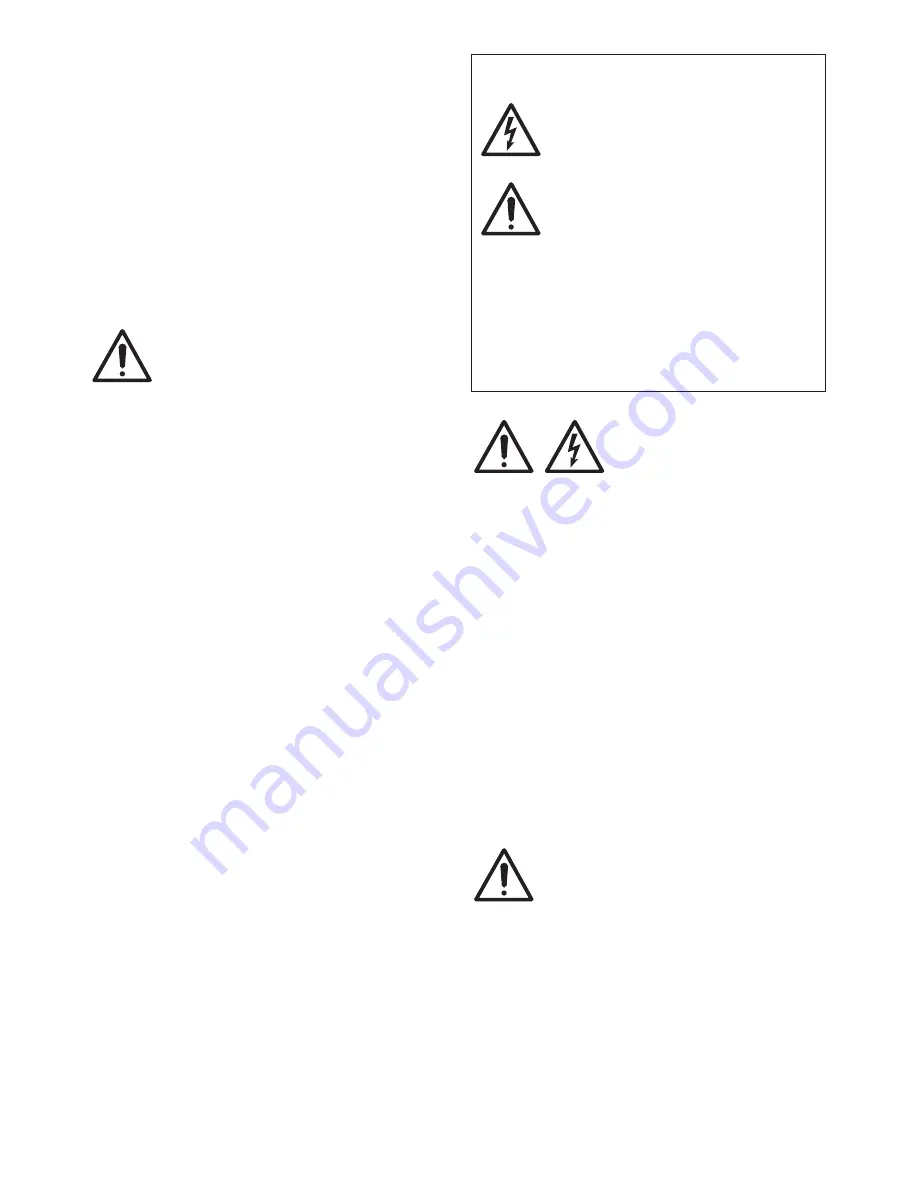
8
5. Starting
With a three-phase power supply make sure
the direction of rotation is correct.
Before installation, momentarily start the motor to
check through the suction opening that the
rotation of the impeller is as shown by the arrow
on the pump. Otherwise disconnect electrical
power and reverse the connections of two phases
in the control box.
Operation with wrong direction of rotation will
cause vibration and loss of delivery capacity.
Reverse rotation can also demage the
mechanical seal.
When in doubt, take the pump out of the water
and check rotation of the impeller by sight.
Never introduce fingers in the
suction opening
unless it is absolutely
certain the electric power has been
disconnected (that the pump cannot be
accidentally switched on) and the impeller has
stopped rotating completely.
The motors with supply current directly
switched by thermally sensitive switches can
start automatically.
Never take the pump out of the water while the
pump is still operating.
Avoid running dry.
Construction with float switch:
the float switch, connected directly to the pump,
controls starting and stopping.
Check that the float switch is free from any obstacle.
If necessary, adjust the float-switch cable (secure
the length with screw 96.09).
Execessive cable length may cause the motor to
overheat and the pump to run dry.
Construction without float switch:
start the pump only if immersed at least 250 mm (GX
40) or 180 mm (GM 50) in the liquid to be raised.
6. Maintenance
Under normal operating conditions the pump will
not require maintenance.
If freezing may be expected while the pump re-
mains inactive and it is not submersed at a safe
depth, remove the pump from the water and
leave in a dry place.
If the pump is temporarily used with incrusting
liquids
(prone to crystallization or liquids with
particles that solidify when exposed to air in
stagnant conditions)
or water containing
chloride,
flush the pump briefly with water
immediately after use to remove any deposit.
If the pump has not been used for a long time and
does not start or gives no water (but electrical
connections are in order), the pump must be
removed from the water and checked to see if it is
choked by any foreign matter or blocked by
sediment, deposits or any other cause.
INSTRUCTIONS FOR SAFETY, HYGIENE AND
HEALTH PROTECTION AT WORK.
Disconnect electrical power before
any servicing operation and make
sure the
pump
cannot
be
accidentally switched on.
The pump may have been immersed
in hazardous substances or products
emanating toxic gases, or may be
located in an environment which is
toxic due to other reasons; make sure all
necessary precautionary measures are taken
to avoid accidents.
Any pumps that require inspection/repair
must be drained and carefully cleaned inside
and outside before dispatch/submission.
Hose down all accessible parts with a jet of water.
In order to avoid the risk of
mechanical or electrical injury
all portable pumps should be
securely isolated from electrical
power supply prior to their relocation.
7. Dismantling
For disassembly and reassembly, refer to the
cross-section drawing.
To inspect the impeller (28.00), to clean the
internal parts and to check whether the impeller
turns freely when moved by hand, remove the
nuts (GX) or the screws (GM) (12.20) and casing
cover (12.00).
To dismantle the impeller remove the nut (28.04).
Use the threaded dismantling holes to remove
the
GMV
impeller.
Others parts should not be dismantled.
The pump function can be impaired by erro-
neous procedure or tampering with internal parts.
If the mechanical seal (36.00) and the oil chamber
are to be inspected, follow these instructions.
CAUTION: there may be slight
pressure in the oil chamber.
Care must be taken to avoid a sudden
spurting of oil.
Once the plug (14.46) with washer (14.47) have
been removed, adjust the hole to the downward
position and empty the chamber completely.
Do not dispose of the waste oil in the
enviroment.
The mechanical seal (36.00) can be inspected by
removing the impeller key (28.20), the screws
(14.24) and the pump casing (14.00).
When re-filling with fresh oil, remember that the
chamber must not be completely filled; a
sufficient quantity of air must remain inside it in
order to compensate for overpressure caused by