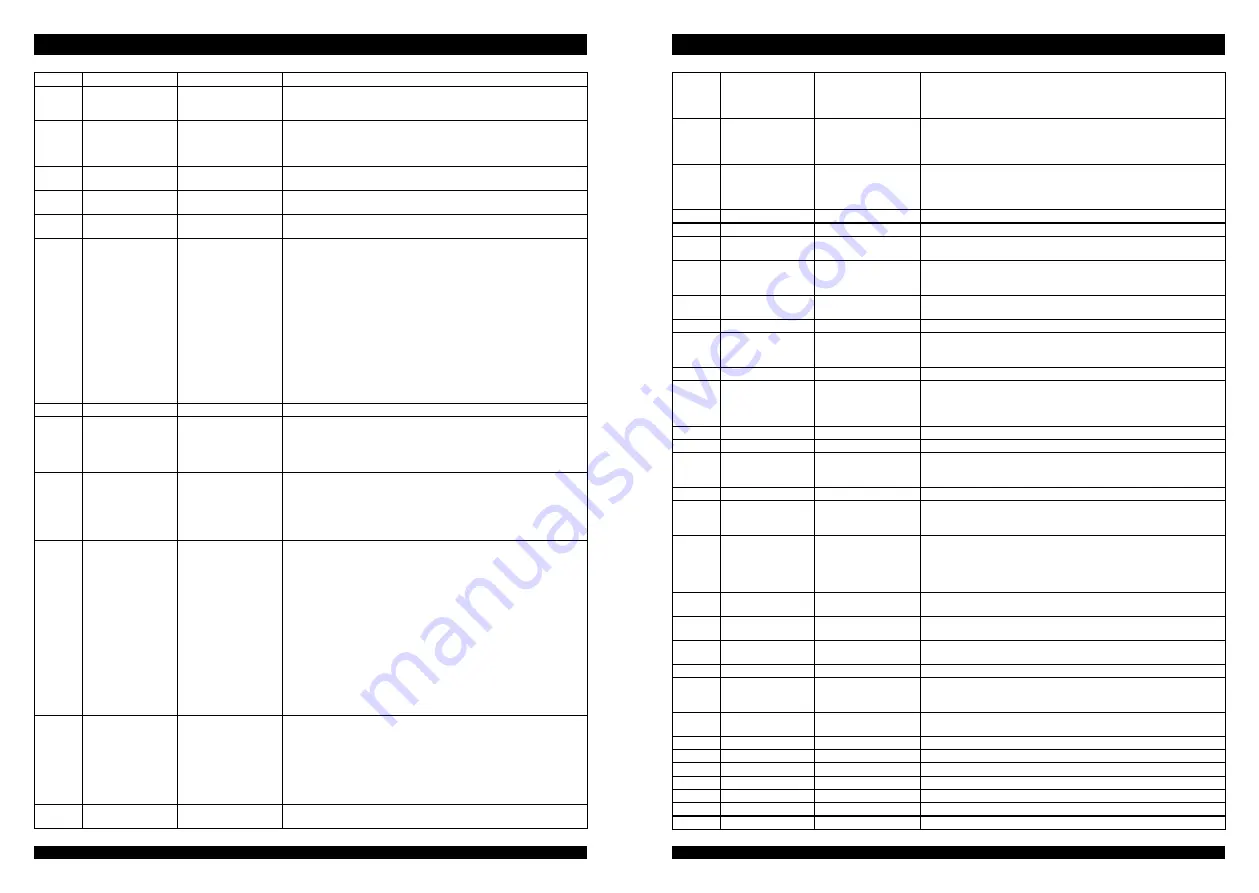
MAINTENANCE
OPERATOR MANUAL
43
P20PS
44
OM-P20PS2019001-EN
Fault code
Fault
Fault name
Solutions
06A39
SERIAL ERROR #1
Slave contactor does not
receive the information of main
contactor from serial port
Replace the controller;
06A8
EEPROM KO
Memory is damaged
Forklift does not travel. Parameter storage becomes faulty so that forklift stops operation.
Operate the key switch for several times. If the fault still exists, replace the logic card. If the
fault disappears, parameters previously stored have been replaced by wrong parameters. It
is imperative to set the parameters again.
06A15
LOGIC FAILURE #4
Logic card fault #4
The output VW-VV of the voltage amplifier exceeds 2.2V-2.8V, and the controller needs to
be replaced; (Steering controller)
06A14
LOGIC FAILURE #3
Logic card fault #3
The output VU-VV of the voltage amplifier exceeds 2.2V-2.8V, and the controller needs to be
replaced; (Steering controller)
06A13
LOGIC FAILURE #2
Logic card fault #2
The voltage between W and V does not meet the requirements, and the controller needs to
be replaced; (Steering controller)
06A12
LOGIC FAILURE #1
Logic card fault #1
Faults caused by under-voltage or over-voltage protection. In 24V system, the controller
detects a voltage above 45V or below 9V; In 48V system, the controller detects a voltage
above 65V or below 11V.
Possible causes:
1.Whether there is short circuit in the circuit system, such as DC-DC, brake coil, etc., or
whether the controller input power supply is in good contact. (Driving controller)
2.Whether the battery voltage is over low or over high. (Driving controller)
3.Check if the power cable above the terminals such as B+, B, main contactor is tight. (Driving
controller)
4.Whether the calibration parameter of controller voltage is consistent with the actual
voltage. (Driving controller)
5.Fault with the hardware circuit protected by over-voltage on the logic card. Replace the
controller. (Driving controller)
6.The voltage between W and U does not meet the requirements, and the controller needs
to be replaced; (Steering controller)
06A9
VMN NOT OK
VMN fault
Replace the controller;
06A20
MAIN CONT. OPEN
MAIN CONT. OPEN
The coil of main contactor has been energized by the logic card, but the contactor does not
engage. Possible cause:
1.The contactor has mechanically become faulty, or its contacts get stuck
2.The contacts of contactor cannot make securely
3.If the contactor operates normally, replace the controller.
