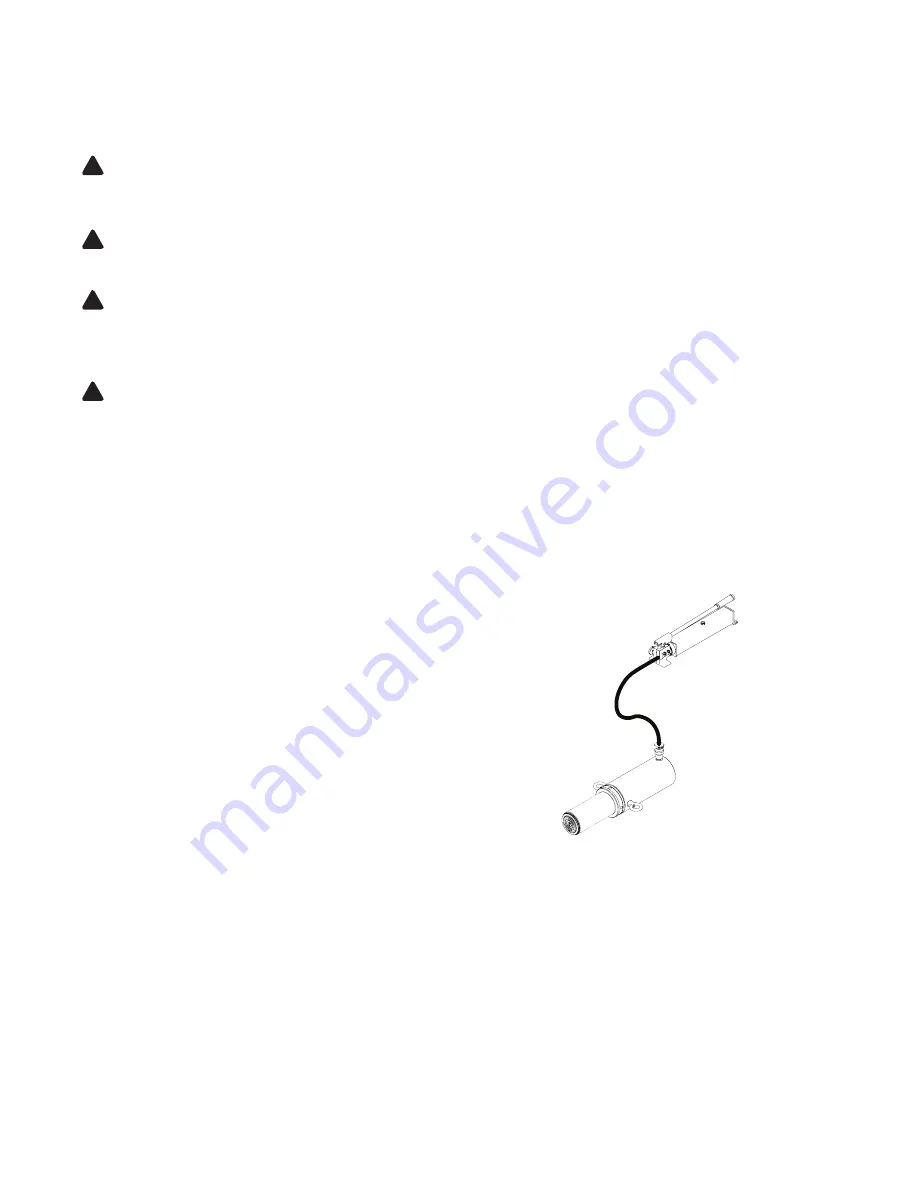
5
Storage
Cylinders should be stored vertically with ram plunger fully retracted
in a dry, protected area, not exposed to corrosive vapor, dust or
other harmful elements. When a cylinder has not been used for
a period of 4 months, it should be connected to a pump and fully
extended and then retracted a minimum of 5 times. This cycle will
lubricate the cylinder wall, reducing the possibility of corrosion
and damage thereof.
How to remove faulty coupler:
If cylinder does not retract,
1. Secure load by other means.
2. Depressurize pump and hose.
3. Remove the cylinder from application.
4. Disconnect and replace with new coupler.
NOTICE:
Do not attempt to grasp with pliers or wrench without
first wrapping the jaws of such tool with rags or similar padding.
How to bleed air from system:
1. Place pump at a higher elevation than the hose and cylinder
as shown in Figure 2.
2. Operate pump to fully extend and retract the cylinder 2 or 3 times.
The objective is to force the air bubbles up hill and back to the
pump reservoir.
3. Follow pump instruction manual to bleed the air from pump
reservoir. On most pumps, air can escape by opening the oil
filler plug/screw.
OPERATION
Operate the hydraulic pump to advance and retract the cylinder.
Do not
continue pumping when cylinder is fully extended. Internal
pressure will build up and may damage the seal of the cylinder.
WARNING: NEVER
rely on hydraulic pressure alone to
secure a load!
NEVER
allow personnel to work or pass
under a load until the load is secured by cribbing, blocking,
or other mechanical means.
WARNING: T
o help prevent material fatigue if the cylinder
is to be used in a continuous application, the load should
not exceed 85% of the rated capacity.
WARNING:
Your cylinder, hose(s), couplings and pump all
must be rated for the same maximum operating pressure,
correctly connected and compatible with the hydraulic fluid
used. An improperly matched system can cause the system
to fail.
WARNING:
All personnel must be clear before lowering load.
MAINTENANCE
1. Inspect hoses and connections daily. Replace damaged
components immediately with BVA Hydraulics Replacement
Parts only.
2. Tighten connections as needed. Use pipe thread sealing
compound when servicing connections.
3.
Always use clean, approved hydraulic fluid and change as
recommended or sooner if the fluid becomes contaminated
(never exceed 400 hours). Follow pump manufacturers
instructions for changing and adding hydraulic fluid.
Use only
good quality hydraulic fluid. We recommend
Mobil DTE13M
or equivalent when using with hand pump or air pump; BVA
Hydraulics Oil (F01) or equivalent when using with electric
pump.
Never
use brake fluid, transmission fluid, turbine oil,
motor oil, alcohol, glycerin etc. Use of other than good quality
hydraulic oil will void warranty and damage the cylinder, pump,
hose etc.
4. Use an approved, high-grade pipe thread sealant to seal all
hydraulic connections. Teflon tape can be used if only one layer
of tape is used and it is applied carefully (two threads back) to
prevent the tape from being introduced into hydraulic system.
A piece of tape could travel through the system and obstruct
the flow of fluid and adversely affect function.
Lubrication & Cleaning
Keep cylinder clean at all times.
1. Any exposed threads (male or female) must be cleaned and
lubricated regularly, and protected from damage. Lubricate with
light machine oil.
2. If a cylinder or ram has been exposed to rain, snow, sand,
airborne abrasive, or any corrosive environment, it must be
cleaned, lubricated, and protected immediately after exposure.
Daily clean exposed ram with clean cloth dampened with light
machine oil. Protect exposed ram from the elements at all times.
3. Keep the hydraulic system as free of dirt as possible. When
not in use, couplers must be sealed with dust covers. All hose
connections must be free of dirt and grime. Any equipment
attached to the cylinder must be kept clean.
!
!
!
!
Figure 2 - Illustration to bleed air from system