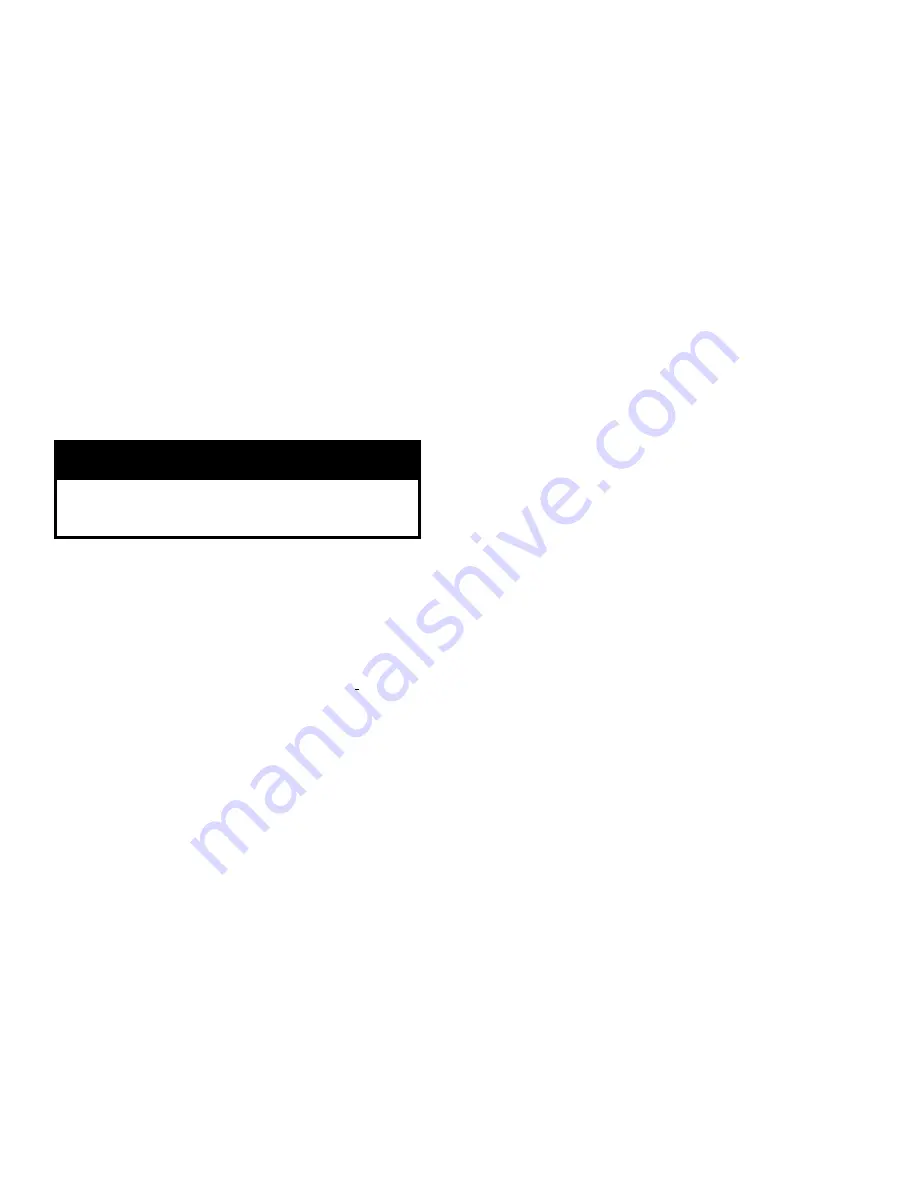
50
Operate the boiler with steam in the entire
system for a few days allowing the condensate
to return to the boiler. If the condensate can
temporarily be wasted, operate boiler only for
the length of time it takes for condensate to run
clear. If the latter cannot be achieved or if the
condensate is returned to the boiler, boil out
the boiler using the SURFACE BLOW-OFF
connection, see Figure 7.
i
. Drain boiler until 1” of water is visible in
gauge glass. Run temporary 1½” NPT pipe
line from the surface blow-off connection to
an open drain or some other location where
hot water may be discharged safely. Do not
install valve in this line.
ii
. Drain about 5 gallons of hot water from
boiler into a container and dissolve into it
an appropriate amount of recommended boil
out compound. Remove safety valve & add
solution to boiler water thru exposed tapping
using a funnel.
NOTICE
Check with local authorities or consult local
water treatment services for acceptable chemical
cleaning compounds.
iii
. Start burner and operate sufficiently to boil
the water without producing steam pressure.
Boil for about 5 hours. Open boiler feed
pipe sufficiently to permit a steady trickle
of water from the surface blow-off pipe.
