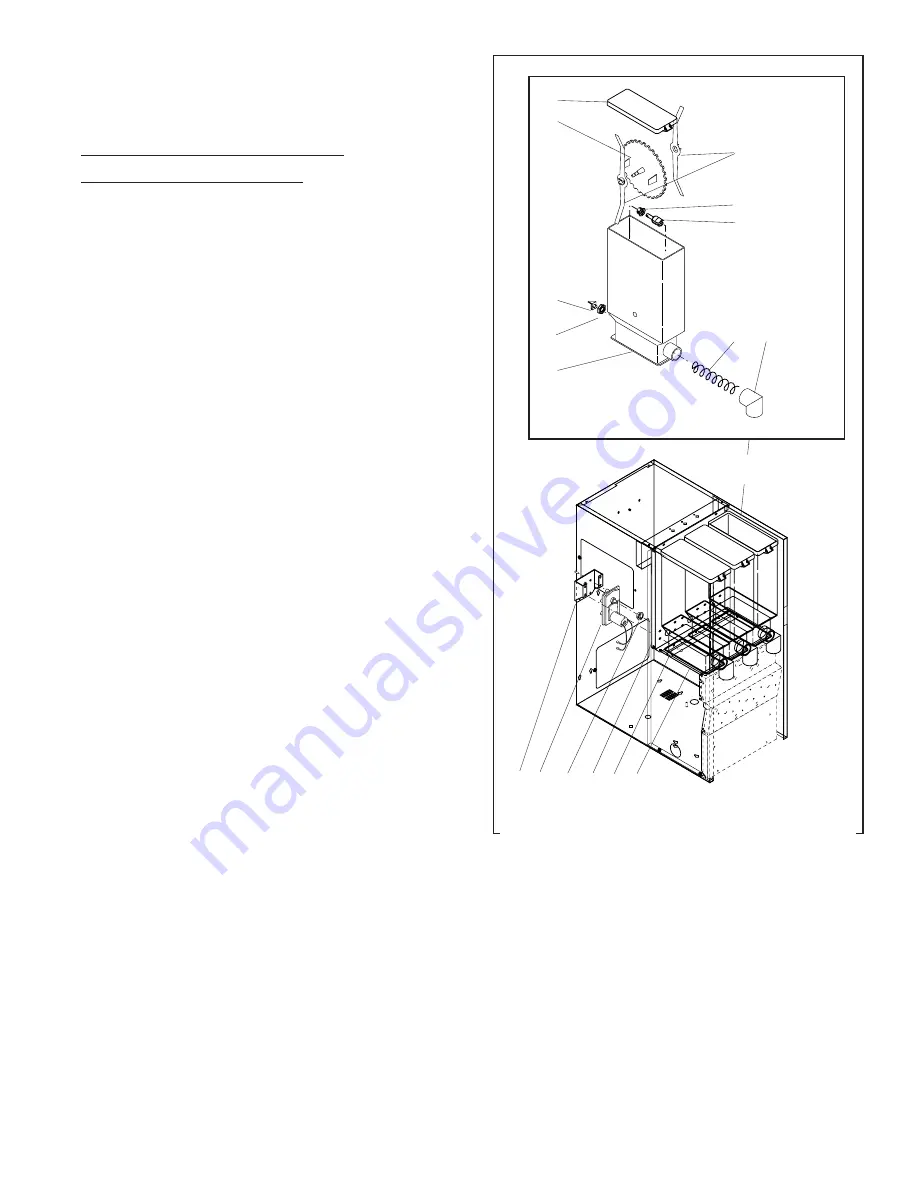
17
SERVICE
AUGER DRIVE COMPONENTS (CONT.)
P2210.30
12 13 14 11 15 16
Late Models
1. Hopper Lid
2. Agitator Disk Assy
3. Auger Drive Shaft
Bushing
4. Mixing Blade
5. Auger Drive Shaft
6. Auger Drive Bracket
7. Locknut
8. Hopper
9. Auger Wire
10. Ejector Elbow
11. Auger Motor Mount-
ing Panel
12. Auger Motor Bracket
13. Auger Motor
14. Dust Seal
15. Shoulder Screw
16. Hopper Support plate
17. Hopper Assembly
1
2
6
7
8
4
3
5
9 10
17
FIG. 3 AUGER DRIVE & HOPPER DISASSEMBLY
Removal, Cleaning and Replacement:
Hopper & Auger (Late Models):
1. Open the dispenser door and raise the top front
cover.
2. Lift the front edge of hopper assy (17) over the
tab on hopper support plate (16) and slide hop-
per assembly out the front of the dispenser.
3. Remove hopper lid (1) and empty product.
4. Pull off the ejector elbow (10).
5. Remove agitator disk assy (2) by pushing out on
the side of the hopper, rotating the agitator disk
assy out of the mounting hubs and lifting the agi-
tator disk assy from the hopper. Remove the mix-
ing blades (4) from the agitator disk by tugging
sharply.
6. Remove auger (9) by pulling it out the front of the
hopper (8).
7. Remove the auger drive bracket by turning it clock-
wise whilde holding the auger drive shaft firmly.
8. Slide auger drive shaft (5) from auger drive shaft
bushing (3) and remove from hopper (8).
9. Remove locknut (7) from auger drive shaft bush-
ing (3) and remove auger drive shaft bushing from
hopper (8).
10. Wash components in a mild solution of dish de-
tergent using a bristle brush when needed.
11. Rinse and dry each item thoroughly.
12. Check for damaged or broken components, re-
place any if necessary and reassemble hopper
assembly.
13. Install hopper assy (17) in the dispenser by sliding
hopper assy in the guides on the hopper support
plate (16) until the slot in the bottom rear the
hopper seats against the shoulder screw (15) in
the hopper support plate.
29215 011906