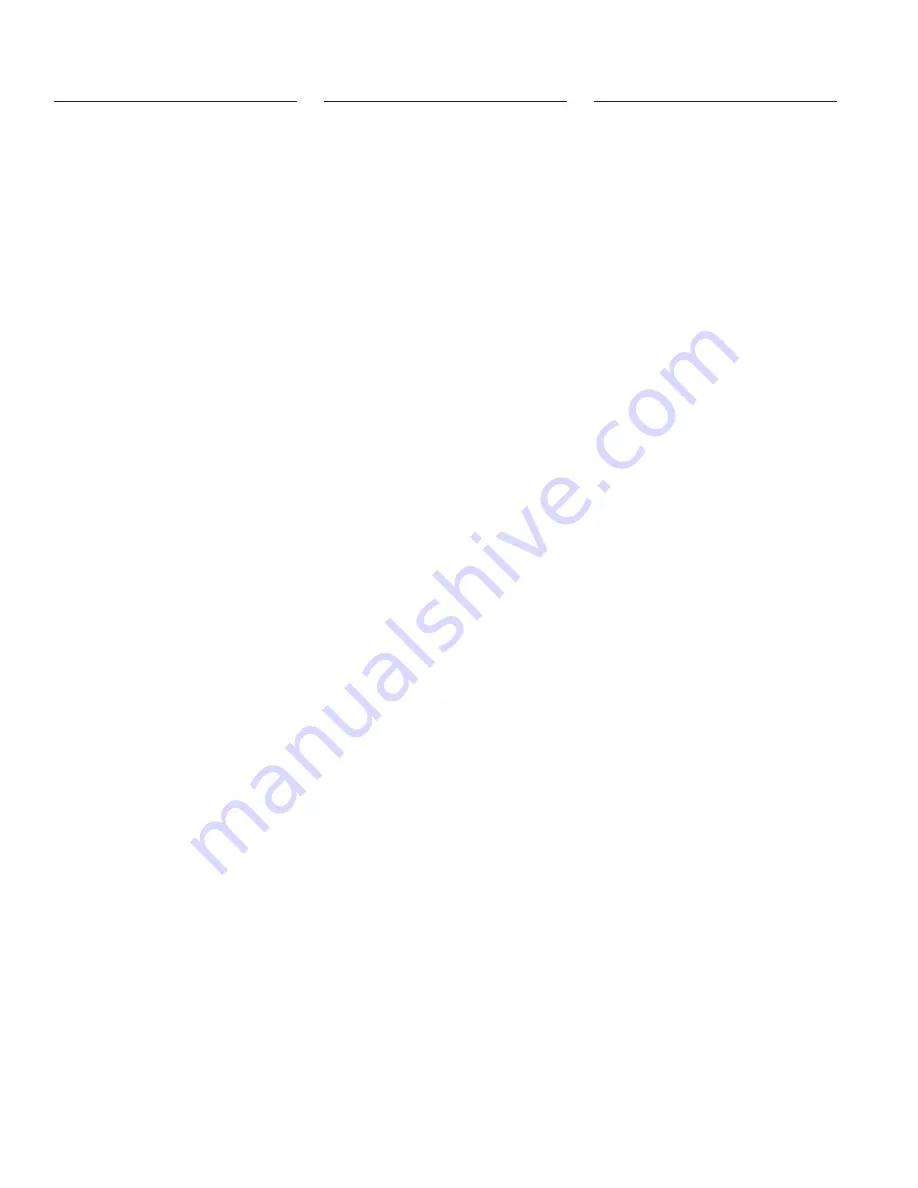
Page 10
TROUBLESHOOTING (cont.)
PROBLEM
PROBABLE CAUSE
REMEDY
Water will not heat or display shows
HEATING TIME TOO LONG.
1. Limit Thermostats
2. Temperature probe
3. Tank heaters
4. Control Board
Remove power from the brewer.
Check for continuity through the
limit thermostat.
CAUTION:
Do not
eliminate or bypass limit thermo-
stat. Use only replacement part
23717.0003.
Remove the probe from the grom-
met and submerge in a water bath
of approximately 70°F (21°C).
Connect an ohmmeter to the pins
in the connector. At 60°F (16°C),
the reading should be 15.3k ± 2k
OHMS, at 70°F (21°C) the reading
should be 11.8k ± 2k OHMS, and
at 80°F (27°C) the reading should
be 9.3k ± 2k OHMS. If the probe is
within these parameters, reconnect
to the control board.
Remove power from the brewer.
Check for continuity through the
tank heaters. If no continuity is
present, check for a wiring problem
(consult wiring schematic), then
replace the tank heater if no wiring
problem is found.
Remove power from the brewer.
Connect a voltmeter across the
tank heater. Reapply power to the
brewer and refer to testing outputs
on page 15. If the voltage measured
when the tank heater is turned on
is very low or zero, then substitute
a control board know to be good
working order.
41747 112608
RELEASED FOR PRODUCTION
DIR Num: 41747.0000 12, December 2018