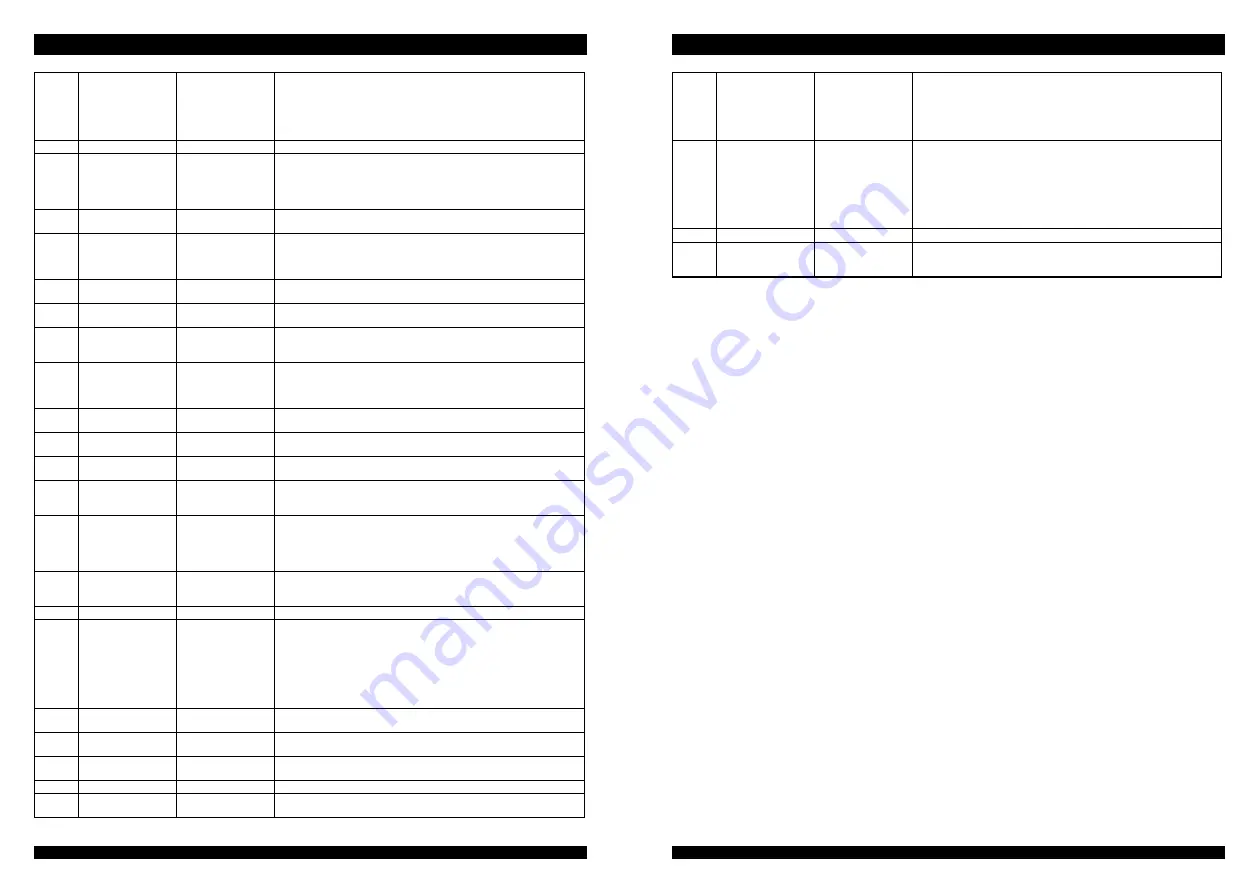
MAINTENANCE
OPERATOR MANUAL
41
P20PS
42
OM-P20PS2019001-EN
02A86 POS. EB. SHORTED
H i g h e n d o f d r i v e o f
electromagnetic brake
provides output earlier than
expected
High end of drive of electromagnetic brake outputs high voltage with the interlock not
engaged.
1.Check whether another high voltage circuit is connected to the high end output connector of
electromagnetic brake;
2.If the high end output connector of electromagnetic brake is not connected but high voltage
still exists, the drive circuit in the controller has already been damaged;
02A80 EMERGENCY
02A8
WATCHDOG#2
Watchdog fault 2
Possible cause: During startup of the forklift, the watchdog circuit has been activated before
the software is initiated. In the standby or operation state, the watchdog signal is invalid (alarm
state).
Fault analysis: The watchdog hardware circuit or microcontroller output section is damaged.
Neither of the two cases is associated with external components. Replace the controller.
02A75 CONT. DRV. EV
EV drive of the controller is
inoperable
EV drive of the controller is inoperable
02A89 POWER MOS SHORT
Short circuit of the power
MOS tube
Before the main contactor engages, the software can check the power bridge. Convert the
low end power of the MOS tube. Lower the phase voltage to –BATT (lift to +BATT). If the
phase voltage variation does not agree with the command, this fault can occur. Replace the
controller. Replace the controller.
