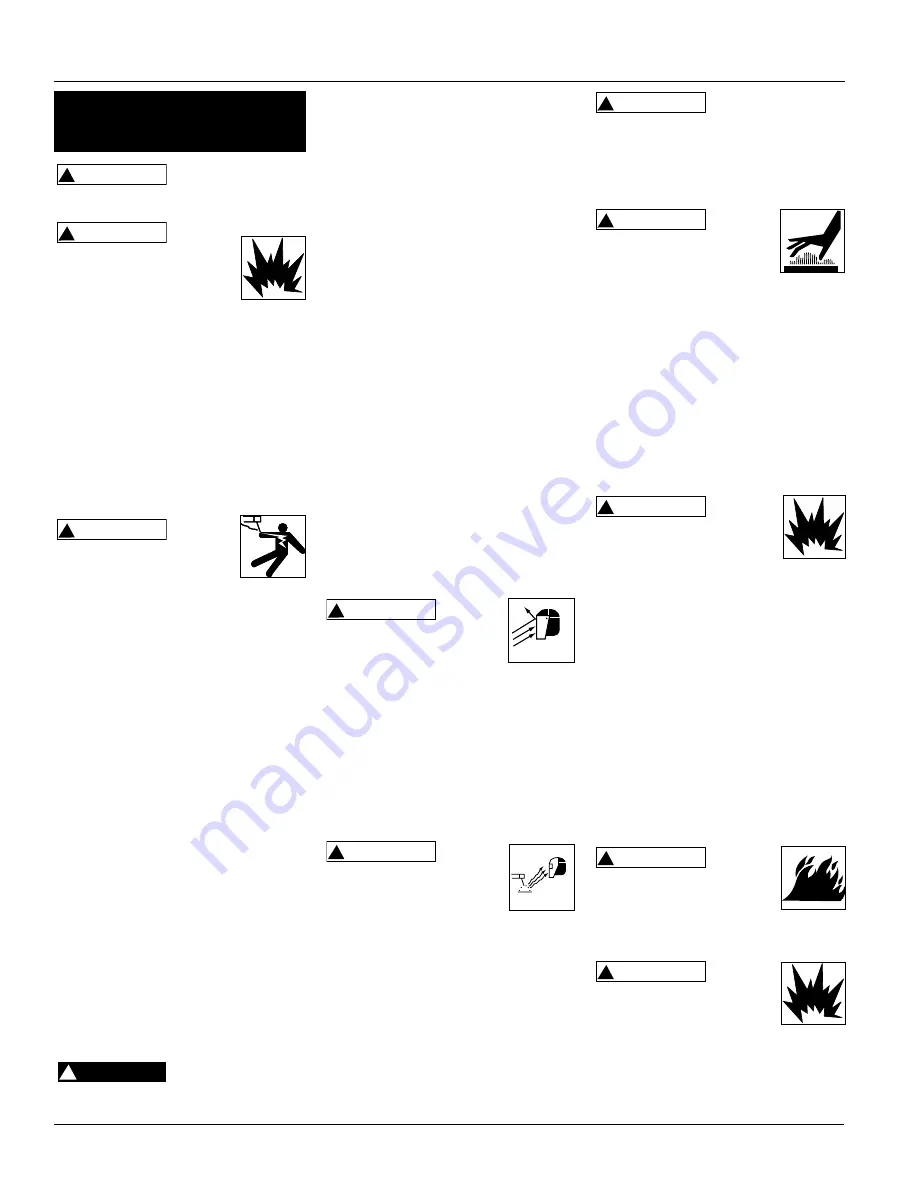
2
Wire Feed Arc Welder
Torch is “live” (has
current potential)
at all times when machine is turned on.
Always keep a fire
extinguisher accessible while
performing arc welding
operations.
●
Before starting or servicing any
electric arc welder, read and
understand all instructions. Failure
to follow safety precautions or
instructions can cause equipment
damage and/or serious personal
injury or death.
●
All installation, maintenance, repair
and operation of this equipment
should be performed by qualified
persons only in accordance with
national, state, and local codes.
Improper use of electric arc
welders can cause electric
shock, injury, and death!
Take all precautions described in this
manual to reduce the possibility of
electric shock.
