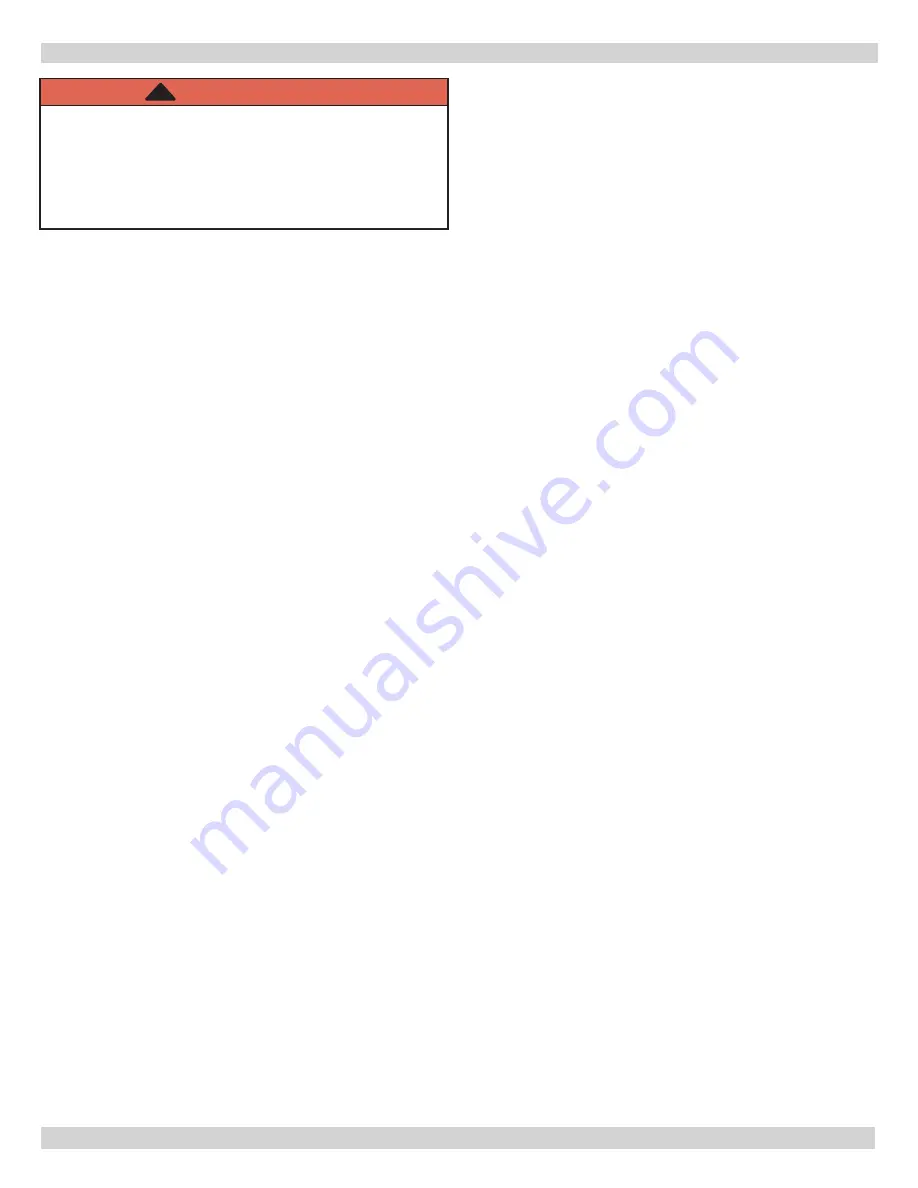
27
IM-BW4-5-02
[240013014 Rev. B [12/15/2020]
Annually
:
Recommend flue passages, combustion
chamber area (target wall, fire door insulation,
durablanket), burner adjustment, control operation, and
boiler seals (fire door gasket or silicone seal, cast iron
sectional seals, flue collector) be checked once each year
by trained Service Technician.
