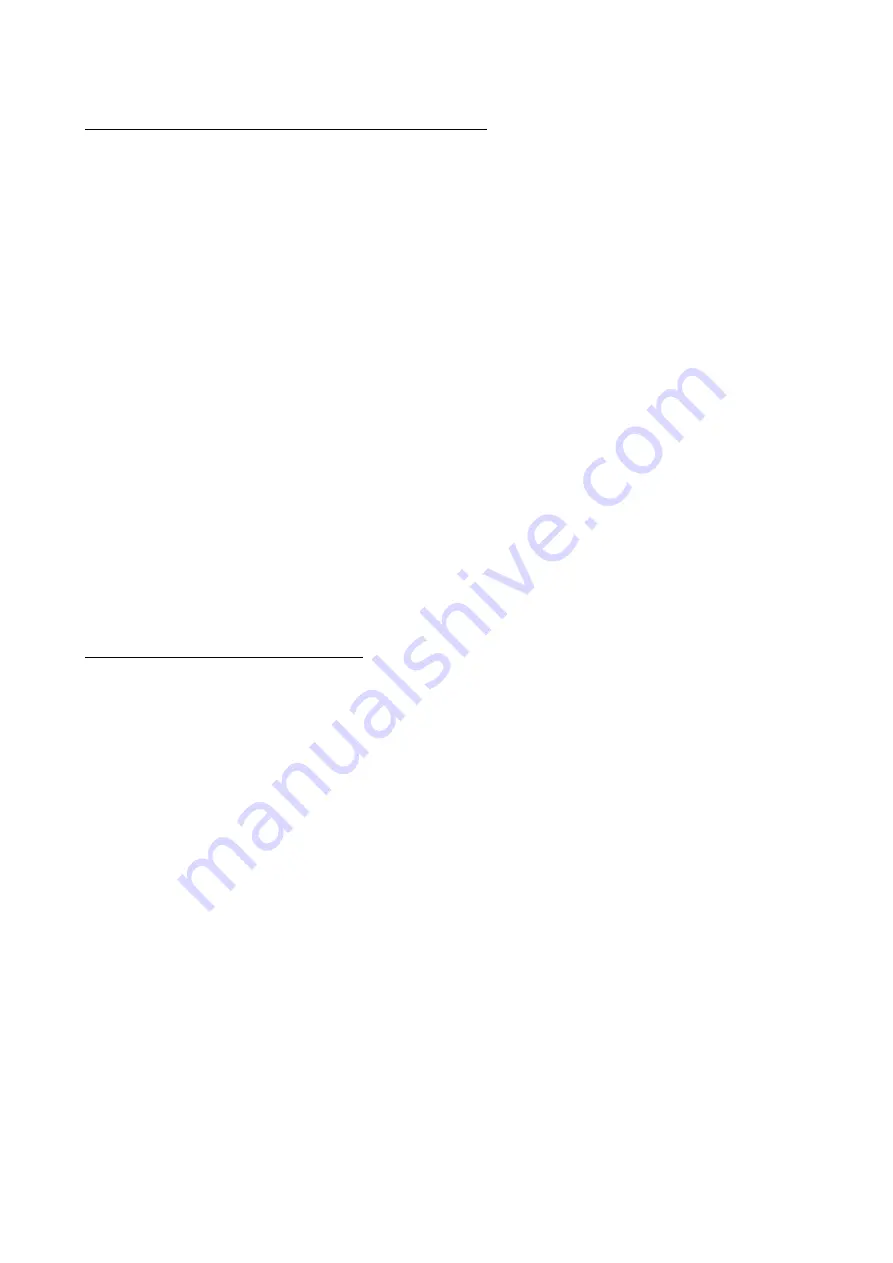
R8
009W2229
General Information for Work with the Gear
Show cleanliness when repairing the gear and before the gear is opened it must be
carefully cleaned.
Use special tools as stated earlier in this section when removing and fitting the gear.
The seal face between the two parts of the housing is tightened with liquid jointing.
When dismantling the halves of the gearbox from each other, loosen the screws in the
flanged joint first and push/press back the fitting pins.
Press the two halves of the gearbox from each other by means of two rods or the like.
Do not use chisels.
Use special tools for loosening parts fixed to the shafts such as bearings, gear-wheels etc.
When assembling the gear and fitting the bearings it is necessary to heat the cylinder
bearings in oil bath before fitting them. The temperature must not exceed 120°C.
When fitting the bearing outer rings the housing should be heated and the bearing outer
rings should be fitted with Loctite.
Removal of Gear from Engine
Before the gear can be dismantled it must be removed from the engine:
1. Loosen the propeller shaft flange and push the propeller shaft a little backwards.
2. Loosen the gear from the engine by removing the bolts of the intermediate flange
between the engine and gear.
