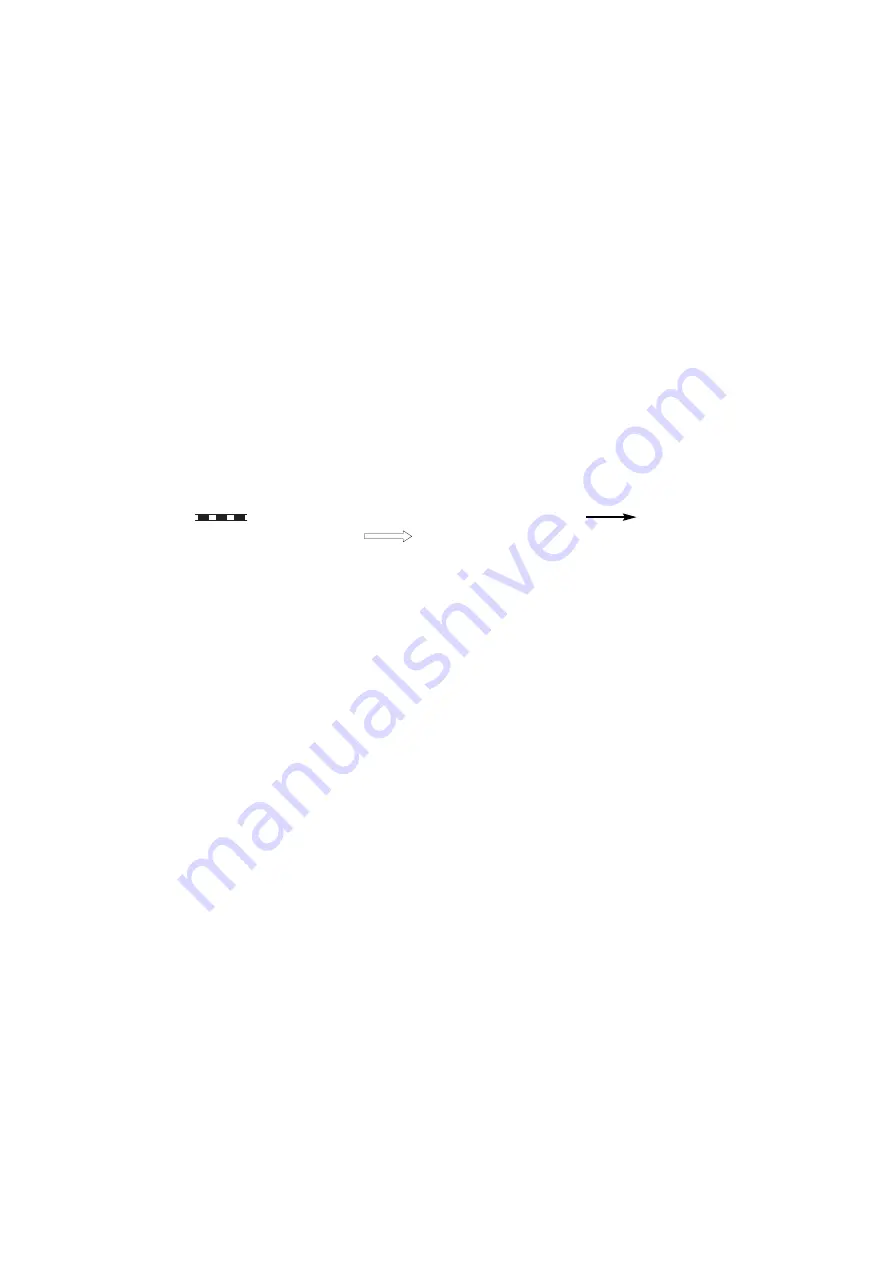
CHAPTER 2
OPERATION AND TIMING
1. This chapter describes the printer functions, the relationships between mechanisms and cir-
cuits, and the timing of operations. Mechanical linkages are indicated by black and white
lines ( ), the flow of control signals by solid arrows ( ), and the flow of groups
of signals by outline arrows ( ).
2. An active-high signal is indicated by "H" or by a signal name without a slash in front of it,
such as "PSNS." An active-low signal is indicated by "L" or by a signal name with a slash in
front of, such as "/SCNON."
