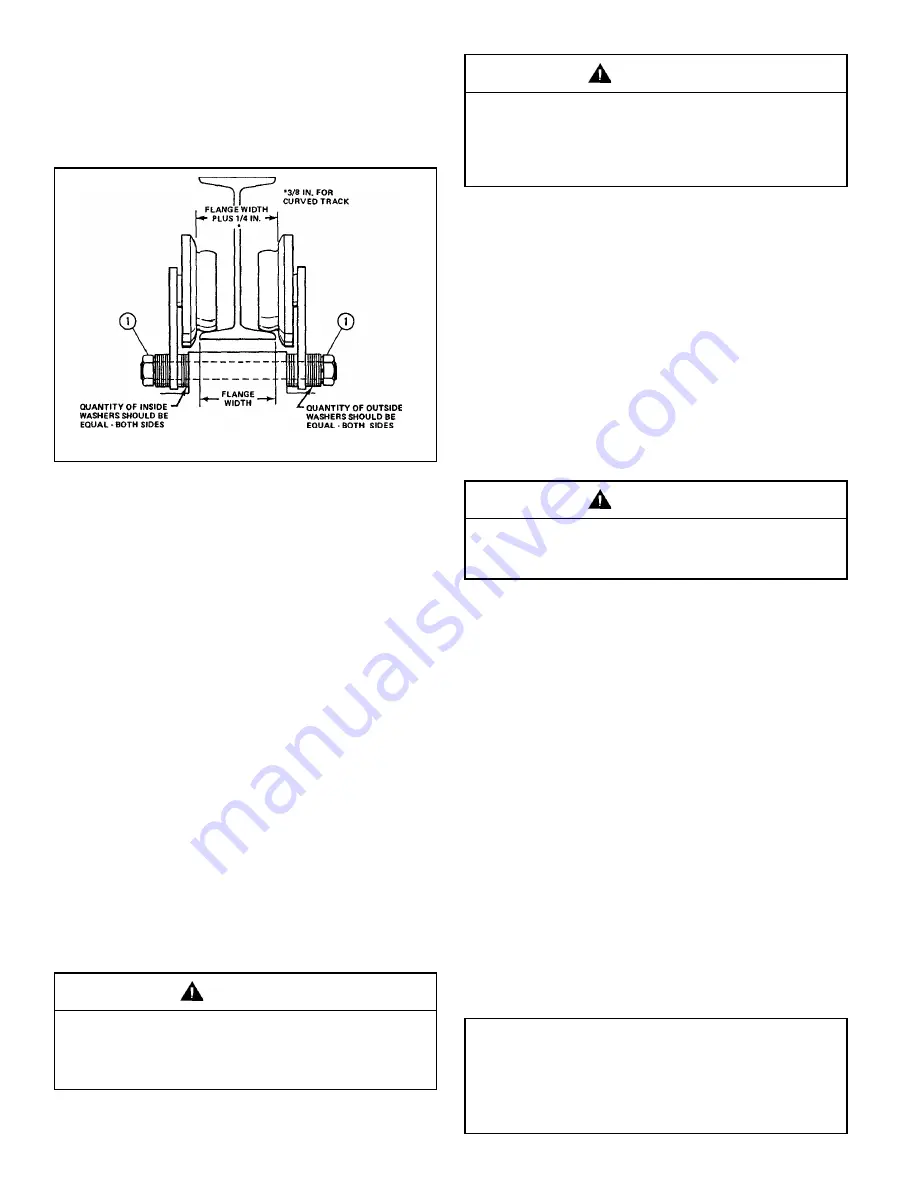
Page 2
The numbers assigned to the parts of our various
assemblies in our parts list are not the part numbers
used in manufacturing the part. They are identification
numbers, that when given with the trolley model number,
permit us to identify, select or manufacture and ship the
correct part needed for any trolley.
particular beam size. As a result the following procedure should
be followed:
4. Measure exact width of bottom beam flange and add 1/4" to this
dimension. This is the required distance between inside faces of
wheel flanges to obtain proper operating clearance, as indicated
in Figure 2.
12207A
Figure 2. Sectional View of Trolley Showing
Proper Wheel and Washer Spacing.
5. An equal number of washers must be removed or added at
each end of lug (inside side plates) as required to obtain proper
wheel spacing determined in Step 4. When spacing is correct,
remaining spacer washers are to be installed in equal numbers
on outside ends of cross pins. Install lock-washers and tighten
hex nuts.
Note: It is important that all the spacer washers that come with
trolley be used.
SUSPENDING TROLLEY AND HOIST
1. On push type trolley models determine whether hoist is to be
suspended with frame parallel to runway beam or cross mounted
(90 degrees to beam). Refer to hoist manual for instructions on
suspension lug rotation.
2. On hand geared models the trolley is restricted to parallel
mounting on hoist frame because of the handwheel and chain.
When hoist chain container is to be used, trolley hand chain must
be placed on side opposite tail chain of hoist (where chain
container is mounted).
3. Hoist and trolley may be installed on I-beam by one of two
methods. If trolley can be slipped directly over end of beam, it
need not be partially disassembled. If this is impossible, remove
hex nuts, lock-washers, outer spacer washers and one side plate
from one side of trolley and reassemble on beam.
OPERATING PRECAUTIONS
DO NOT load trolley beyond rated load.
DO NOT subject trolley to side loads. Always center trolley
over load when hoisting.
DO NOT ram trolley into end stops, other trolleys, or any
obstruction on beam. Improper and careless operation can
result in a hazardous condition for operator and load.
ALWAYS be sure load is clear of obstruction before traversing
load and trolley.
DO NOT stand and DO NOT cause or allow others to stand or
get under any load the trolley is supporting. DO keep clear,
and make sure others keep clear, of any load the trolley is
supporting.
MAINTENANCE AND LUBRICATION
1. BUDGIT Heavy Duty Rigid Mount Trolleys are built to give long
service, but should be inspected periodically for evidence of
damage or wear, particularly when subjected to unusual severe
operating conditions.
2. Lubrication requirements:
a. Wheel bearings are permanently lubricated and require no
additional lubricant.
b. Drive wheel gears are to be lubricated with an open type
gear grease which is heavy, plastic, extreme pressure and
tacky; such as MOBILTAC 325 NC or equal.
REPLACEMENT PARTS
The following parts lists and illustrations cover standard model
BUDGIT Heavy Duty Rigid Mount Trolleys. Typical units are used
as the basis for the exploded parts illustrations; therefore certain
variations may occur from the parts information given. For this
reason always give the catalog number and model number .
Pins referred to in some column headings are trolley suspension
pins.
In all cases, after trolley and hoist have been installed on
I-beam, make sure a suitable stop is secured to each end of
beam to prevent trolley rolling off. Make certain lock-washers
are in place on cross pins and hex nuts are tight.
CAUTION
If trolley is mounted on an open-end beam, end stops
must be installed to prevent trolley from running off the
end of the beam, resulting in injury to operator and others,
including danger to life and limb and damages to load
and other property.
WARNING
These trolleys are not designed nor intended to be used
to support or transport people or for supporting or
transporting loads over people.
WARNING
Recheck clearance dimensions between wheel flanges and
beam flanges.