Continue this slow boiling and trickle of
overflow for several hours until the water
coming from the overflow is clear.
iv
. Stop burner and drain boiler in a manner
and to a location that hot water can be
discharged with safety.
v
. Refill boiler to normal water line. If water
in gauge glass does not appear to be clear,
repeat steps (
i
. thru
iii
.) and boil out the
boiler for a longer time.
b. Low pressure steam boilers such as the
MegaSteam™, should be maintained with
appropriate water treatment compounds.
Add suitable water treatment compounds as
recommended by your qualified water treatment
company.
c. Remove temporary surface blow-off piping, plug
tapping and reinstall safety valve. Boil or bring
water temperature to 180°F promptly in order to
drive off the dissolved gases in the fresh water.
d. If unsteady water line, foaming or priming
persist, install gate valve in Hartford Loop and
drain valves in return main and at boiler as
shown in Figure 12 and proceed as follows:
i
Connect hoses from drain valves to floor
drain. Close gate valve in Hartford Loop and
open drain valve in return main. Fill boiler
to normal water level, turn on oil burner and
operate boiler at this water level for at least
30 minutes after the condensate begins to
run hot, then turn off burner.
Close all radiator valves. Remove all supply
main air valves and plug the openings in
supply main.
ii.
Draw about 5 gallons of hot water from
boiler into a container and dissolve into it
the appropriate amount of a recommended
boilout compound. Remove safety valve
from boiler and pour this solution into
boiler, then reinstall safety valve.
iii
. Turn on oil burner and keep operating while
feeding water to boiler slowly. This will
raise water level in boiler slowly so that
water will be boiling hot and will rise slowly
into supply main and back through return
main, flowing from drain hose at about
180°F. Continue until water runs clear from
drain hose for at least 30 minutes.
iv
. Stop feeding water to boiler but continue
operating oil burner until excess water in
boiler flows out through supply main and
water lowers (by steaming) until it reaches
normal level in boiler. Turn off oil burner.
Drain boiler. Open all radiator valves.
Reinstall all supply main air valves. Open
gate valve in Hartford Loop.
v
. When boiler has cooled down sufficiently
(crown sheet of sections are not too hot to
touch), close the drain valves at boiler and
in return main and feed water slowly up to
normal level in boiler. Turn on oil burner
and allow boiler to steam for 10 minutes,
then turn off burner. Draw off one quart of
water from bottom gauge glass fitting and
discard. Draw off another quart sample and
if this sample is not clear, repeat the cycle
of draining the boiler and return main and
refilling the boiler until sample is clear.
vi
. If the boiler water becomes dirty again
at a later date due to additional sediment
loosened up in the piping, close gate valve
in Hartford Loop, open drain valve in
return main, turn on oil burner and allow
Condensate to flow to drain until it has run
clear for at least 30 minutes while feeding
water to boiler so as to maintain normal
water level. Turn off oil burner, drain boiler,
open gate valve in Hartford Loop, then
repeat Step 1 above.
e. Make pH or Alkalinity Test.
After boiler and system have been cleaned and
refilled as previously described, test the pH of
the water in the system. This can easily be done
Summary of Contents for MST288
Page 11: ...11 Figure 4 Boiler Removal from Skid ...
Page 19: ...19 Figure 9 Float Type LWCO and Pressure Limit Installation ...
Page 25: ...25 Figure 12 Recommended Boiler Piping for Gravity Return Steam Boiler ...
Page 34: ...34 Figure 18 Wiring Diagram Steam Hydrolevel CG450 Probe LWCO ...
Page 35: ...35 Figure 18A Wiring Diagram Riello 40 Series Burner Steam Hydrolevel CG450 Probe LWCO ...
Page 36: ...36 Figure 19 Wiring Diagram Steam McDonnell Miller PS 801 Probe LWCO ...
Page 37: ...37 Figure 19A Wiring Diagram Riello 40 Series Burner Steam McDonnell Miller PS 801 Probe LWCO ...
Page 38: ...38 Figure 20 Wiring Diagram Steam McDonnell Miller 67 Float LWCO ...
Page 39: ...39 Figure 20A Wiring Diagram Riello 40 Series Burner Steam McDonnell Miller 67 Float LWCO ...
Page 45: ...45 Figure 24 L1 and V1 Head Electrode Positioning and Gun Setting Beckett AFG ...
Page 58: ...58 Bare Boiler Assembly ...
Page 60: ...60 Jacket Assembly ...
Page 62: ...62 MST288 Thru MST629 Steam Boilers Trim and Controls ...
Page 64: ...64 Beckett AFG Burner ...