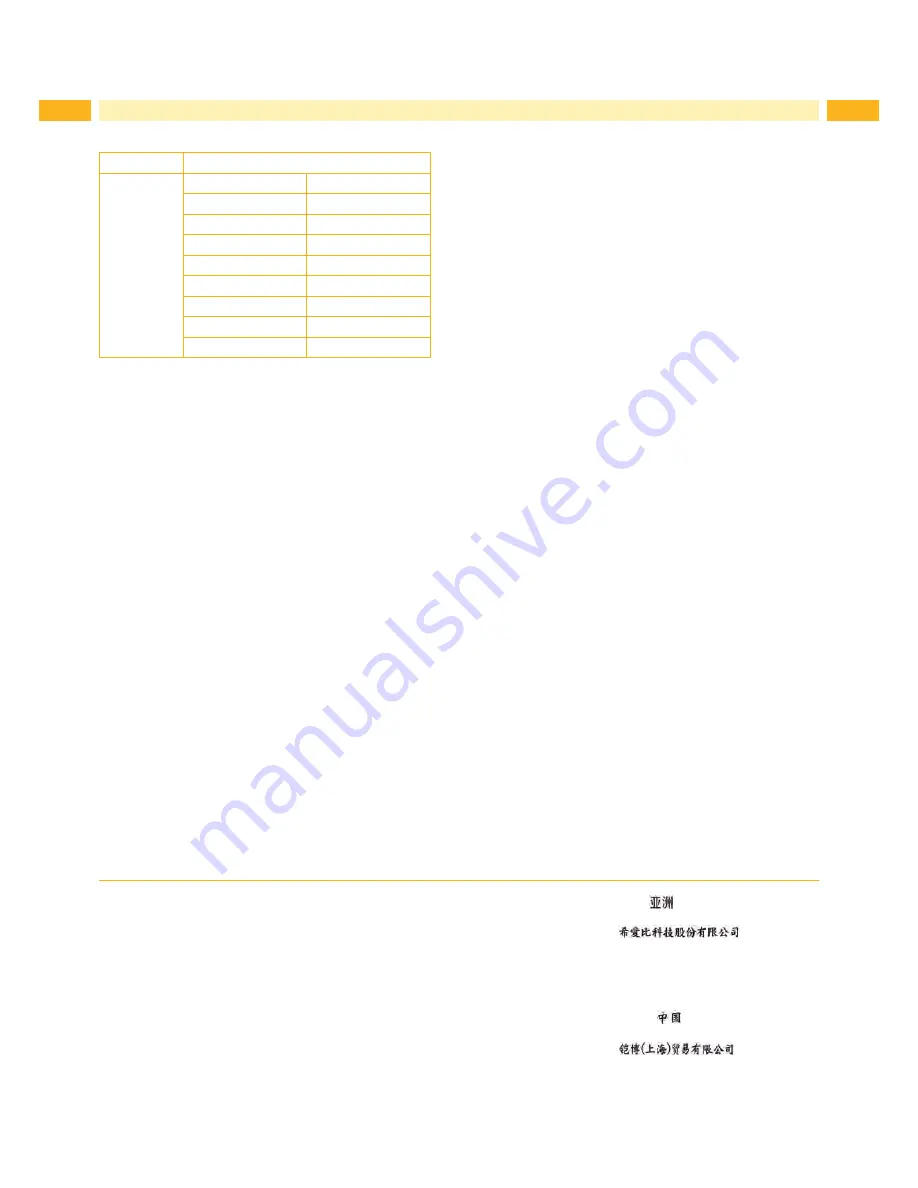
2
2
Family
Type
MACH 4S
-
MACH 4.3S/200B
-
MACH 4.3S/200P
-
MACH 4.3S/200C
MACH 4S/300B
MACH 4.3S/300B
MACH 4S/300P
MACH 4.3S/300P
MACH 4S/300C
MACH 4.3S/300C
MACH 4S/600B
-
MACH 4S/600P
-
MACH 4S/600C
-
Edition:
12/2017 - Part No. 9003102
Copyright
This documentation as well as translation hereof are property of
cab Produkttechnik GmbH & Co. KG.
The replication, conversion, duplication or divulgement of the
whole manual or parts of it for other intentions than its original
intended purpose demand the previous written authorization by
cab.
Editor
Regarding questions or comments please contact cab
Produkttechnik GmbH & Co. KG.
Topicality
Due to the constant further development of our products
discrepancies between documentation and products can occur.
Please check www.cab.de for the latest update.
Terms and conditions
Deliveries and performances are effected under the General
conditions of sale of cab.
Service Manual
for the following product
Germany
cab Produkttechnik
GmbH & Co KG
Postfach 1904
D-76007 Karlsruhe
Wilhelm-Schickard-Str. 14
D-76131 Karlsruhe
T49 721 6626-0
T49 721 6626-249
www.cab.de
[email protected]
France
cab technologies s.a.r.l.
F-67350 Niedermodern
Téléphone +33 388 722 501
www.cab.de/fr
[email protected]
USA
cab Technology Inc.
Tyngsboro MA, 01879
Phone +1 978 649 0293
www.cab.de/us
[email protected]
Asia
cab Technology Co., Ltd.
Junghe, Taipei, Taiwan
Phone +886 2 8227 3966
www.cab.de/tw
[email protected]
China
cab (Shanghai)Trading Co., Ltd.
Phone +86 21 6236-3161
www.cab.de/cn
[email protected]
Representatives in other countries on request