Before The Start Of Each Heating Season
(or when
system has been shut down for extended periods of time)
recheck whole system for water, oil, and vent piping leaks.
Replace or patch any leaks or faulty seals.
Vent Pipe:
Visually inspect entire venting system once a
month for any signs of leakage, deterioration, or soot build
up. If vent pipe shows any signs of leaking or deterioration,
replace it immediately. If it shows any signs of soot
build up, clean vent pipe and have burner settings and
combustion checked by trained Service Technician.
Safety Relief Valve:
Valve should open automatically
when system pressure exceeds pressure rating (usually 30
psi) of safety relief valve. Should valve ever fail to open
under this condition, shut down the system. Drain system
until system pressure is reduced below safety relief valve
pressure rating. Contact Service Technician to replace the
valve and inspect heating system to determine cause, may
indicate equipment malfunction. Safety relief valve should
be tested monthly during heating season. Prior to testing,
make certain discharge pipe is properly connected to valve
outlet and arranged so as to contain and safely dispose of
boiler discharge. Hold trip lever fully open for at least five
seconds in order to flush free any sediment that may lodge
on valve seat. Permit valve to snap shut. Refer to valve
manufacturer’s instructions packaged for more details.
Conventional Expansion Tank
:
Tank may become
water logged or may receive excess air. Frequent automatic
opening of safety relief valve indicates water logging. High
boiler temperature accompanied by unusually low radiation
unit temperature (and “knocking” noises) indicates excess
air in the tank. To correct either condition, close valve
between boiler and tank. Drain tank until empty. Check all
tank plugs and fittings, tighten as necessary. Open valve
between boiler and tank. Water will rise to normal height in
tank if system has automatic fill valve, otherwise manually
refill system.
Diaphragm Expansion Tank
:
Tank may become
water logged. Frequent automatic opening of safety relief
valve indicates water logging. High boiler temperature
accompanied by unusually low radiation unit temperature
(and “knocking” noises) indicates excess air in the tank. To
correct this condition, replace diaphragm expansion tank.
Water System:
If system is to remain out of service
during freezing weather, drain it completely (water left in
system may freeze and will crack pipes and/or boiler).
Tankless Coil (Or Cover Plate) Gasket:
Gasket
should be checked at least twice year for leakage, replace if
necessary. If gasket is replaced, make sure that when coil
plate (or cover plate) is reattached, ten nuts are torqued
in alternating pattern to insure equal force is applied to
entire gasket creating good seal. Nuts should be torqued so
gasket does not squeeze out from behind the plate.
Oil Burner:
Oil burner maintenance is listed in this
manual under “Operating The Boiler”.
Never burn garbage or paper in the unit, never leave
combustible material around it.
MAINTENANCE
Oil Burner Maintenance
:
Perform following
preventative maintenance annually, preferably prior to
heating season. Refer to burner manual provided with
boiler.
1.
Fuel Filter
Replace to prevent contaminated fuel from
reaching nozzle. Partially blocked fuel filter can cause
premature failure of fuel pump.
2.
Fuel Pump Unit
Replace pump screen and clean pump
unit to maintain fuel delivery to nozzle.
3.
Ignition Electrodes
Clean and adjust per
manufacturer’s recommendations, to maintain reliable
ignition of oil.
4.
Nozzle
Replace to maintain safe and reliable
combustion efficiency. Replace with nozzle as required
in charts located in this manual.
5.
Fan and Blower Housing
Must be kept clean, free of
dirt, lint and oil to maintain proper amount of air fuel
requires to burn.
6.
Check Final Burner Adjustments.
If any component parts must be replaced, always use parts
recommended by burner manufacturer.
WARNING
Burn, scald hazard. Some maintenance tasks
require draining the boiler. Verify boiler is cool and
at zero pressure before draining. Verify boiler is
appropriately drained before removing relief valve,
control well, tankless coil etc. Failure to follow these
instructions could result in death or serious injury.
!