A signal that is "H" or has a name without a slash is active at the supply voltage level
(indicating that the signal is being output), and inactive at ground level (indicating that the
signal is not being output).
A signal that is "L" or has a slash in front of its name is active at ground level, and inac-
tive at the supply voltage level.
There is a microcomputer in this printer. But as the internal operation of the microcom-
puter cannot be checked, an explanation of the operation of the microcomputer has been left
out.
As it is assumed that no repair will be made to customer circuit boards, the explanation
of board circuits is limited to an outline using block diagrams. So there are two types of cir-
cuit explanations; (1) everything from the sensor to the input sections of the major circuit
boards, (2) everything from the output sections of the major circuit boards to the loads.
These are explained with block diagrams according to the function.
I.
BASIC OPERATION ................. 2-1
II.
ENGINE CONTROL SYSTEM.... 2-4
III. LASER/SCANNER SYSTEM ..... 2-22
IV.
IMAGE FORMATION SYSTEM . 2-28
V.
PICK-UP/FEED SYSTEM ......... 2-38
VI. VIDEO CONTROL SYSTEM...... 2-50
VII. PAPER FEEDER...................... 2-58
VIII. ENVELOPE FEEDER ............... 2-63
IX. DUPLEXING UNIT ................... 2-68
Summary of Contents for LBP-1760
Page 8: ......
Page 10: ......
Page 12: ...This page intentionally left blank 1 2 CHAPTER 1 ...
Page 23: ...Figure 1 5 1 1 13 CHAPTER 1 100mm 1220mm 600mm 630mm ...
Page 28: ...Figure 1 5 3 1 18 CHAPTER 1 ...
Page 34: ...This page intentionally left blank 1 24 CHAPTER 1 ...
Page 36: ......
Page 38: ......
Page 75: ...This page intentionally left blank 2 37 CHAPTER 2 ...
Page 80: ...Figure 2 5 3 2 42 CHAPTER 2 ...
Page 83: ...Figure 2 5 6 2 45 CHAPTER 2 ...
Page 85: ...This page intentionally left blank 2 47 CHAPTER 2 ...
Page 92: ......
Page 114: ......
Page 160: ......
Page 162: ......
Page 195: ...This page intentionally left blank 4 33 CHAPTER 4 ...
Page 199: ...This page intentionally left blank 4 37 CHAPTER 4 ...
Page 222: ...C Clutches Solenoids Figure 4 9 4 4 60 CHAPTER 4 SL102 CL101 SL101 SL701 ...
Page 224: ...D Motors Others Figure 4 9 6 4 62 CHAPTER 4 FM101 H901 M101 FM701 M702 M701 ...
Page 226: ...E PCBs Figure 4 9 7 4 64 CHAPTER 4 ...
Page 229: ...Figure 4 9 9 4 67 CHAPTER 4 J604 J602 J601 J104 J105 J72 J110 J603 J6 J7 J1 J8 J5 J4 J3 J2 ...
Page 232: ......
Page 234: ......
Page 270: ...COPYRIGHT C 1998 CANON INC CANON LBP 1760 REV 0 MAY 1998 PRINTED IN JAPAN IMPRIME AU JAPON ...
Page 277: ......
Page 279: ......
Page 280: ......
Page 286: ......
Page 288: ......
Page 289: ......
Page 295: ......
Page 296: ......
Page 304: ......
Page 306: ...PRINTED IN JAPAN IMPRIME AU JAPON 0698AB0 50 CANON INC ...
Page 310: ...COPYRIGHT C 1998 CANON INC CANON LBP 1760 REV 0 MAY 1998 PRINTED IN JAPAN IMPRIME AU JAPON iv ...
Page 312: ...COPYRIGHT C 1998 CANON INC CANON LBP 1760 REV 0 MAY 1998 PRINTED IN JAPAN IMPRIME AU JAPON vi ...
Page 315: ......
Page 335: ......
Page 356: ......
Page 358: ......
Page 359: ......
Page 366: ......
Page 368: ......
Page 369: ......
Page 378: ......
Page 388: ......
Page 392: ......