3. Lift clear the gear of the engine.
4. Dismantle the flexible coupling by loosening the central nut and pulling off the
coupling half from the input shaft of the gear with special tool No. T 41069.
Summary of Contents for DV36/48
Page 3: ...A1 009W2329 SECTION A INTRODUCTION AND TECHNICAL DATA...
Page 9: ...A7 009W2329...
Page 11: ...A9 009W2329 Longitudinal Section of DV36...
Page 12: ...A10 009W2329 Cross Section of DV36...
Page 14: ......
Page 15: ...B1 009W2329 R01 SECTION B LIST OF TOOLS...
Page 20: ...B6 009W2329 R01...
Page 21: ...009W2329 R01 C1 SECTION C CYLINDER HEAD...
Page 23: ...009W2329 R01 C3 Exploded view of cylinder head...
Page 30: ...009W2329 R01 C10 Fitting measurements for the fuel nozzle into insert...
Page 33: ...009W2329 R01 C13 Pressing in dimensions for valve guide...
Page 36: ...009W2329 R01 C16 Exhaust valve Tolerances and repair measures...
Page 37: ...009W2329 R01 C17 Inlet valve Tolerances and repair measures...
Page 43: ...009W2329 R01 D1 SECTION D FLYWHEEL...
Page 47: ...009W2329 R01 E1 SECTION E FRONT END COVER...
Page 51: ...G1 009W2329 R01 SECTION G REAR END COVER AND HAND START...
Page 55: ...G5 009W2329 R01...
Page 56: ...G6 009W2329 R01...
Page 61: ...009W2329 XLS H1 SECTION H FUEL SYSTEM...
Page 73: ...009W2329 XLS H13 Causes and Remedies of the Fuel Pump...
Page 74: ......
Page 75: ...IJ1 009W2329 R01 SECTION IJ PISTON CONNECTING ROD AND CYLINDER LINER...
Page 79: ...IJ5 009W2329 R01 Measurements for Piston...
Page 80: ...IJ6 009W2329 R01...
Page 81: ...IJ7 009W2329 R01 Piston Ring 1 Please note page IJ4...
Page 82: ...IJ8 009W2329 R01 Piston Ring 3 Please note page IJ4...
Page 84: ...IJ10 009W2329 R01 Arrangement of Connecting Rod...
Page 87: ...IJ13 009W2329 R01 Test Measurements of Cylinder Liner...
Page 88: ......
Page 89: ...L1 009W2329 R01 SECTION L CRANKCASE CRANKSHAFT MAIN BEARINGS AND OIL SUMP...
Page 93: ...L5 009W2329 R01 Rear gear wheel and rear part of crank...
Page 95: ...L7 009W2329 R01 Front part of crank...
Page 98: ......
Page 99: ...M1 009W2329 R01 SECTION M CAMSHAFT COMPLETE...
Page 104: ...M6 009W2329 R01 Drawing of pushrod Drwg No 000E9455...
Page 105: ...M7 009W2329 R01 Drawing of push rod guide...
Page 106: ......
Page 107: ...N1 009W2329 R01 SECTION N LUBRICATING OIL SYSTEM...
Page 110: ...N4 009W2329 R01 Fitting of dip stick...
Page 111: ...N5 009W2329 R01 Pipe connections in oil sump...
Page 116: ......
Page 117: ...009W2329 R01 O1 SECTION O COOLING WATER SYSTEM...
Page 125: ...009W2329 R01 O7 Circulation pump...
Page 129: ...009W2329 R01 O11...
Page 130: ...009W2329 R01 O12...
Page 131: ...P1 009W2329 R01 SECTION P ELECTRICAL SYSTEM...
Page 133: ...P3 009W2329 R01...
Page 134: ...P4 009W2329 R01...
Page 135: ...P5 009W2329 R01...
Page 136: ...P6 009W2329 R01...
Page 137: ...P7 009W2329 R01 Generator with double charging diodes Drg no 009V0053...
Page 138: ...P8 009W2329 R01...
Page 139: ...P9 009W2329 R01...
Page 140: ...P10 009W2329 R01...
Page 141: ...R1 009W2329 R01 SECTION R ZF GEAR BW7...
Page 144: ...R4 009W2229...
Page 174: ......
Page 175: ...009W2329 R01 S1 SECTION S SAIL DRIVE TYPE Z 7...
Page 178: ...009W2329 R01 S4...
Page 184: ...009W2329 R01 S10...
Page 185: ...009W2329 R01 S11...
Page 186: ...009W2329 R01 S12...
Page 187: ...009W2329 R01 S13...
Page 188: ......
Page 189: ...009W2329 R01 T1 SECTION T IRREGULAR OPERATION CAUSES AND REMEDIES...
Page 192: ......
Page 193: ...009W2329 R01 V1 SECTION V MAINTENANCE...
Page 194: ...009W2329 R01 V2 CONTENTS Recommended maintenance and check list page V 3...
Page 196: ......