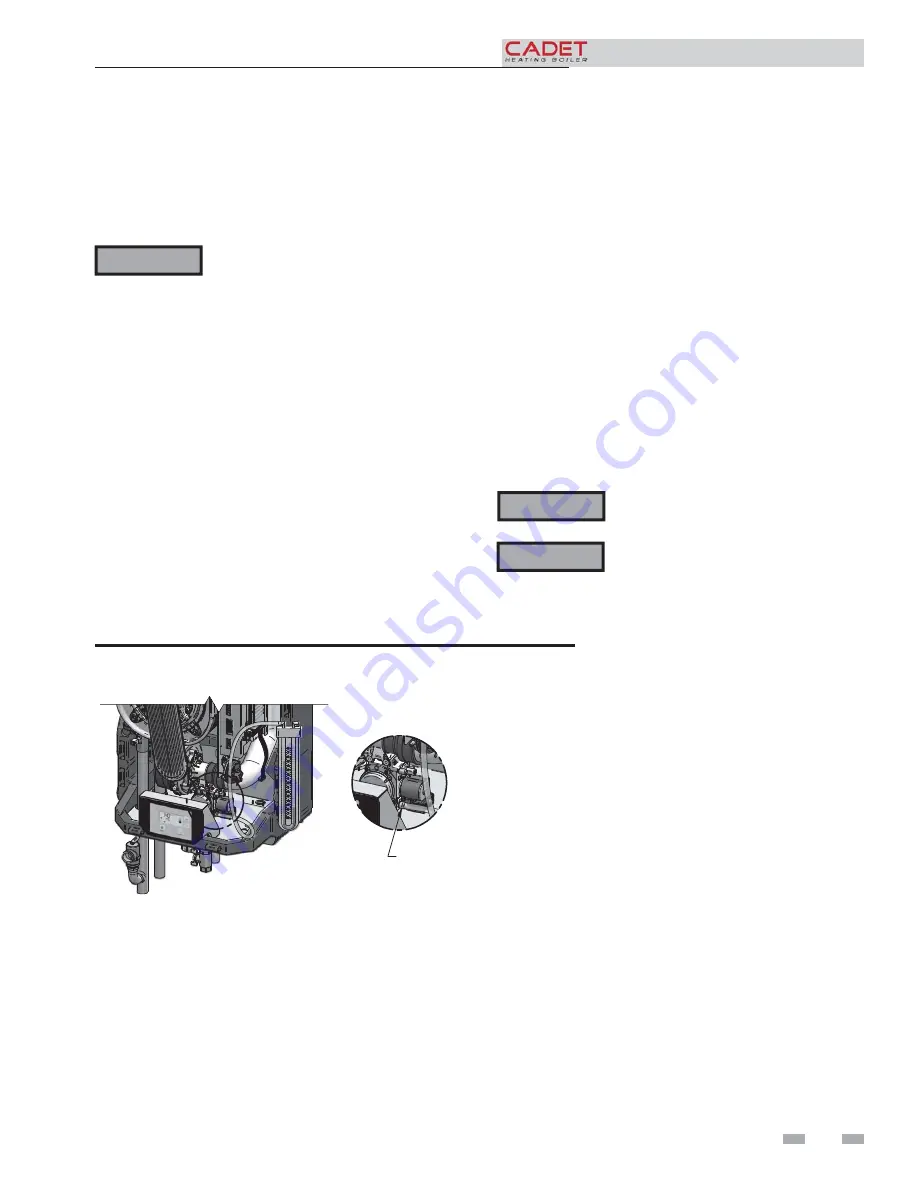
45
7
Gas connections
(continued)
WARNING
When re-tightening the set screw, be
sure to tighten securely to prevent gas
leaks.
Do not check for gas leaks with an open
flame -- use the bubble test. Failure to
use the bubble test or check for gas leaks
can cause severe personal injury, death,
or substantial property damage.
14. Turn on the gas supply at the manual gas valve.
15. Turn ON power at source.
16. Adjust the temperature set point on the control panel
of the boiler control module to the desired
water temperature so the appliance will call for heat.
17. Check burner performance by cycling the system while
you observe burner response. The burner should
ignite promptly. Flame pattern should be stable. Turn
system off and allow burner to cool, then cycle burner
again to ensure proper ignition and flame
characteristics.
Gas Pressure
The gas pressure must remain between 4 inches w.c. (natural),
8 inches w.c. (LP) minimum and 14 inches w.c. (natural and
LP) maximum during stand-by (static) mode and while in
operating (dynamic) mode. If an in-line regulator is used, it
must be a minimum of 10 feet from the Cadet heating boiler. It
is very important that the gas line is properly purged by the gas
supplier or utility company. Failure to properly purge the lines
or improper line sizing, will result in ignition failure.
The problem is especially noticeable in NEW LP installations
and also in empty tank situations. This can also occur when
a utility company shuts off service to an area to provide
maintenance to their lines.
Gas valve replacement
The gas valve MUST NOT be replaced with a conventional gas
valve under any circumstances.
DETAIL
LOOSEN SET SCREW ONE (1)
FULL TURN THEN PLACE
TUBING OVER PRESSURE TAP
IMG00244
Figure 7-3 Inlet Gas Supply Check
DO NOT adjust gas valve outlet pressure.
The gas valve is factory-set for the correct
outlet pressure. This setting is suitable
for natural gas and propane, requiring
no field adjustment. Attempting to
alter the gas valve outlet pressure could
result in damage to the valve, causing
potential severe personal injury, death, or
substantial property damage.
Failure to follow all precautions could
result in fire, explosion, or death!
WARNING
WARNING
Installation & Service Manual
12. Shut off the gas supply at the manual gas valve in the gas
piping to the appliance.
13. Remove the manometer from the pressure tap on top of
the gas valve. Re-tighten the set screw inside the pressure
tap.