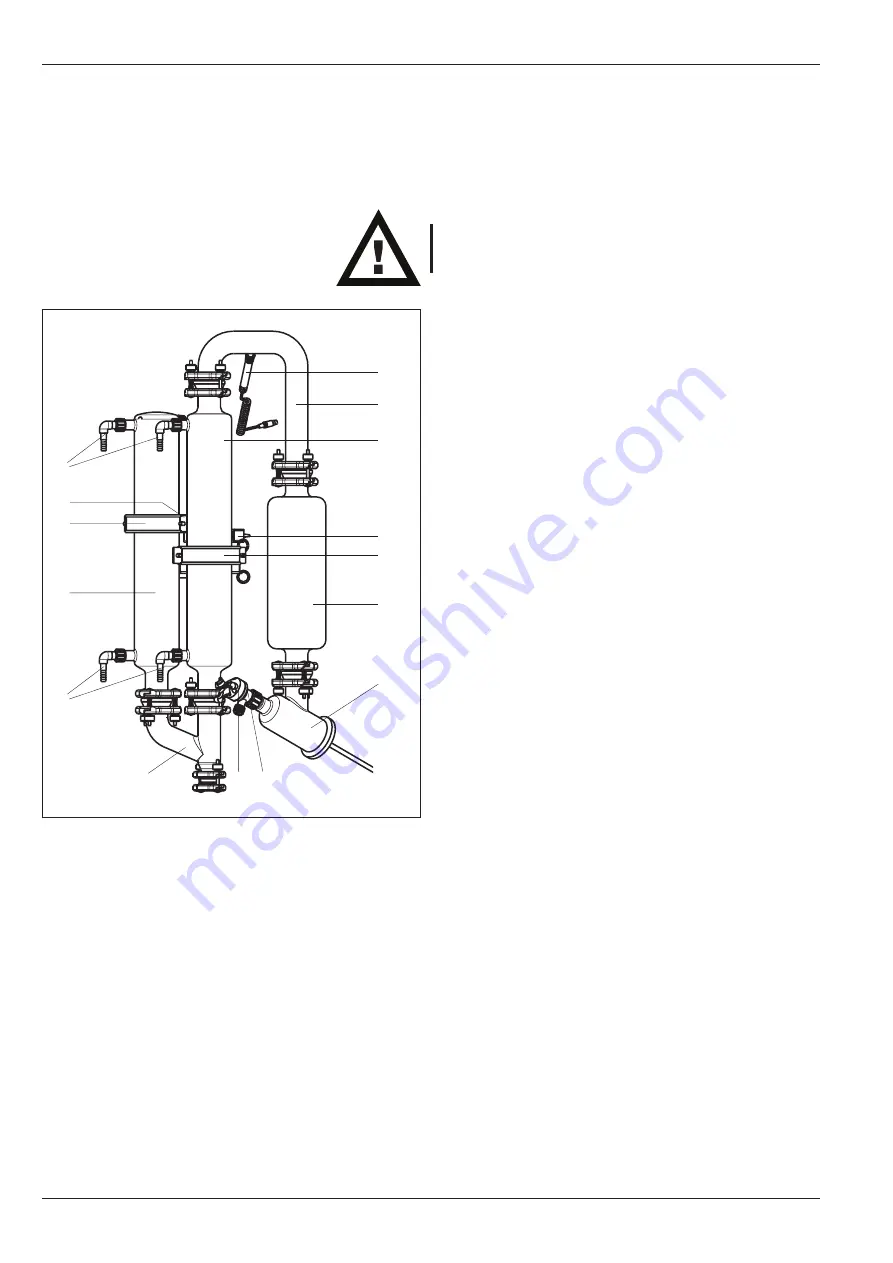
12
BÜCHI
Rotavapor
R-220
4 Putting into Operation
4.8
Installation of the Descending Glass Assembly
with a 2
nd
Cooler
All glassware used must be intact, with no signs of cracks,
spreading impact marks, or other damage. Inspect the glass-
ware visually before installing it.
•
Fix the descending distributor head
햲
in position on the
gear head using a DN70 EasyClamp connection.
•
Place the expansion vessel
햳
on the distribution head
and fix it in position with a DN45 EasyClamp connection.
•
Introduce the cooler
햴
, together with the cooler holder
햵
, into the pivoting clamp
햶
.
•
Connect the cooler and the expansion vessel with the U-
tube
햷
and fix them in position with two DN45 EasyClamp
connections.
•
Insert the second cooler
햸
, together with the cooler holder
햹
, into the pivoting clamp
햺
.
•
Join the two coolers with the Y-connection
햻
and fix them
in position with two DN45 EasyClamp connections.
•
Align the coolers (
햴
and
햸
) and the expansion vessel
햳
in their vertical positions and fix them in place with pivoting
clamps (
햶
and
햺
).
•
Screw the cooling water hose nipples
햽
onto coolers
햴
and
햸
.
•
Insert the stop cock
햾
, with the PTFE hose mounted on
it, into the distribution head, and secure it with a standard
joint clamp
햿
.
•
Screw the temperature sensor
헀
into the support connec-
tion in the U-tube.
•
Check all EasyClamp connections and tighten them evenly
and in parallel.
→
The installation of the receiving fixture is described on Page
13.
Fig. 8: Downgrade glass assembly with two coolers
햸
햹
햽
햺
햽
햻
햿 햾
햶
햲
햷
햳
헀
햴
햵