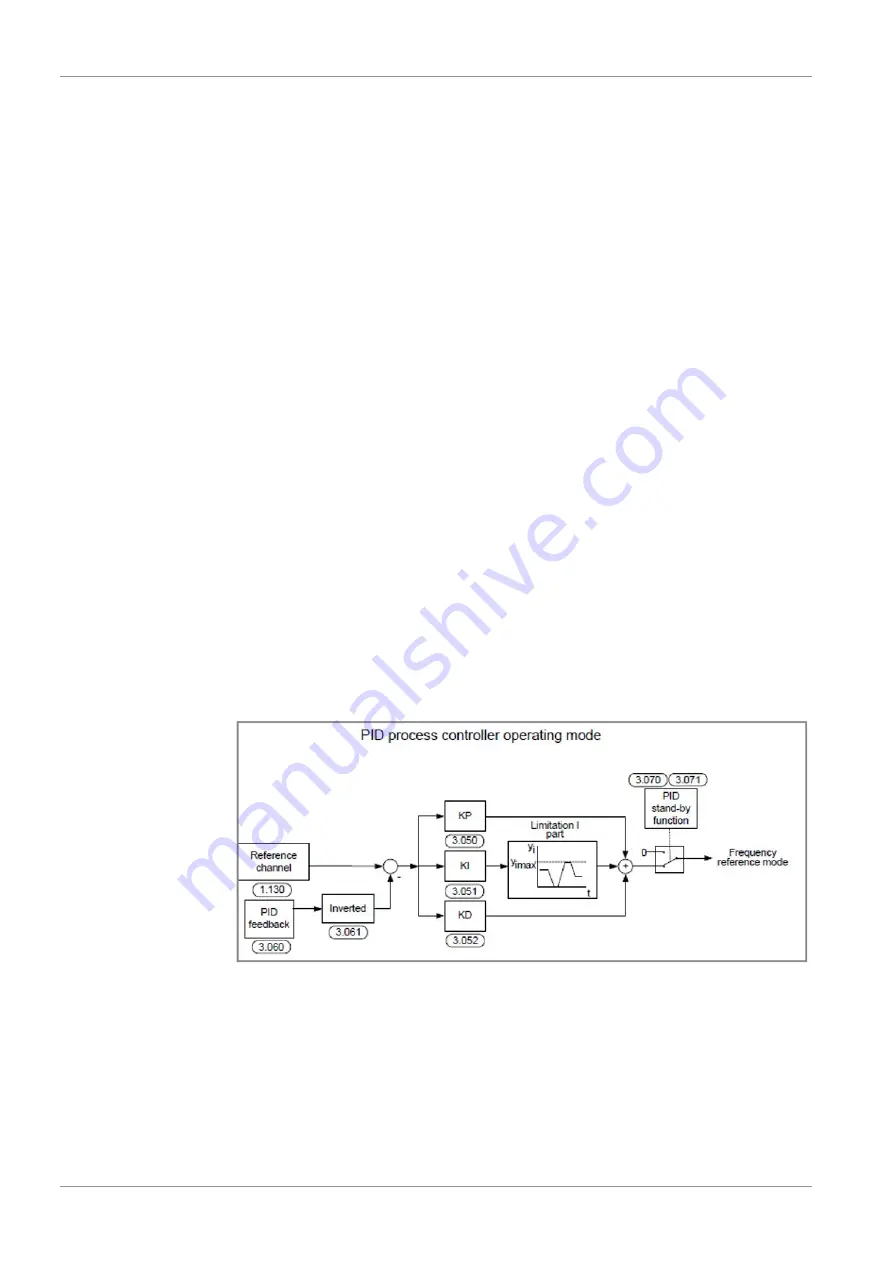
7 | Parameter Description
32 / 44
0870208958_INVEOR_VFD_-0002_PCI_en
4.065 AI2 physical maximum
Selection of the upper limit of a physical value to be displayed:
100 = default value to be adapt to your process
7.7 PID Process Control
7.7.1 Description
In the case of PID process control, the target pressure value and actual pressure value are
compared and the system then regulates to reach the pressure target. This requires to
connect the optional pressure transmitter (part nr. 0653 215 220) to the analogue input
1 or 2.
PID process control:
The target value for the PID process controller is read in percentage steps as in the “fre-
quency setting mode”. 100 % corresponds to the working range of the connected
sensor, which is read in via the actual value input (selected by the “PID actual value”).
Depending on the control difference, a rotation speed value is output to the control out-
put with the help of the amplification factors for the proportional gain (3.050), integral
gain (3.051) and derivative gain (3.052).
In order to prevent the integral share from increasing infinitely in the case of uncontrol-
lable control differences, this value is limited to a specific set value (corresponding to the
“maximum frequency” (1.021)).
PID inverted (usually used in vacuum process):
The PID actual value can be inverted using parameter 3.061. The actual value is impor-
ted inversely, i.e. 0 V … 10 V correspond internally to 100% … 0%.
Please note that the target value must also be defined inversely.
An example:
A sensor with an analogue output signal (0 V… 10 V) is to operate as the source of the
actual value (at AIx). At an output variable of 7 V (70 %), this is to be regulated in-
versely. The internal actual value then corresponds to 100 % – 70 % = 30 %.
In other words, the target value to be specified is 30 %.