure below for cleaning during servicing.
1) Fixing inlet guide
Clean it with a dry lint-free paper.
2) Static eliminator
Clean it with a dry lint-free paper.
3) Transfer roller
Basically, do not touch it with your hands or clean it. When cleaning is absolutely necessary, clean with a dry lint-free paper.
Take care not to touch the roller and let solvents or oils be removed.
4) Pickup roller
Clean it with a dry lint-free paper.
5) Separation pad
Clean the rubber part with a lint-free paper
6) Feeding roller
Clean it with a dry lint-free paper.
4.4.2 Cleaning Method
0025-1256
LBP6000 / LBP6000B
Cleaning at servicing
[1]
Fixing inlet guide
[2]
Static eliminator
[3]
Transfer roller
[4]
Pickup roller
[5]
Separation pad
[6]
Feeding roller
[1]
[3]
[4]
[6]
[5]
[2]
Summary of Contents for LBP3010 Series
Page 1: ...Sep 8 2010 Service Manual LBP6000 6018 3010 3100 3150 Series ...
Page 2: ......
Page 6: ......
Page 12: ...Contents ...
Page 13: ...Chapter 1 PRODUCT DESCRIPTION ...
Page 14: ......
Page 16: ......
Page 28: ......
Page 29: ...Chapter 2 TECHNICAL REFERENCE ...
Page 30: ......
Page 74: ......
Page 75: ...Chapter 3 DISASSEMBLY AND ASSEMBLY ...
Page 76: ......
Page 119: ...Chapter 4 MAINTENANCE AND INSPECTION ...
Page 120: ......
Page 122: ......
Page 126: ......
Page 127: ...Chapter 5 TROUBLESHOOTING ...
Page 128: ......
Page 130: ......
Page 137: ...Chapter 6 APPENDIX ...
Page 138: ......
Page 140: ......
Page 144: ......
Page 145: ...Sep 8 2010 ...
Page 146: ......