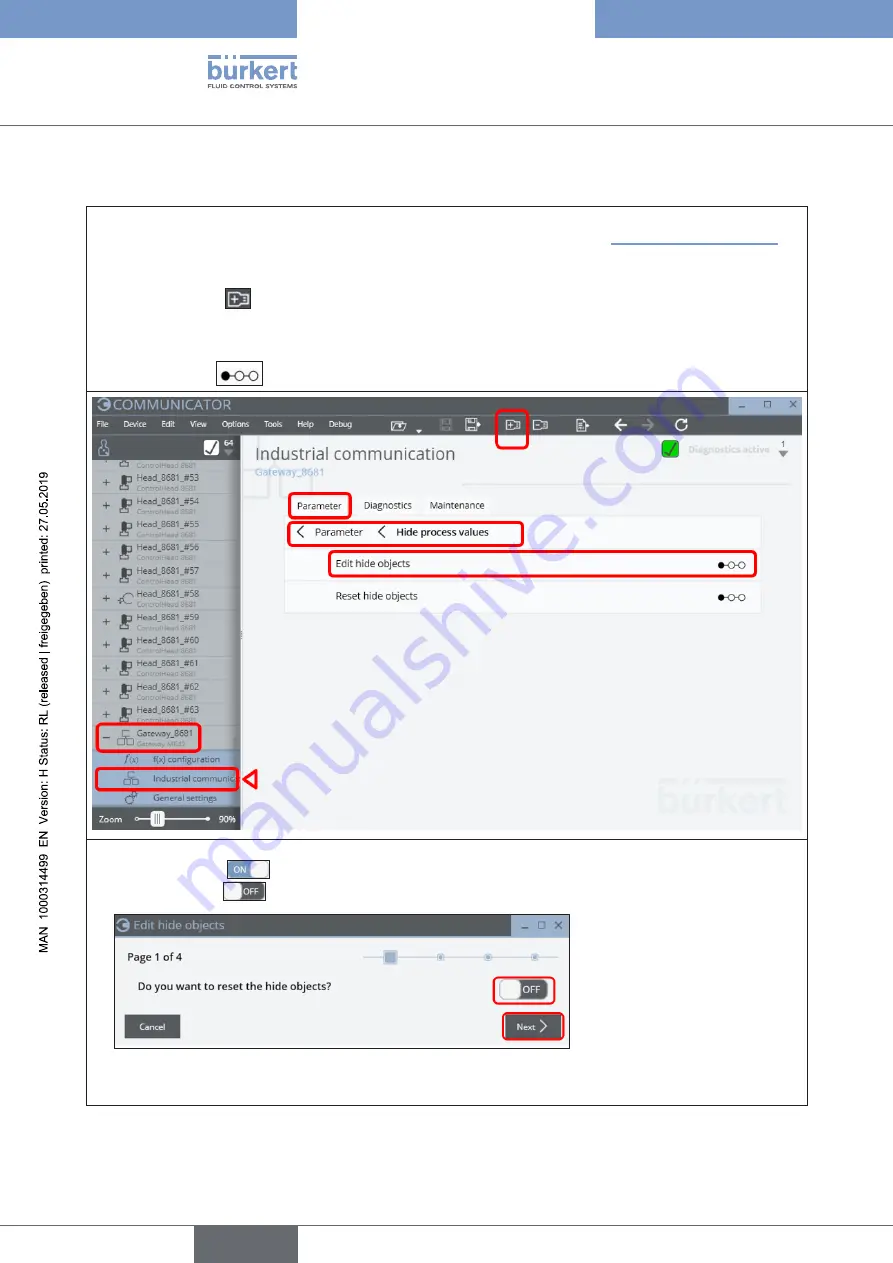
48
büS/CANopen-Design
6.17.2 “Hide function” via “Bürkert Communicator”
→
Connect the PC (with Bürkert Communicator Type 8920) via “büS stick” to the büS/CANopen data line (e.g.
to a free connection of a CAN junction box in the same network - as shown in “Fig. 2: Network principle”)
→
Start the Bürkert Communicator Type 8920
→
Click on the icon
to add an interface (e.g. “büS COM8”)
→
Open the desired gateway (e.g. “Gateway_8681”) and select
“Industrial communication”
and then the
“Parameter”
tab, search for
“Hide process values”,
then
select
“Edit hide objects”
and start the
step sequence
with a click
→
“Page 1”
: Start the “hiding function”:
set the switch to
(ON) in order to reset already hidden values – or
set the switch to
(OFF) in order to NOT reset already hidden values.
→
Click on
“Next”
(or cancel the “hiding process” via button “Cancel”).
english
Type 8681 büS/CANopen
Summary of Contents for 8681
Page 59: ...59 english Type 8681 büS CANopen ...
Page 60: ...www burkert com ...