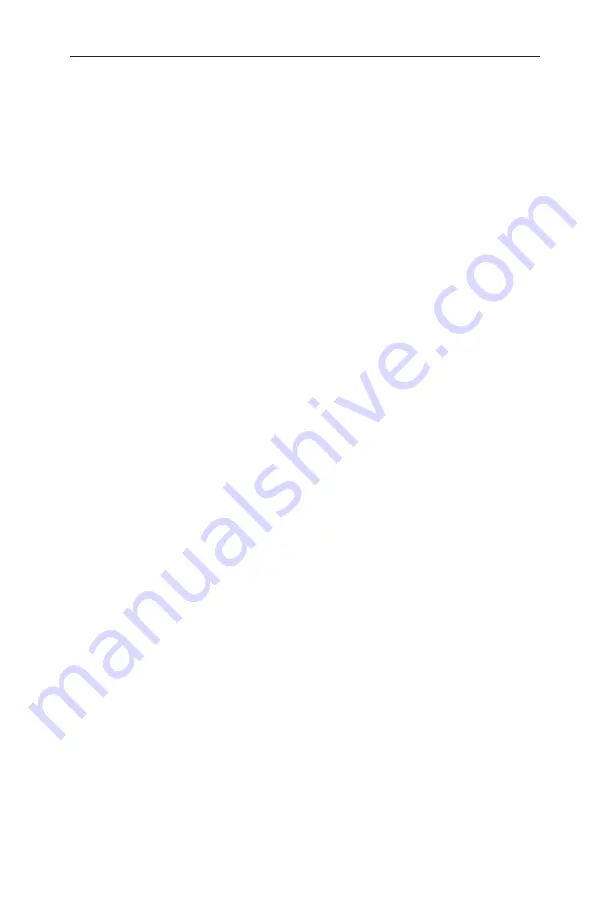
29
Model 764 Differential Pressure Transmitter
Section 4
Removal of the Barton Style Connector Assembly
A special connector tool is required for removal of the Barton style connector
assembly, and is available from Cameron (Part No. 9A-0764-1174B).
To remove the Barton style connector assembly, perform the following steps.
1. Remove the transmitter from service and de-energize it.
2. Remove the transmitter cover (see procedure on
page 25
).
3. Disconnect red and black signal leads from the transmitter circuit board
(TB 1-7 and TB 2-6) as shown in Figure 4.3,
page 30
.
4.
Loosen or remove the two mounting screws on the Zero and Span mount
-
ing bracket to provide additional room for the lead wires.
5.
Insert the connector tool (Part No. 9A-0764-1174B) into the transmitter
conduit hub opening and carefully unscrew and remove the connector as
-
sembly (connector and two O-rings) as shown in Figure 4.3,
page 30
.
Installation of the Barton Style Connector Assembly
To install a Barton style connector assembly, perform the following steps:
1. Mate the connector tool (Part No. 9A-0764-1174B) to the connector as
-
sembly as shown in Figure 4.3,
page 30
.
2. Install two O-rings onto the threaded end of the connector assembly.
Lightly lubricate the threads and O-rings with Dow Corning High
Vacuum Grease.
3. Screw the assembly into the transmitter conduit hub opening.
4.
Replace the two mounting screws in the Zero and Span mounting bracket
and tighten.
5.
Connect the red and black signal leads of the connector assembly to the
transmitter circuit board (TB 1-7 and TB 2-6) as shown in Figure 4.3,
page 30.
6.
Install new O-rings into the grooves of the transmitter cover. Lightly
lubricate the O-rings with Dow Corning High Vacuum Grease.
7.
Replace the transmitter cover (see procedure on
page 25
).