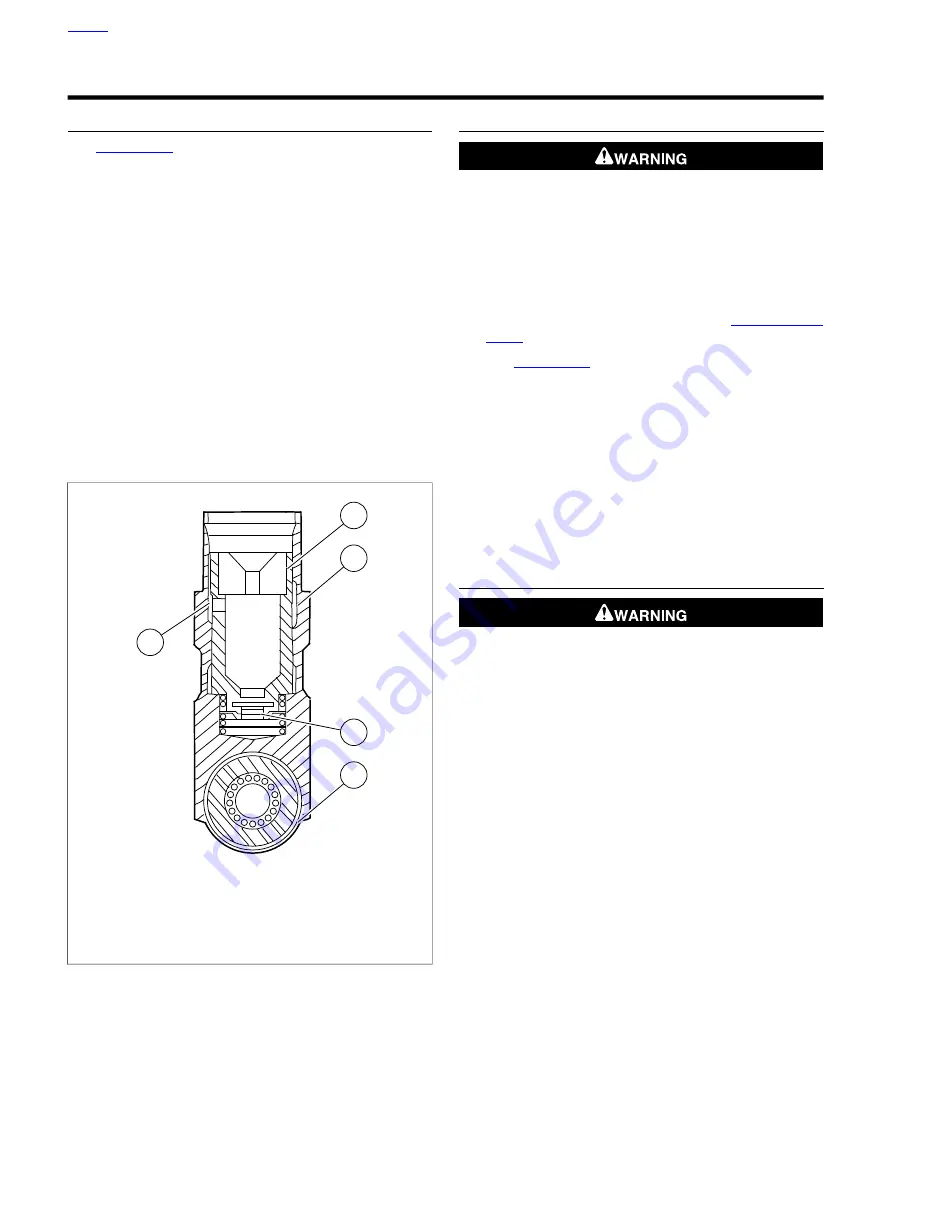
3.16
HYDRAULIC LIFTERS
GENERAL
See
. The lifter assembly consists of a hydraulic
lifter and roller. The lifter and roller, under compression force
from valve spring, follow the surface of the revolving cam. The
up-and-down motion produced is transmitted to the valve by
the push rod and rocker arm. The lifter contains a piston (or
plunger) and cylinder; it also contains a check valve, which
allows the unit to fill with engine oil, thereby reducing clearance
in the valve train.
When a lifter is functioning properly, the assembly operates
with minimal lifter clearance. The unit automatically com-
pensates for heat expansion to maintain a no-clearance condi-
tion.