●
Verify that all components of the
arc welder are clean and in good
condition prior to operating the
welder. Be sure that the insulation
on all cables, wire feed gun, and
power cords is not damaged.
Always repair or replace damaged
components before operating the
welder. Always keep welder panels,
shields, etc. in place when operating
the welder.
●
Always wear dry, protective clothing
and welding gloves, and insulated
footwear.
●
Always operate the welder in a
clean, dry, well ventilated area. Do
not operate the welder in humid,
wet, rainy, or poorly ventilated
areas.
●
Be sure that the work piece is
properly supported and grounded
prior to beginning any electric arc
welding operation.
●
Coiled welding cable should be
spread out before use to avoid
overheating and damage to
insulation.
Never immerse the
wire or wire feed
gun in water. If the welder becomes
!
DANGER
!
WARNING
!
WARNING
!
WARNING
wet for any reason, be absolutely
certain that it is completely clean and
dry prior to attempting use!
●
Always shut the equipment off and
unplug the power prior to moving
the unit.
●
Always attach the work lead first.
●
Verify that the work piece is
securely grounded.
●
Always shut off electric arc welding
equipment when not in use, and cut
off any excess wire from the wire
feed gun.
●
Never allow any part of the body to
touch the wire and ground or
grounded work piece at the same
time.
●
Awkward welding conditions and
positions can be electrically
hazardous. When crouching,
kneeling or at elevations, be sure to
insulate all conductive parts, wear
appropriate protective clothing, and
take precautions to prevent injury
from falls.
●
Never attempt to use this
equipment at current settings or
duty cycles higher than those
specified on the equipment labels.
●
Never use an electric arc welder to
thaw frozen pipes.
Flying
sparks and hot metal can
cause injury. As welds cool,
slag can be thrown off. Take
all precautions described in this manual
to reduce the possibility of injury from
flying sparks and hot metal.
●
Wear ANSI approved face shield or
safety glasses with side shield
protection when chipping or
grinding metal parts.
●
Wear ear plugs when welding
overhead to prevent spatter or slag
from falling into ears.
Electric arc
welding operations produce
intense light and heat and
ultraviolet (UV) rays. This
intense light and UV rays can cause
injury to eyes and skin. Take all
precautions described in this manual to
reduce the possibility of injury to eyes
and skin.
●
All persons operating this
equipment or in the area while
equipment is in use must wear
protective welding gear including:
welding helmet or shield with at
least shade 10, flame resistant
clothing, leather welding gloves,
and full foot protection.
!
WARNING
!
WARNING
Never look at arc
welding operations
without eye protection as described
above. Never use a shade filter lens
that is cracked, broken, or rated below
number 10. Warn others in the area not
to look at the arc.
Electric arc welding
operations cause sparks and
heat metal to temperatures
that can cause severe burns! Use
protective gloves and clothing when
performing any metal working
operation. Take all precautions
described in this manual to reduce the
possibility of skin and clothing burns.
●
Make sure that all persons in the
welding area are protected from
heat, sparks, and ultraviolet rays.
Use additional face shields and
flame resistant barriers as needed.
●
Never touch work pieces until
completely cooled.
Heat and sparks produced
during electric arc welding
and other metal working
operations can ignite flammable and
explosive materials! Take all
precautions described in this manual to
reduce the possibility of flames and
explosions.
●
Remove all flammable materials
within 35 feet (10.7 m) of welding
arc. If removal is not possible,
tightly cover flammable materials
with fire proof covers.
●
Do not operate any electric arc
welder in areas where flammable or
explosive vapors may be present.
●
Take precautions to be sure that
flying sparks and heat do not cause
flames in hidden areas, cracks,
behind bulkheads, etc.
Fire hazard! Do not weld on
containers or pipes that
contain or have contained
flammable materials or gaseous or
liquid combustibles.
Arc welding closed cylinders
or containers such as tanks
or drums can cause explosion
if not properly vented! Verify that any
cylinder or container to be welded has
an adequate ventilation hole, so that
expanding gases can be released.
!
WARNING
!
WARNING
!
WARNING
!
WARNING
!
WARNING
General Safety
(Continued)
www.chpower.com