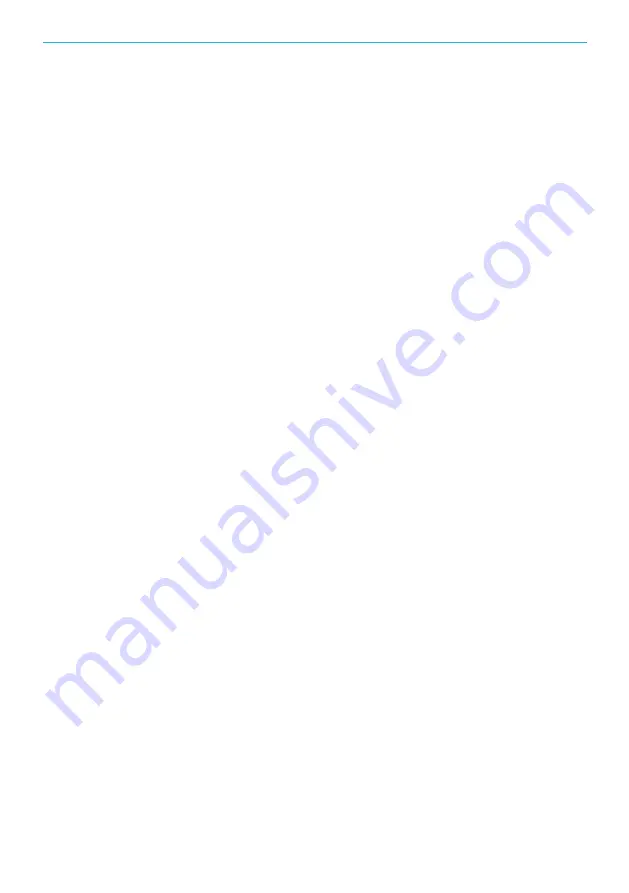
Operating Instructions
Uniprep 7 Rotary Scraping Tool
05
Pipe Preparation
1. Inspect the end of the pipe to be scraped to ensure it has no
damage or deep scores and that it is externally clean.
2. Check that the pipe is round. Ovality should be reduced where
possible. (Re-round with re-rounding tool if required).
3. Check that the end has been cut reasonably square.
4. Measure the insertion depth of the fitting and add on a minimum of
25mm (35mm recommended) to give a scraping witness. Mark the
distance (from furthest protruding face of pipe end) and cross hatch
that length of pipe with suitable pen such as white china pencil.
Using the Scraping Tool
Firstly, check the expanding body, ensure all parts are present and
nothing is loose or hanging off the tool.
1. Insert expanding body of the tool into pipe making sure the feet are
past the point of any pipe end regression with the Feed Screw collet
outermost.
2. Using supplied hex spanner locate on Feed Screw Collet expand the
body by turning anti-clockwise until very tight, aiming to leave the
Feed Screw Drive knob uppermost. Once tight, remove the spanner.
3. Quarter turn the feed screw drive knob to raise and disengage the
thread driver (if not already in position). Next fully insert the feed
screw and engage the feed screw driver by turning the feed screw
drive knob a quarter turn. Unscrew the crank arm T screw ready to
receive the scraper arm.
4. Raise the crank handle and insert the scraper arm. (Note it is highly
recommended to have the crank handle and scraper arm together
in the same orientation to prevent injury from rotation of the tool)
Lower the scraper arm until the scraper tip is approximately 6-10mm
from the pipe surface and lock in position with the crank arm T
screw.
5. Mark the position of the blade tip on the pipe to identify the point
when the telescopic scraper arm is retracted. This mark is used to
identify when the feed screw is nearing the end of the thread and to
prevent the scraper arm falling out and/or being damaged.
03. Operation