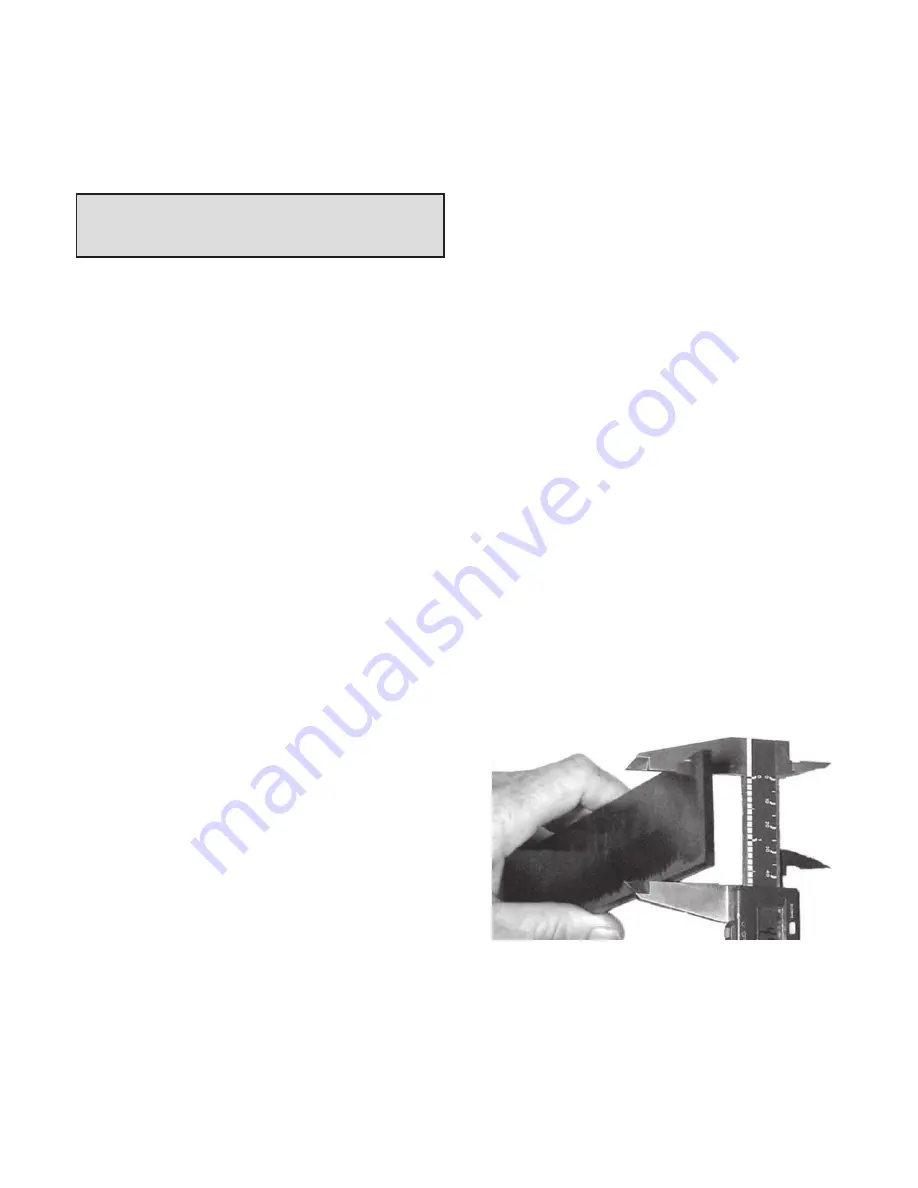
The motor must be connected in accordance with the
electrical codes using a fused switch to protect the
motor against electrical or mechanical overloads. The
motor starter has to be set consistent with the motor
current, listed on the nameplate. For other voltage
requirements, contact the factory for motor and/or
starter information.
Correct direction of rotation is marked by an arrow on
the housing and is clockwise when looking at the motor
from the motor’s fan side.
Observe the motor fan and jog the motor briefly to make
sure it is rotating clockwise. If the motor is rotating
backwards, correct as follows:
On 3 phase motors, reverse any two leads of the three
at the power connection.
Single-phase motors are normally prewired for the cor-
rect direction. In cases where the motor is wired bi-
directional, see the schematic on the underside of the
terminal box cover for the correct direction.
2.0
SERVICE AND PARTS
Following the instructions in this manual, the technician
can completely service and repair the Seco SV pump.
A complete inventory of spare parts is maintained at
Busch, Inc. at all times. Parts will be shipped immedi-
ately upon request.
The pumps may also be shipped to the Virginia Beach,
Virginia factory or nearest authorized service center for
repair. For the location of the nearest authorized serv-
ice center, contact Busch, Inc. in Virginia Beach,
Virginia.
Busch, Inc. maintains an excellent repair department
staffed by factory-trained technicians who specialize
solely in Busch products.
3.0
MAINTENANCE
The required periodic maintenance on the Seco SV
pumps is very low. To prevent premature wear and to
insure optimum performance, it is recommended that
the following steps be performed:
3.1
Inlet Filter
The inlet filter element (Ref. 27) is located inside the fil-
ter cover (Ref. 24) at the front of the pump. Access to
the filter can be gained by removing the two socket
head cap screws (Ref. 72) retaining the outer plastic
cover (Ref. 70) and the three socket head cap screws
and copper washers (Ref. 28/29) retaining the filter
cover.
The filter cartridge should be cleaned on a weekly
basis, depending on the amount of foreign particles to
which the pump is exposed.
When cleaning the inlet filters be careful not to knock
any foreign particles that have collected inside the
housing into the pump. Replace the element if it is
extremely dirty or has been subjected to moisture, oil or
grease.
3.2
Vacuum Relief Valve
A vacuum relief valve comes installed on the most cur-
rent models. It is designed to allow a continuous flow
of air through the pump to maximize vane life. This
valve should be field adjusted to slightly exceed the
vacuum level required for the specific application.
3.3
Vane Inspection
Vane wear should be checked every six months or
more often when the pump is subjected to severe oper-
ating conditions. Vane wear can be checked (see Fig.
6) by following the first three steps of the disassembly
procedure. See the values below for wear tolerances:
Pump Model
Minimum Width of Vane
SV1010
27 mm / 1.063 inch
SV1016
27 mm / 1.063 inch
SV1025
33 mm / 1.339 inch
SV1040
33 mm / 1.339 inch
4.0
DISASSEMBLY
4.1
Tools
To completely disassemble/assemble the Seco pumps,
the following tools are recommended:
CAUTION: After electrical connection has
been made, the rotation of the motor must
be checked.
3
Fig. 6 - Measuring Vane Width