06A5
STBY I HIGH
Standby current is high
Checks whether the motor current is zero via controller in the vehicle standby state. If it is
not zero, this fault occurs, stop the vehicle immediately. Possible cause:
1.One end of the terminal is connected directly to another load rather than to a drive motor,
such as a lift motor.
2.Current sensor or logic card damaged. Replace the logic card first. If the fault persists,
replace the power part.
。
06A10
HIGH
TEMPERATURE
Temperature overheating
When full power is allowed, the temperature of the controller exceeds 85 °C (this
temperature is related to the parameter "MAXIMUM CURRENT"). Corresponding relation is
as follows:
Parameter setting
Alarm temperature
MAXIMUM CURRENT=50%
96°C
MAXIMUM CURRENT=60%
94°C
MAXIMUM CURRENT=70%
92°C
MAXIMUM CURRENT=80%
90°C
MAXIMUM CURRENT=90%
88°C
MAXIMUM CURRENT=100% 86°C
At this time, the maximum current of the controller decreases with increasing temperature.
When the temperature is 105 °C, the controller current is reduced to 0.
If the chopper is cold state, the fault occurs:
1.The logic card temperature calibration parameters are incorrect. Check the parameters.
2.Controller internal temperature sensor fault,
3.Check the temperature sensor itself for damage.
06A48
MOTOR TEMPERAT.
Motor temperature high
1.If the motor temperature digital switch is turned on, or analogue signal exceeds the cutout
value, then the fault results.
2.When motor temperature rises to 120°C, the controller will display the warning. The forklift
still can travel but the maximum current is reduced with the forklift performance degraded.
When the motor temperature reaches 125°C, the motor stops working. In this case, action
shall be taken to cool the motor.
3.The fault still exists when the motor cools, check the line. If all have no faults, replace the
controller.
06A1
HIGH CURRENT
Current over high
1
、查看转向控制器是否与电机匹配;
2
、更换控制器
06A4
POWER FAILURE #3
Power fault #3
1.Check if the controller fuse is normal;
2.Check if power supply cable is firmly connected to the controller;
3.Check if the controller V phase wire is connected properly;
4.Replace the controller;
06A3
POWER FAILURE #2
Power fault #2
1.Check if the controller fuse is normal;
2.Check if power supply cable is firmly connected to the controller;
3.Check if the controller U phase wire is connected properly;
4.Replace the controller;
06A2
POWER FAILURE #1
Power fault #1
1.Check if the controller fuse is normal;
2.Check if power supply cable is firmly connected to the controller;
3.Check if the controller W phase wire is connected properly;
4.Replace the controller;
06A26
BAD ENCODER SIGN
Encoder phase sequence error Change encoder A, B phase;
06A45
STEER SENSOR KO
Dual potentiometer fault
Check the wiring and output of the two-way steering potentiometer.
06A0
STEER HAZARD
Steering angle exceeds limit
1.Reduce the steering angle and turn the key switch to “ON”;
2.Change the angle parameter setting inside the steering controller;
06A53
INPUT ERROR #1
Advanced steering controller
CAN#4 has a voltage input
higher than 12V
Check if the CAN#4 cable is correct;
06A56
SL CENTERING
Swing angle of self centering
is out of range
Replace the controller;
06A55
SL EPS NOT ALL.
Self centering is not completed Replace the controller;
06A54
CAN BUS KO SL.
Slave contactor does not
receive any CAN information
from main contactor
Replace the controller;
06A54
06A52
MICRO SLAVE #8
The encoder of the main
microprocessor is inconsistent
with the encoder of the slave
microprocessor
Replace the controller;
06A51
MICRO SLAVE #3
06A44
CLOCK PAL NOT OK
Clock error
Replace the controller;
06A50
STEPPER MOT MISM
Frequency of stepper motor Q
and D line and voltage values
do not match
Replace the controller;
;
06A49
MOTOR LOCKED
Steering motor stalling
Steering motor continuous maximum current time exceeds 1s;
06A40
MICRO SLAVE #4
Steering motor current is
opposite to the command
direction
Replace the controller;
06A47
FB POT LOCKED
Feedback value of steering
potentiometer locked
1.Check if the feedback angle potentiometer has mechanical looseness;
2.Check if there is a mechanical limit;
3.Check if the feedback angle potentiometer reaches its own limit point;
4.If the fault occurs in the opposite direction of the steering wheel during installation, adjust
the direction of the steering wheel;
06A46
JERKING FB
Steering potentiometer voltage
changes too much
Replace the feedback potentiometer;
06A0
EMERGENCY
Emergency reverse
After completing the emergency reverse, engage the interlock switch again and the fault
disappears.
06A43
CURRENT GAIN
Controller maximum current is
not controlled
Replace the controller;
06A42
NO SYNC
06A41
SLAVE COM. ERROR
Main contactor does not
receive the information of
slave contactor from serial port
Replace the controller;
06A38
POSITION ERROR
Position error
1.Check if the steering motor encoder A and B phases are loosely connected;
2.Check if the steering motor A and B phases receive interference;
06A31
LOOK. FOR PATH
06A32
PATH OUT
06A33
LATERAL OUT
06A34
ANGLE
06A35
LOSING PATH
06A36
LOSING STRAIGHT
06A30
WRONG ANT. RECEP
Summary of Contents for P20PS
Page 1: ...P20PS OPERATOR MANUAL OM P20PS2019001 EN...
Page 2: ...P20PS OPERATOR MANUAL OM P20PS2019001 EN...
Page 27: ......