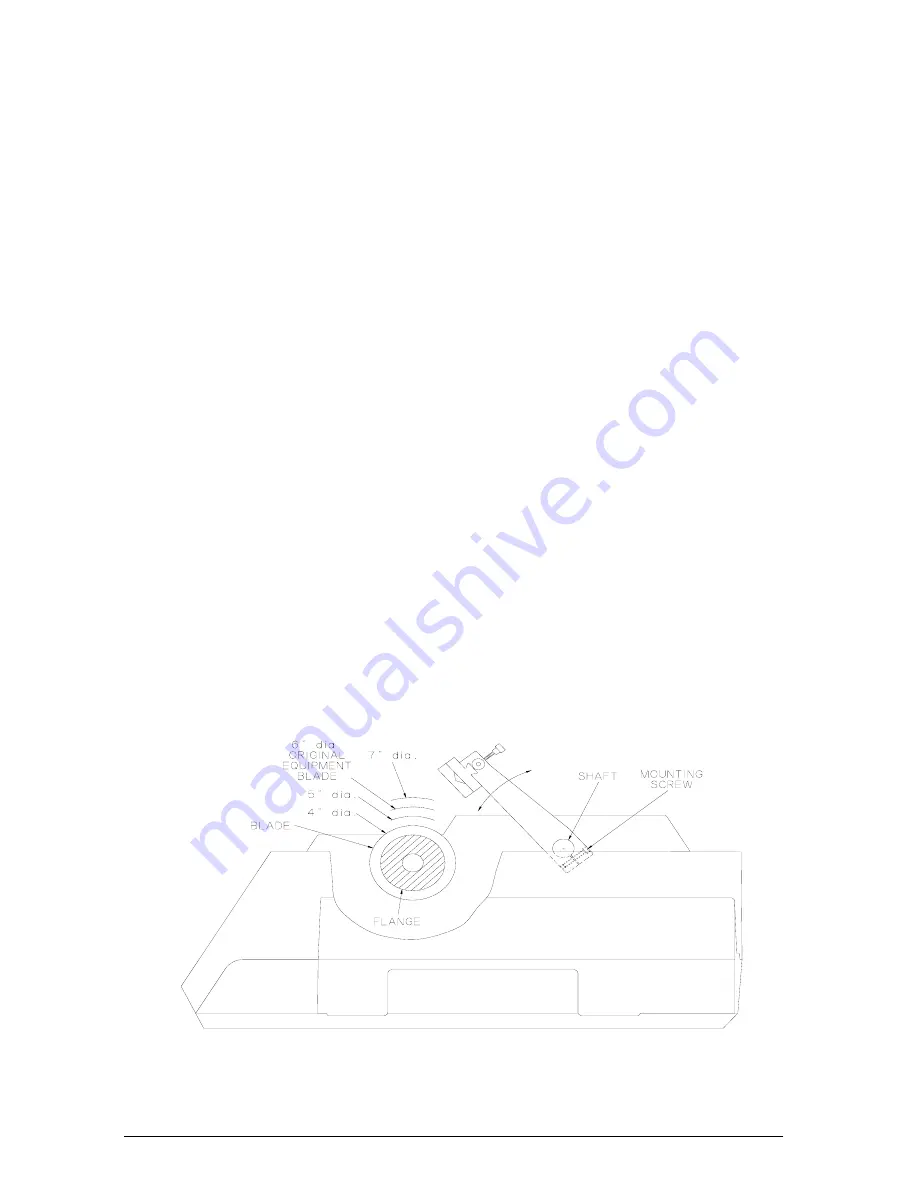
5.
Press the CYCLE RUN Button. The Support Arm will begin to lower
and the Blade will rotate at the selected speed. The preset load will
not be applied for approximately 7 seconds. During this interval, the
sample will approach the blade and a 100g load will be applied in
order to establish a "kerf" cut. The unit will then apply the set load.
The ISOMET™ 2000 Saw is supplied with a 6
″
dia. Wafering Blade
as standard equipment and the Support Arm is set at the factory to
accommodate this condition. In normal operation, the Arm auto-
matically advances the specimen into the Wafering Blade until the
cut is completed or until the lower position limit switch within the
cutter is activated, whichever comes first. If the specimen does not
contact the Wafering Blade within seven seconds, the Arm will
automatically return to the start position without cutting the sample.
This could occur if a much smaller Wafering Blade is used or if the
sample is very small and the Specimen Arm is not repositioned.
Figure 6
shows the factory set Arm position (when the arm is
raised to it’s maximum) relative to the various size Wafering
Blades that may be used with the ISOMET™ 2000 Saw. It is
easy to see that there is a considerable distance for the Support
Arm to travel before making contact with a four inch diameter
blade. The support arm should be lowered with the LOWER
button until the specimen is about 1 cm. from the blade before
starting the cut cycle.
If necessary to allow for a variety of operational conditions, the
Support Arm may be repositioned. This is accomplished by
loosening the Mounting Screw that secures the Support Arm to
the shaft. Be careful to prevent the Support Arm from striking
the Wafering Blade. Reposition the Support Arm as described in
Positioning The Sample section on page 6.
NOTE
Do not move the specimen arm laterally along the shaft. The arm has
25.4 cm of stroke. Any loss in stroke by repositioning the arm may
result in the arm stalling against the cabinet resulting in loss of
micrometer accuracy.
Figure 6
Support Arm Adjustment
6. During operation, observe the Load Bar Graph. Due to
differences in sample thickness and density/consistency, or as
9
MA112480-20
03/06/00
Summary of Contents for ISOMET 2000
Page 1: ...ISO 9001 Registered Company ISOMET 2000 Precision Saw MA112480 20 03 06 00 ...
Page 15: ...Figure 9 Parts Diagram for ISOMET 2000 Precision Saw 13 MA112480 20 03 06 00 ...
Page 16: ...Figure 10 Parts Diagram for ISOMET 2000 Precision Saw 14 MA112480 20 03 06 00 ...
Page 17: ...Figure 11 Parts Diagram for ISOMET 2000 Precision Saw 15 MA112480 20 03 06 00 ...
Page 18: ...Figure 12 Parts Diagram for ISOMET 2000 Precision Saw 16 MA112480 20 03 06 00 ...
Page 19: ...Figure 13 Parts Diagram for ISOMET 2000 Precision Saw 17 MA112480 20 03 06 00 ...
Page 20: ...Figure 14 Parts Diagram for ISOMET 2000 Precision Saw 18 MA112480 20 03 06 00 ...
Page 21: ...Figure 15 Parts Diagram for ISOMET 2000 Precision Saw 19 MA112480 20 03 06 00 ...
Page 22: ...Figure 16 Parts Diagram for ISOMET 2000 Precision Saw 20 MA112480 20 03 06 00 ...
Page 23: ...Figure 17 Parts Diagram for ISOMET 2000 Precision Saw 21 MA112480 20 03 06 00 ...
Page 24: ...Figure 18 Parts Diagram for ISOMET 2000 Precision Saw 22 MA112480 20 03 06 00 ...
Page 25: ...Figure 19 Parts Diagram for ISOMET 2000 Precision Saw 23 MA112480 20 03 06 00 ...
Page 27: ...Figure 21 Parts Diagram for ISOMET 2000 Precision Saw 25 MA112480 20 03 06 00 ...
Page 36: ...NOTES 34 MA112480 20 03 06 00 ...