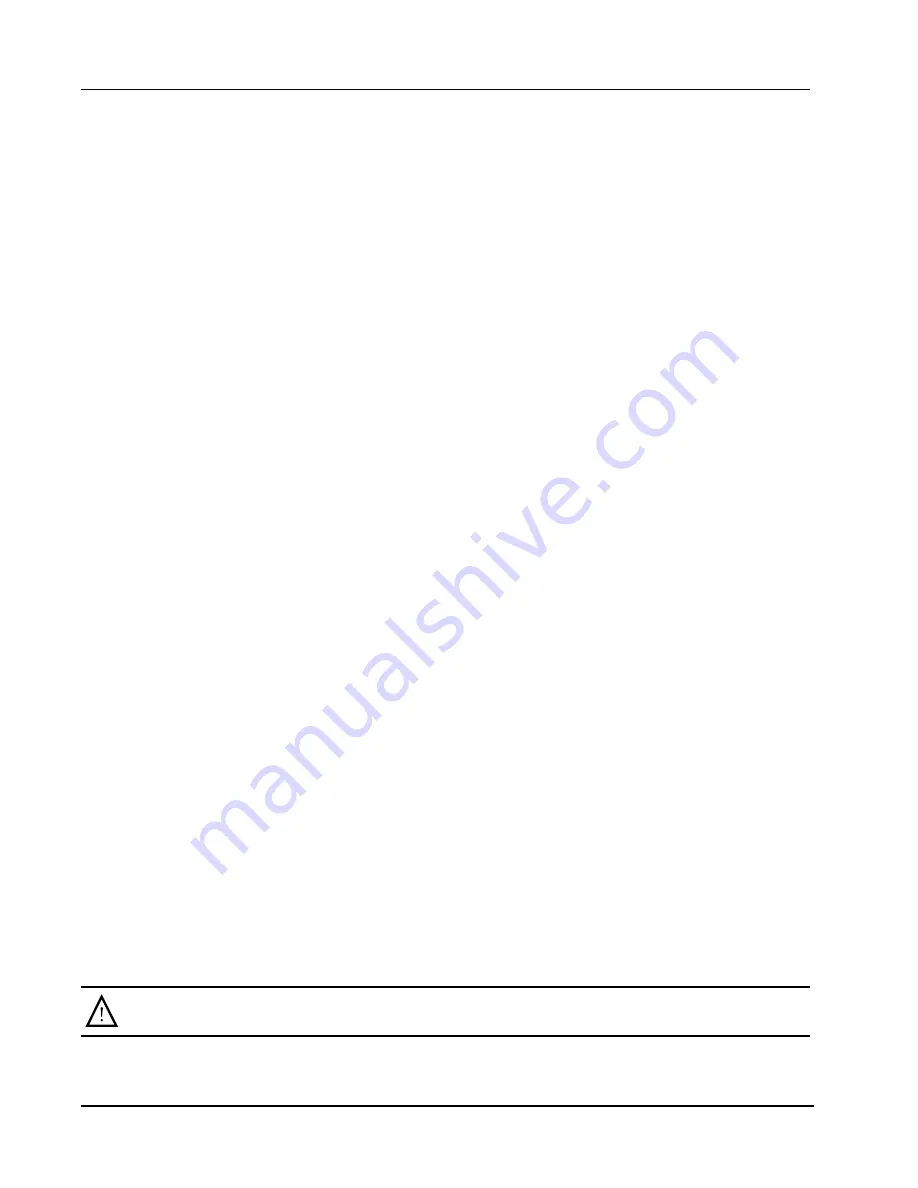
C-16
Appendix C
Scanner
®
2000 microEFM
(BLOCK_ERR) parameter for possible causes.
Remember to check the mode of the resource block. If it is in OOS mode, all other blocks will automatically
be placed in OOS mode as well.
The block error parameter provides an overview of hardware and software erors. It is effective in tracing a
wide variety of errors including block configuration errors, link configuration errors, fault state forced, need
for maintenance, input/output/memory failure, and lost data.
If the error is defined as a block configuration error, check that all parameters in the block with an invalid
default value have been configured. Check that all limit parameters are within the range established by the
scaling parameter. Changing an engineering unit can cause a configuration error if it causes some values to go
out of range.
Resource State
Another good early checkpoint is in the resource block. The Resource State (RS_STATE) parameter shows
the status of the control strategy. If the Resource State is Failure, a memory failure or other hardware failure
has been detected.
Transducer Block Error
The transducer error (XD_ERROR) parameter reports errors that are unique to the Scanner 2000. It displays
only one error at a time, and when multiple errors are present, it displays only the highest priority errror. For
a list of common transducer errors, their descriptions, and tips for identifying the cause, see the
F
oundation
™
Fieldbus Protocol Manual for Scanner 2000.
Communication Faults
When a communication fault occurs, use the configuration tool to determine if it affects a single device or
the entire network. If a device fails to communicate, it will be removed from the live list displayed in the
configuration tool.
Common checkpoints include:
• Check continuity of connections. Measure resistances to eliminate a short circuit as the cause.
• Confirm voltage levels. If the supply voltage at the device is below 9 VDC, the device may not operate
normally. Possible causes may include
– voltage drop due to poor connections in junction boxes or at the device
– too many devices on a network
• Check for noise sources.
Maintenance
Instructions are provided below for replacement of the main board, fieldbus interface board, or fieldbus
module. For all other maintenance, see
Section 5—Scanner 2000 Maintenance, page
.
WARNING: Before servicing the Scanner 2000, disconnect all power sources/signal sources or
verify that the atmosphere is free of hazardous gases.
Summary of Contents for Scanner 2000 microEFM
Page 1: ...NUFLO Scanner 2000 microEFM Hardware User Manual Manual No 9A 30165023 Rev 10 ...
Page 26: ...26 Section 1 Scanner 2000 microEFM ...
Page 104: ...A 18 Appendix A Scanner 2000 microEFM ...
Page 106: ...B 2 Appendix B Scanner 2000 microEFM ...