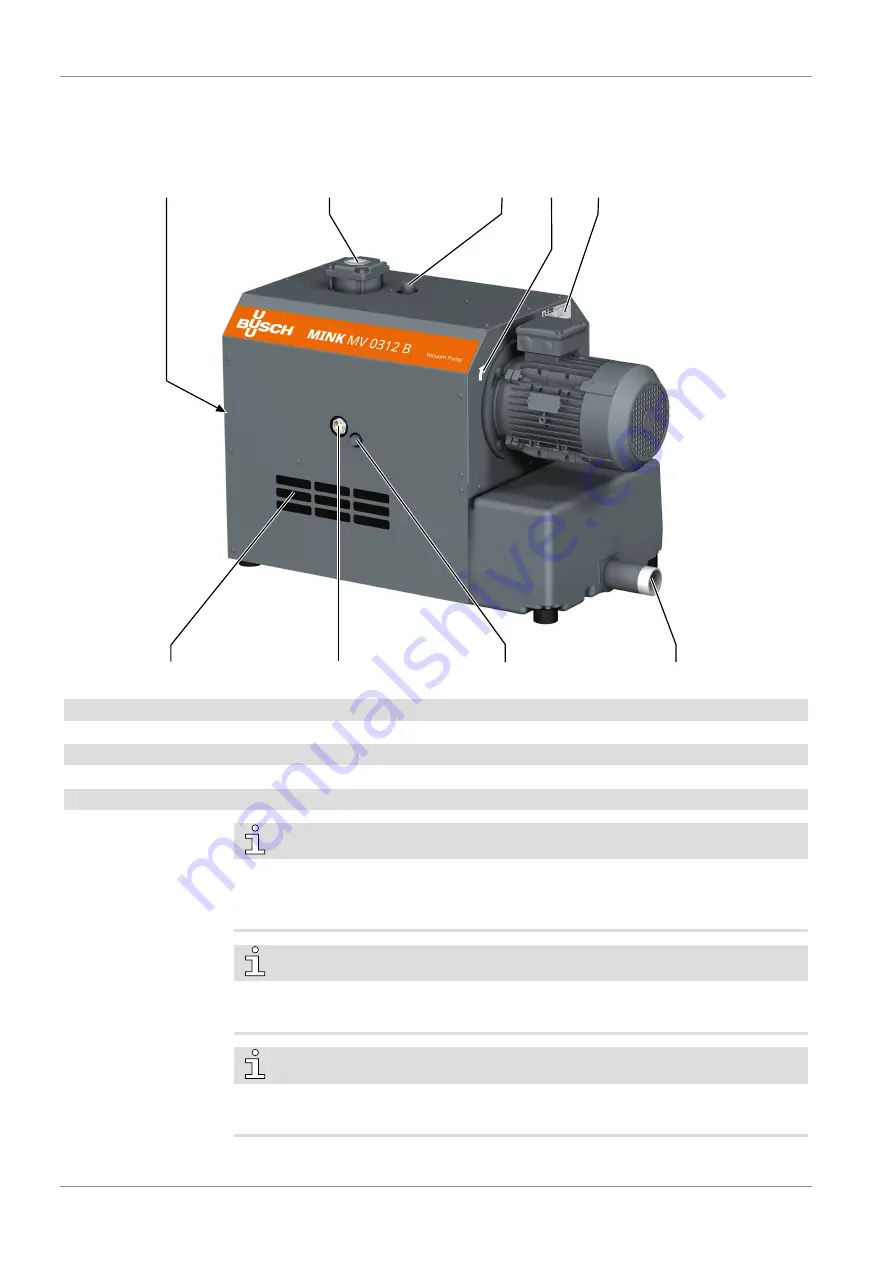
2 | Product Description
4 / 24
0870166451_MV0312B_B0004_IM_en_MD
2
Product Description
CAI
IN
OFP
CAO
OSG
ODP
OUT
NP
DA
IN
Suction connection
ODP
Oil drain plug
OUT
Discharge connection
CAI
Cooling air inlet
OFP
Oil fill plug (=Venting valve)
CAO
Cooling air outlet
OSG
Oil sight glass
NP
Nameplate
DA
Directional arrow
NOTE
Technical term.
In this instruction manual, we consider that the term ‘machine’ refers to the ‘vacuum
pump’.
NOTE
Illustrations
In this instruction manual the illustrations may differ from the machine appearance.
NOTE
Product origin
The serial number on the nameplate (NP) determines the manufacturing plant.
Summary of Contents for MINK MV 0312 B
Page 23: ...Note ...