It is normal for lifters to click when engine is started after
standing for some time. Hydraulic lifters have a definite leak-
down rate which permits the oil in the lifters to escape. This is
necessary to allow units to compensate for various expansion
conditions of parts and still maintain correct clearance opera-
tion. Lifters are functioning properly if they become quiet after
a few minutes of engine operation.
1
2
3
4
5
sm00172
1.
Oil
2.
Piston
3.
Oil
4.
Check valve
5.
Roller
Figure 3-106. Lifter Assembly (Typical)
REMOVAL
Compressed air can pierce the skin and flying debris from
compressed air could cause serious eye injury. Wear
safety glasses when working with compressed air. Never
use your hand to check for air leaks or to determine air
flow rates. (00061a)
1.
Clean all dirt from around crankcase. Blow loose particles
from area with compressed air.
2.
Remove cylinder head assemblies. See
.
3.
See
. Remove push rod covers.
a.
Remove screws (4).
b.
Remove push rod covers (3).
c.
Remove gaskets and O-rings (6, 2). Discard parts.
4.
Remove valve hydraulic lifters (7).
a.
Remove anti-rotation screws (8).
b.
Remove lifters from crankcase bore using a thin-
bladed screwdriver. Mark the location and orientation
(front/back) of each lifter.
CLEANING AND INSPECTION
Compressed air can pierce the skin and flying debris from
compressed air could cause serious eye injury. Wear
safety glasses when working with compressed air. Never
use your hand to check for air leaks or to determine air
flow rates. (00061a)
1.
Clean all parts, except roller/lifter assembly, thoroughly in
solvent. Blow dry with compressed air.
NOTE
Inside and outside micrometers used for measuring roller/lifters
and bores must be calibrated to verify accurate readings.
2.
Inspect valve lifters for excessive clearance in guide.
Accurately measure lifter bore inner diameter with a gauge.
a.
Clearance should be within 0.0008-0.0020 in. (0.0203-
0.0508 mm).
b.
Fit a new lifter and/or replace crankcases if clearance
exceeds SERVICE WEAR LIMIT of 0.0030 in. (0.076
mm).
3.
Check lifter roller freeplay.
a.
Roller clearance on pin should be within 0.0006-
0.0010 in. (0.0152-0.0254 mm).
b.
Replace lifters if clearance exceeds SERVICE WEAR
LIMIT of 0.0015 in. (0.0381 mm).
3-76 2010 XB Service: Engine
Summary of Contents for XB 2010
Page 1: ...2010 Buell XB Models Service Manual 99490 10Y 2009 Buell Motorcycle Company ...
Page 4: ...Blank Text Here ...
Page 6: ...NOTES ...
Page 22: ...NOTES ...
Page 78: ...1 56 2010 XB Service Maintenance NOTES ...
Page 80: ...NOTES ...
Page 268: ...NOTES ...
Page 306: ...sm00134 Figure 3 46 Valve Spring Compressor HOME 3 38 2010 XB Service Engine ...
Page 338: ...sm00207 Figure 3 98 Flanged Oil Line HOME 3 70 2010 XB Service Engine ...
Page 364: ...3 96 2010 XB Service Engine NOTES ...
Page 366: ...NOTES ...
Page 410: ...4 44 2010 XB Service Fuel System NOTES ...
Page 412: ...NOTES ...
Page 472: ...5 60 2010 XB Service Drive Transmission NOTES ...
Page 474: ...NOTES ...
Page 488: ...sm00366 Figure 6 13 Boot Gap HOME 6 14 2010 XB Service Electrical ...
Page 570: ...6 96 2010 XB Service Electrical NOTES ...
Page 572: ...NOTES ...
Page 596: ...NOTES ...
Page 610: ......
Page 620: ...B 24 2010 XB Service Appendix B Wiring NOTES ...
Page 622: ...NOTES ...
Page 626: ...C 4 2010 XB Service Appendix C Conversions NOTES ...
Page 628: ...NOTES ...
Page 666: ...D 38 2010 XB Service Appendix D Hose and Wire Routing NOTES ...
Page 668: ...NOTES ...
Page 674: ...E 6 2010 XB Service Appendix E Active Intake Japanese Models NOTES ...
Page 675: ...TABLE OF CONTENTS SUBJECT PAGE NO F 1 GLOSSARY F 1 APPENDIX F GLOSSARY ...
Page 676: ...NOTES ...
Page 680: ...F 4 2010 XB Service Appendix F Glossary NOTES ...
Page 706: ...XXVI TORQUE VALUES NOTES ...