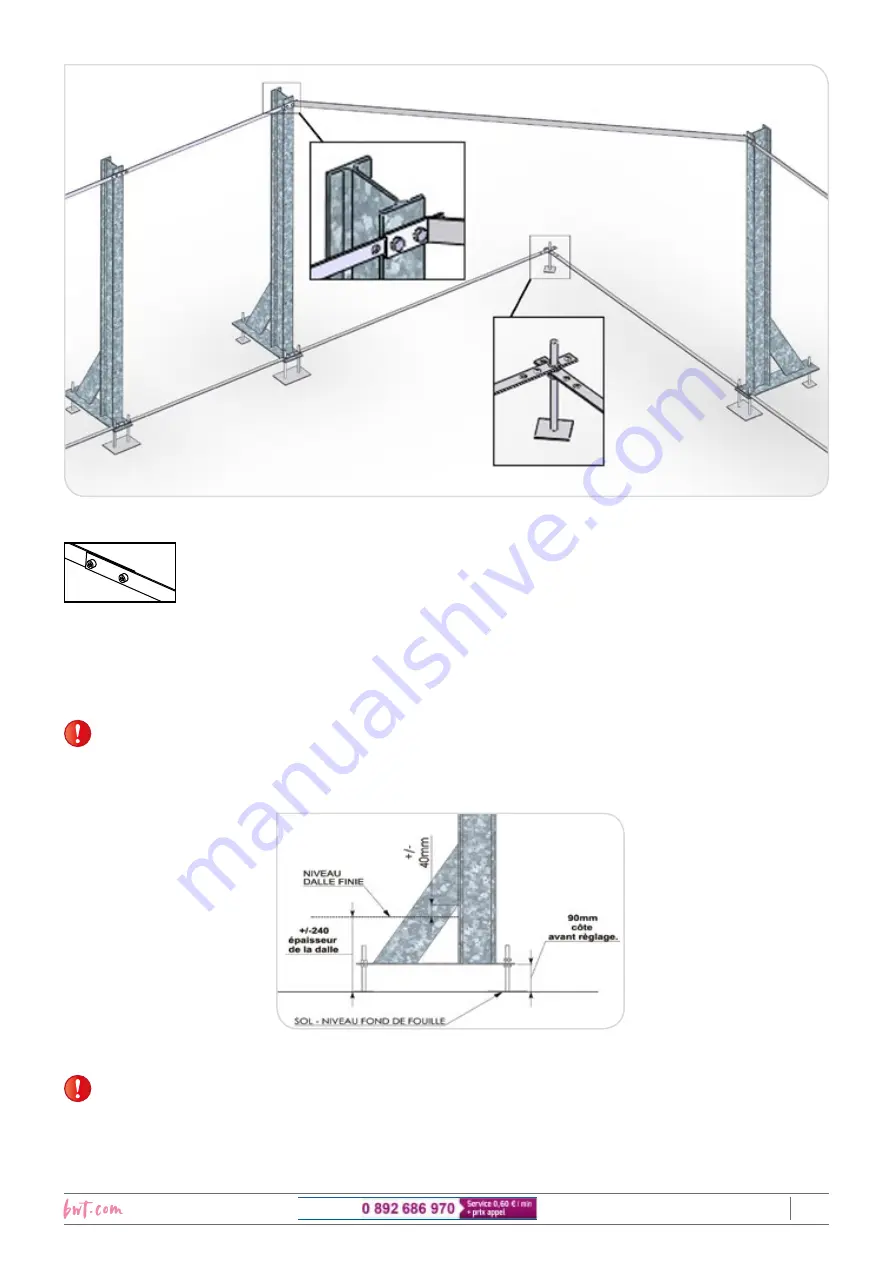
11/48
2019/01 - Indice de révision : A - Code : 97160421
WOODEN POOLS
BWT
myPOOL
HOTLINE
Figure 6 – Top and bottom bars
Depending on the version, the flat metallic bards are delivered as two separate sections
to be bolted together.
Once the metallic structure has been assembled, adjust the position of the posts carefully and check :
•
that the posts are level, straight and perfectly aligned.
•
that the pool diagonals measured at the axis of the corner jacks are equal (
).
For pools1.20 m deep, the slab thickness should be approx 350 mm, disregard the +/- 40 mm
measurement. The measurement before adjustment, 90 mm, is unchanged
.
Figure 7 – Detail of the jack
Take particular care during this stage of the assembly, it will impact subsequent phases and determine
the quality of the pool finish.