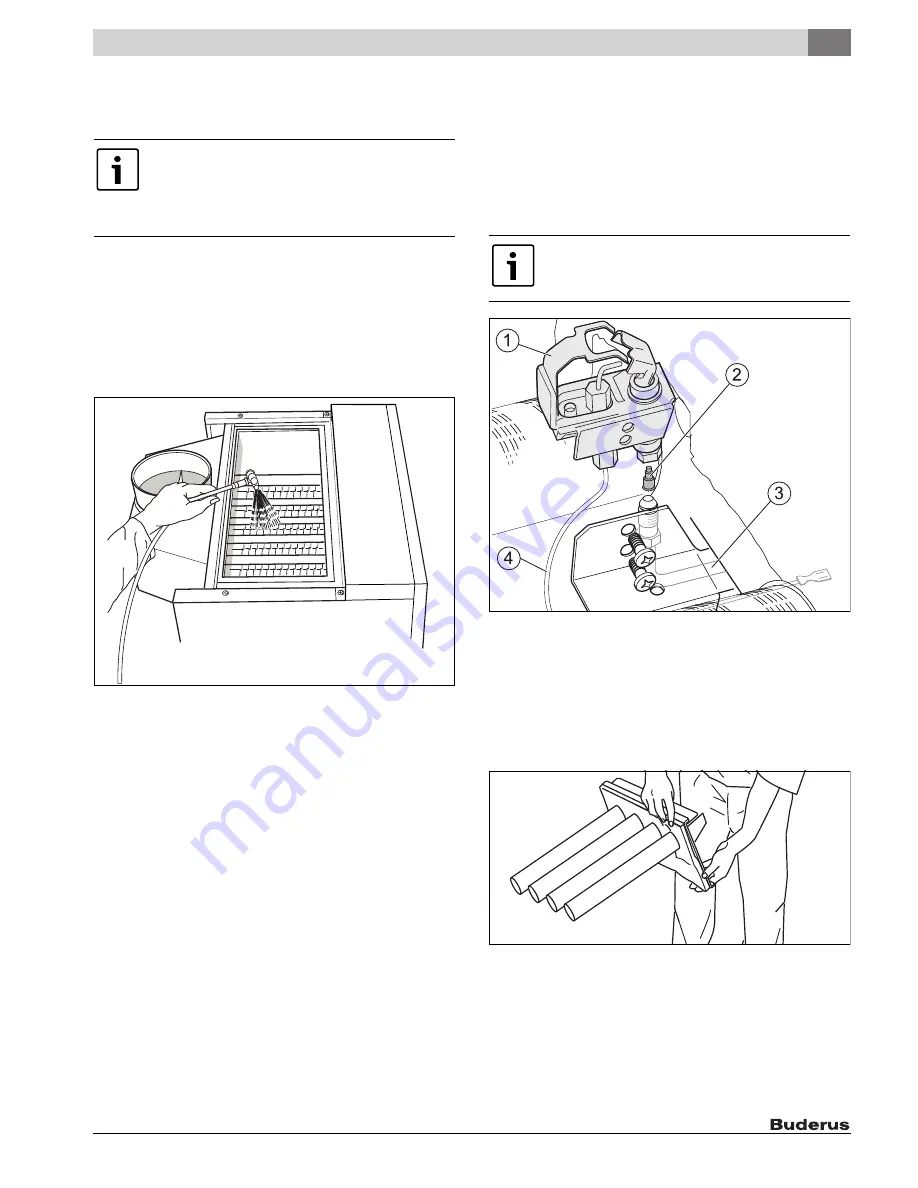
9
Boiler inspection and maintenance
Logano G234X – 6 720 811 233 (2017/02)
27
9.5.3
Wet cleaning the boiler (chemical cleaning)
▶ For wet cleaning, use a cleaning agent appropriate for the degree of
soiling (e. g. soot or scale).
▶ Remove the boiler casing and thermal insulation; check for damage.
▶ Unscrew cleaning cover from the draft diverter.
▶ Cover the control panel with foil to prevent spray getting into the
control panel.
▶ Ventilate boiler room well.
▶ Spray cleaning agent evenly from the top into the hot gas flues
(
▶ Install the burner in reverse order of removal (
Fig. 34 Wet cleaning the boiler
▶ Place the heating system in operation.
▶ Heat the boiler to a temperature of at least 122 °F (55 °C).
▶ Shut down the heating system.
▶ Allow boiler to cool.
▶ Remove burner (
▶ Brush out the hot gas flues.
▶ Clean combustion chamber and bottom panel.
▶ Ventilate boiler room well again.
▶ Install or clean the burner (
▶ Screw cleaning cover into place and replace insulation.
▶ Install boiler cover.
9.6
Cleaning the burner
▶ Remove burner (
▶ Check burner rods for dirt.
If necessary, clean burner as described below:
▶ Unscrew pilot burner unit (
▶ Disconnect pilot gas line [3] from pilot burner unit.
▶ Remove and blow out pilot orifice [2].
▶ Immerse burner rods in water with cleaning agent and brush off.
Fig. 35 Pilot burner
[1]
Pilot burner unit
[2]
Pilot orifice
[3]
Pilot gas line
[4]
Ignitor sensor cable
▶ Rinse off the burner rods under a stream of water. Hold burner so that
water enters all slots of the burner rods and drains out again.
▶ Remove remaining water by swinging the burner (
Fig. 36 Swinging burner
▶ Check that the burner rods are free.
▶ Remove water and dirt residue in the slots.
▶ If slots are damaged: Replace burner.
▶ Install the burner in reverse order of removal (
▶ Place boiler in operation as directed in Section 6, starting on
▶ Check that the AquaSmart
TM
functions properly.
In some circumstances, you may need to proceed
differently from the method described here.
▶ For wet cleaning (chemical cleaning), observe the
operating instructions of the relevant cleaning
equipment and cleaning agent.
6 720 806 028-20.1T
▶ Make sure that the insulation on the burner shield
does not get wet.
Summary of Contents for G234X/38
Page 34: ...10 Logano G234X 6 720 811 233 2017 02 34 Notes...
Page 35: ...10 Logano G234X 6 720 811 233 2017 02 35 Notes...
Page 36: ......