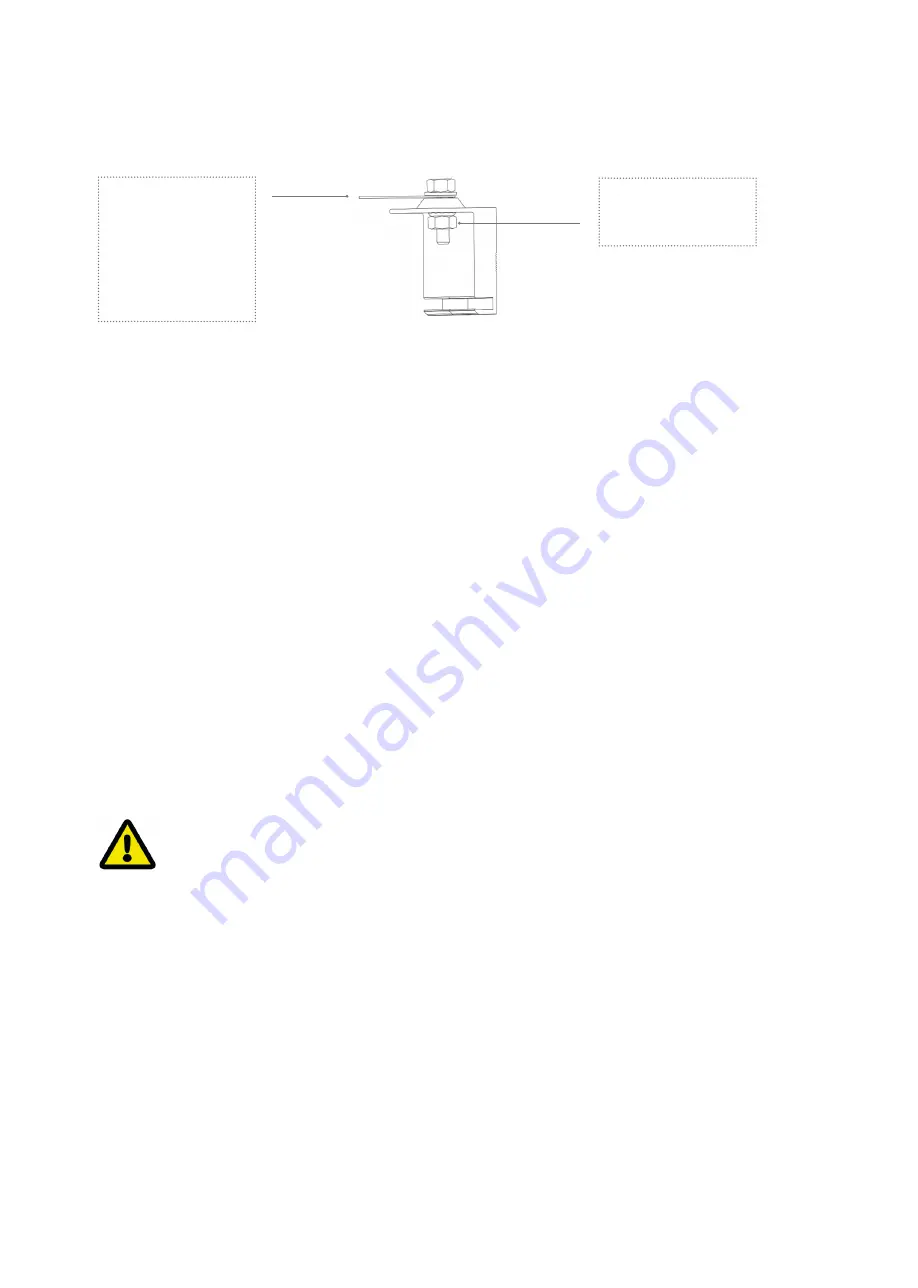
| 11
· A grounding kit containing an M5 (3/16“) SS cap bolt, an
M5 (3/16“) SS flat washer, an M5 (3/16“) SS cup washer,
and an M5 (3/16“) SS nut (with teeth) should be used to
attach copper grounding wire to a pre-drilled grounding
hole on the frame (see image above). The grounding holes
are located at the upper and lower edges of the long side
frame, close to the module short sides.
· Mounting rail designs should be such to allow easy access
to the grounding holes located on the long side of the fra-
me, in order to enable the equipment grounding function
when required.
· Place the wire between the flat washer and the cup was-
her. Ensure that the cup washer is positioned between the
frame and the wire with the concave side up to prevent
galvanic corrosion. Tighten the bolt securely using the SS
toothed nut. A wrench may be used to do this. The tigh-
tening torque is 3-7 Nm (2.2-5.2 ft-lbs).
6.0
MOUNTING INSTRUCTIONS
The applicable regulations pertaining to work
safety, accident prevention and securing the
construction site must be observed. Workers
and third party personnel shall wear or install fall arrest
equipment. Any third party need to be protected against
injuries and damages.
· The mounting design must be certified by a registered
professional engineer. The mounting design and
procedures must comply with local codes and
requirements from all relevant authorities.
· Canadian Solar Inc. does not provide mounting hardware.
· The system designer and installer are responsible for load
calculations and for proper design of support structure.
· The loads described in this manual correspond to test
loads. For installations complying with IEC 61215-2:2016
1. To fix the wire between
the flat washer and
cup washer, place the
cup washer (concave
side up) between the
frame and the wire.
2. Then tighten the bolt
using the toothed nut.
GROUNDING METHOD:
BOLT + TOOTHED NUT + CUP WASHER.
and UL 1703, a safety factor of 1.5 should be applied for
calculating the equivalent maximum authorized design
loads. Project design loads depend on construction,
applicable standards, location and local climate.
Determination of the design loads is the responsibility of
the racking suppliers and/or professional engineers. For
detailed information, please follow local structural code or
contact your professional structural engineer.
· Use appropriate corrosion-proof fastening materials. All
mounting hardware (bolts, spring washers, flat washers,
nuts) should be hot dip galvanized or stainless steel.
· Use a torque wrench for installation.
· Do not drill additional holes or modify the module frame.
Doing so will void the warranty.
WHEN CLAMPS ARE USED AS FIXING MATERIAL:
· Install and tighten the module clamps to the mounting
rails using the torque stated by the mounting hardware
manufacturer. System designer and installer are
responsible for load calculations and for proper design
of support structure. It is recommended to use a torque
wrench for installation. Tightening torques should
respectively be within 17-23 Nm (12.5-17.0 ft-lb) for
M8x1.25-Grade8.8 (5/16”-18 Grade B7) galvanized or A2-
70 stainless steel coarse thread bolts, depending on bolt
class. The yield strength of bolt and nut should not be less
than 450 MPa.
· Clamp material should be anodized aluminum alloy or
steel of appropriate grade. For frameless module used
clamps, one buffer rubber material (Recommended
material is EPDM) must be added between the clamp and
the glass.
· Clamp positions are of crucial importance for the reliability
of the installation, the clamp centerline must only be
positioned within the authorized position ranges indicated
below, depending on the configuration and load.