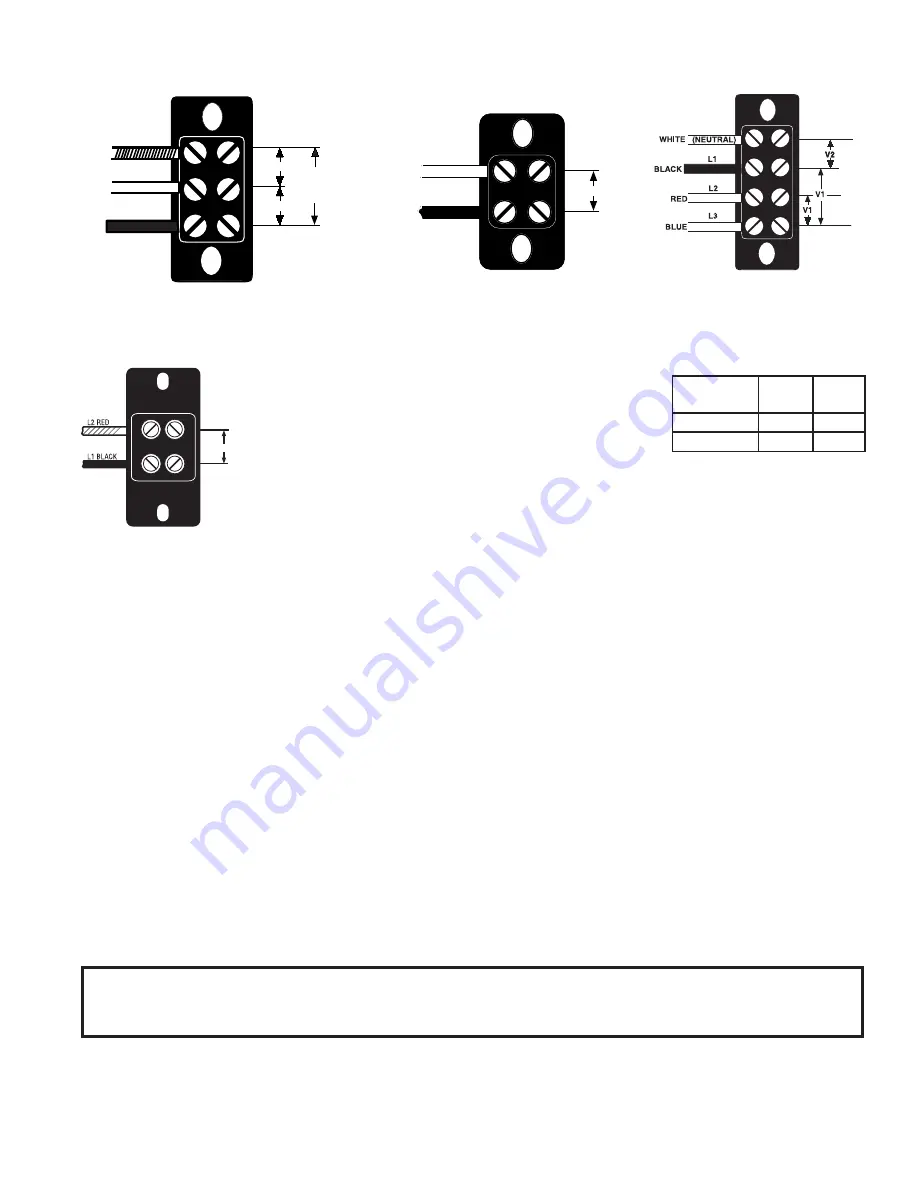
Page 5
ELECTRICAL HOOK-UP
CAUTION –
Improper electrical installation will damage electronic components.
1. An electrician must provide electrical service as specified.
2. Using a voltmeter, check the voltage and color coding of each conductor at the electrical source.
3. Remove the front, lower left access panel beneath the sprayhead.
4. Feed the cord through the strain relief and connect it to the terminal block.
5. Connect the brewer to the power source and verify the voltage at the terminal block before proceeding. Replace the
access panel.
6. If plumbing is to be hooked up later be sure the brewer is disconnected from the power source. If plumbing has been
hooked up, the brewer is ready for
Initial Set-Up.
PLUMBING REQUIREMENTS
This brewer must be connected to a cold water system with operating pressure between 20 and 90 psi (138 and 620
kPa) from a
1
⁄
2
" or larger supply line. A shut-off valve should be installed in the line before the brewer. Install a regulator
in the line when pressure is greater than 90 psi (620 kPa) to reduce it to 50 psi (345 kPa). The water inlet fitting is
3
⁄
8
" flare
or female quick connect.
NOTE –
Bunn-O-Matic recommends
3
⁄
8
" copper tubing for all installations from the
1
⁄
2
" water supply line. A tight coil of copper
tubing in the water line will facilitate moving the brewer to clean the counter top. Bunn-O-Matic does not recommend the
use of a saddle valve to install the brewer. The size and shape of the hole made in the supply line by this type of device may
restrict water flow.
This equipment must be installed to comply with the Basic Plumbing Code of the
Building Officials and Code Administrators International, Inc. (BOCA)
and the Food Service Sanitation Manual of the Food and Drug Administration (FDA).
PLUMBING HOOK-UP
1. Flush the water line and securely attach it to the flare fitting located on bottom of brewer.
2. Turn on the water supply.
Requires 3-wire, grounded service rated
120/208 or 120/240 volts ac, 30 amp, single
phase, 60 Hz.
ELECTRICAL REQUIREMENTS
L2 RED
WHITE
NEUTRAL
L1 BLACK
120 V.A.C.
120 V.A.C.
208 OR 240 V A.C.
P1841
Requires 4-wire, grounded
service rated 120/208 volts
ac or 120/240 volts ac, 30
amp, three phase, 50 Hz.
L1, L2, L3, are the 3 phases
V1 = Phase to phase voltage, between any 2 phases.
V2 = Phase to neutral voltage, L1 to neutral must be 120V.
P2612
SYSTEM
VOLTAGE
V1
V2
208
208
120
240
240
120
CAUTION:
Do not connect L1 to a circuit operating at
more than 150 volts to ground.
35879 112204
Requires 2-wire, grounded
service rated 120 volts ac, 20
amp, single phase, 60 Hz.
120V.A.C.
NEUTRAL
WHITE
L1 BLACK
Requires 2-wire, grounded
service rated or 200 volts
ac, 26.4 amp or 230 volts
ac, 26.9 amp, single phase,
60 Hz.
200 or 230V.A.C.