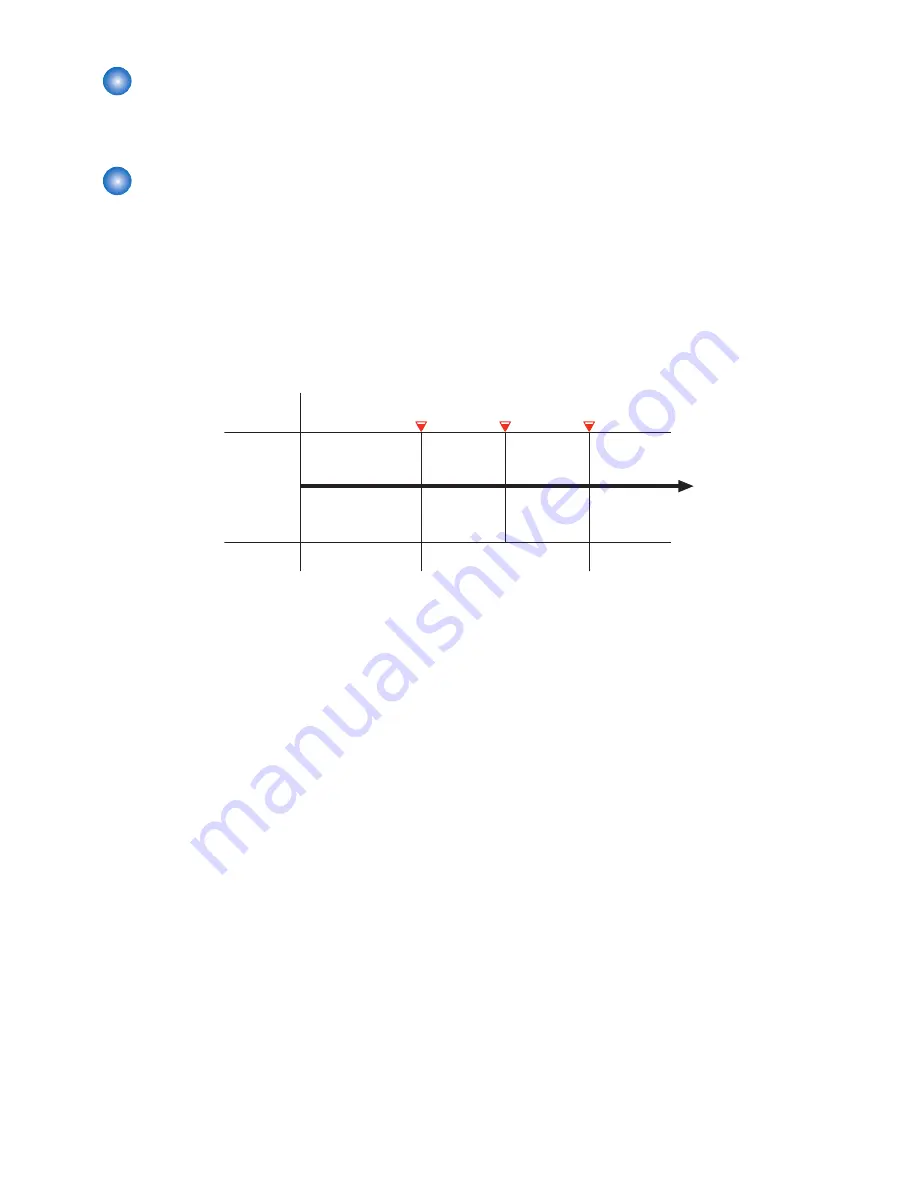
Lifter Control
When the cassette is set, the Cassette 2 Lifter Motor rotates to raise the Lifter Plate. Then, the paper is raised to the position to
be picked up.
Registration Control
It is a control to align the image on the ITB with the paper at a specified timing.
Based on the leading edge detection by the Pre-Registration Sensor, the following 2 controls are used:
• Non-stop Registration Control
• Stop Registration Control
Basically, non-stop registration control is used. However, if the Pre-Registration Sensor is turned ON later than the period of time
corresponding to the maximum correctable distance of the non-stop registration control, it is not possible to align the image on
the ITB with the paper at the specified timing, and a jam code is generated. (Jam code: 0A90)
On the other hand, if the Pre-Registration Sensor is turned ON earlier than the period of time corresponding to the minimum
correctable distance of the non-stop registration control, the image on the ITB is aligned with the paper at the specified timing by
the stop registration control.
Sensor ON
(early)
Sensor ON
(late)
Jam occurs
Paper feed
Sensor
detection
timing
Non-stop Registration Control
Decelerated
Accelerated
Stop Registration
Control
Sensor ON
(ideal)
■ Non-stop Registration Control
It is a control to align paper and image on the ITB at a specified timing by increasing or decreasing the paper feed speed. Since
paper is not stopped at the registration position, paper interval can be shortened and productivity can be improved.
■ Stop Registration Control
It is a control to stop paper at the registration position, align the image on the ITB with the paper at a specified timing, and then
resume paper feed.
Stop registration control stops the Pre-registration Roller. Paper fed by the Pre-registration Roller after being picked up from the
cassette generates an arch due to being pushed against the Registration Roller which has been stopped. In order to align the
image on the ITB with the paper at a specified timing, this control stops paper feed with the paper arched, aligns the image on
the ITB with the paper at the specified timing, and then resumes paper feed.
2. Technical Explanation
16
Summary of Contents for AJ1
Page 1: ...Revision 2 0 Cassette Feeding Unit AJ1 Service Manual ...
Page 6: ...Safety Precautions Notes Before it Works Serving 2 ...
Page 8: ...Product Overview 1 Overview 4 ...
Page 11: ...Technical Explanation 2 Basic Configuration 7 Controls 10 ...
Page 14: ...Paper Path Cassette 2 2 Technical Explanation 9 ...
Page 23: ...Periodical Service 3 List of Periodical Service Works 19 ...
Page 48: ...Adjustment 5 Pickup Feed System 44 ...
Page 54: ...APPENDICES Service Tools 50 General Circuit Diagram 51 ...