02A74 DRV. SHOR. EV
Short circuit of EV cable
Check whether the low end of EV1/EV2/EV3 is short circuited to B-. If not, it is required to
replace the controller;
02A76 COIL SHOR. EV.
PEV coil fault
Fault with the PEV drive coil. Check whether the PEV drive coil connection or the coil itself
are in good conditions;
02A92 CURRENT GAIN
Fault with current gain
Maximum current gain is the factory set value. It indicates that the maximum current
adjustment procedure has not yet been initiated.
Solution: ZAPI technician correctly sets the current gain parameter.
02A96 ANALOG INPUT
Analogue signal input fault
This fault occurs when all analogue signals are converted into the same value by the A/
D converter, with delay exceeding 400ms. This function is used to detect fault with the A/D
converter or conversion of analogue signal
Fault analysis: If this fault persists, replace the controller.
02A64 TILLER ERROR
Interlock mismatches H&S
input
Replace the controller;
02A47 EVP2 NOT OK
NAUX2 input voltage is
outside the range
Check whether NAUX2 input voltage is within the range. If not, re-calibrate the maximum and
minimum of NAUX2, and turn the key switch to “ON” again. This fault will disappear.
02A48 EVP1 NOT OK
NAUX1 input voltage is
outside the range
Check whether NAUX2 input voltage is within the range. If not, re-calibrate the maximum and
minimum of NAUX2, and turn the key switch to “ON” again. This fault will disappear.
02A49 LIFT + LOWER
Faults with lifting and
lowering exist at the same
time
1.Improper operation;
2.Fault with the “LIFT “and “LOWER” switches;
3.Replace the controller;
02A79 PUMP INC START
Oil pump startup sequence
fault
Incorrect oil pump startup sequence. Possible causes:
1.The “LIFT” or “TILT” switch has already at the “ON” position before the forklift is started.
2.Operation sequence error.
3.Incorrect wiring connection.
4.If the fault cannot be eliminated, replace the controller.
02A90 PUMP VACC RANGE
O i l p u m p l i f t s p e e d
regulation sensor signal is
outside the range
1.Upper and lower voltage limits of the lift speed regulation sensor have not been correctly
taken. Move to the “PROGRAM VACC” menu and take them again;
2.Check whether the wiring of the lift speed regulation sensor is correct;
02A27 PHASE KO
Open circuit of U/V/W phase Check whether U/V/W phase is correctly connected.
02A89 PUMP VACC NOT OK
O i l p u m p l i f t s p e e d
regulation sensor fault
Inspection time: idling state
The lift speed regulation sensor voltage is at least 1V higher than the minimum set in the
“PROGRAM VACC” menu for accelerator signal range.
Possible causes:
1.Upper and lower voltage limits of the lift speed regulation sensor have not been taken.
Move to the “PROGRAM VACC” menu and take them again.
2.Lift speed regulation sensor error
3.Controller fault.
02A42 AUX DRIV.OPEN
Fault with drive of auxiliary
output
Drive circuit of auxiliary coil is unable to drive the load. Device itself or drive coil.
02A0
DATA ACQUISITION
Data collection
Activation of this fault indicates data acquisition is under way. Wait data acquisition is
completed.
02A67 NO CAN MSG.
No CAN signal
Fault with CAN communication between steering and towing. Check CAN connection, as well
as version and configuration of software.
02A0
CHECK UP NEEDED
Maintenance interval
Maintenance interval is expired. Maintenance is required.
02A61 THERMIC SENS. KO
Temperature sensor fault
Controller temperature sensor output signal is outside the range. This fault is not related to
external components. Replace the controller.
02A41 WRONG BATTERY
Fault with battery setting
While the forklift is being started, the controller checks whether battery voltage is within the
nominal voltage range.
1.Check whether the “BATTERY VOLTAGE” setting in the “TESTER” agrees with the
indication of the voltmeter. In the case of disagreement, change battery voltage setting to be
the same as the measured value, by using the “ADJUST BATTERY) function.
2.Replace the battery.
02A53 WRONG ZERO
Error of zero voltage
While the forklift is being started, feedback value of high end voltage of VMN is not in the
order of 2.5V. Circuit of the controller is damaged.
Fault analysis: The following checks are recommended.
Check internal connection of the motor.
Check power cable connection of the motor.
Check for drain current between the motor and the forklift housing.
If the motor connection is in good condition, the fault is in the controller interior. Replace the
controller.
02A99 SLIP_PROFILE
Slip fault
“SLIP PROFILE” selection error. Check hardware parameter settings.
02A40
AUX DRIV.SHRT. // all254 Short circuit of auxiliary drive
Short circuit of drive circuit of electromagnetic brake or auxiliary electric brake.
Check for short circuit or low-impedance push-pull output between A16 and –BATT.
Fault with drive circuit of logic card. Replace the controller.
Summary of Contents for P20PS
Page 1: ...P20PS OPERATOR MANUAL OM P20PS2019001 EN...
Page 2: ...P20PS OPERATOR MANUAL OM P20PS2019001 EN...
Page 27: ......