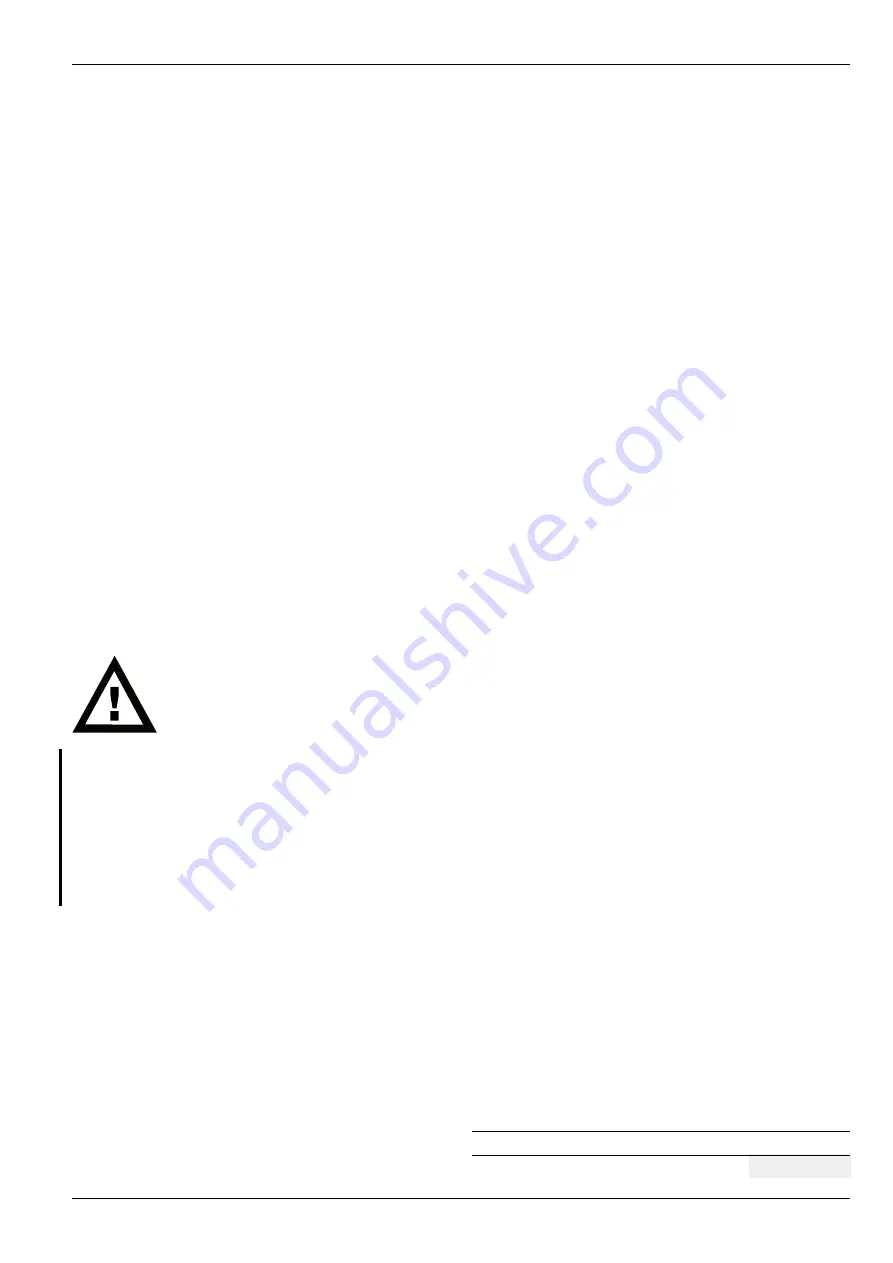
1
BÜCHI
Distillation Unit
K-314
Contents
Contents
Read these instructions thoroughly before you use the
BÜCHI
Distillation Unit
K-314
. Store these instructions in the imme-
diate vicinity of the apparatus so that they may be consulted at
any time. The unit must only be connected to the mains and
switched on after having completed all necessary preparations.
Chapter 2 contains important safety information. Knowledge
of this is imperative for the safe operation of the Distillation
unit.
Subject to technical change without notice. No part of these
instructions may be reproduced in any form whatsoever or
processed, reproduced or disseminated by means of
electronic or optical systems without the express written
permission of Büchi Labortechnik AG. All rights reserved.
Copyright © Büchi Labortechnik AG 1998
en, Version C (22 pages)
Order No.
K-314 Operating instructions
9670
6
1
Scope of Delivery
2
2
Safety
3
2.1
Symbols
3
2.2
Requirements for the operator
3
2.3
Regulation use
3
2.4
Non-regulation use
3
2.5
General hazards
4
2.6
Safety measures
4
3
Function
6
3.1
Principle of operation
6
4
Putting into operation
7
4.1
Setup location
7
4.2.
Unpacking
7
4.3
Water supply
7
4.4
Drain hose
8
4.5
Connection of the supply tanks
8
5
Operation
9
5.1
Control elements
9
5.2
Control elements and their function
9
5.3
Start-up Checklist
10
5.4
Supply tanks
10
5.5
Rubber bung and PTFE hose
10
5.6
Sample tube holder
11
5.7
Distillation outlet tube
12
5.8
Connection to the mains
12
5.9
Adjusting the cooling water flow
12
5.10
K-314 switching ON/OFF checklist
12
5.11
Carrying out the Kjeldahl distillation
13
5.12
Cleaning the unit
13
5.13
Malfunctions
14
6
Maintenance
15
6.1
General information and preparations
15
6.2
Maintenance: daily, weekly
15
6.3
Rubber bung and PTFE hose
15
6.4
Cleaning the feeding pump
16
6.5
Changing glass parts
16
6.6
Customer service
16
6.7
Main fuses
17
6.8
Checking the unit
17
7
Taking out of operation
18
7.1
Storage/Transport
18
7.2
Disposal
18
8
Replacement parts
19
9
Appendix
20