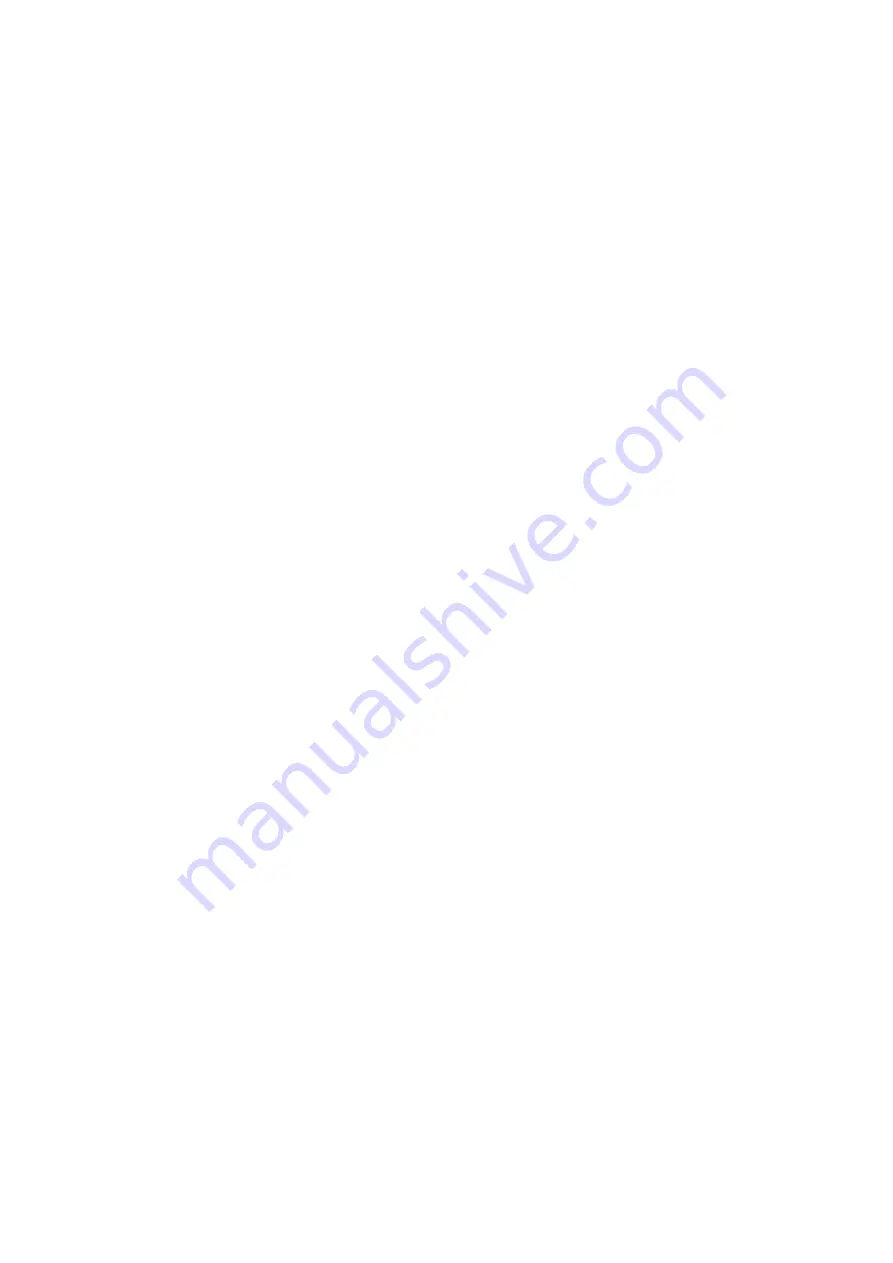
If the unit requires any attention beyond the replacement of contact points and
condenser, it is recommended that the complete machine should be sent to an
authorised Wico service station.
This is fitted between the toolbox and the battery in a position that ensures air-
cooling when the machine is moving.
It is important not to obstruct the air flow to the rectifier by the fitting of any
additional accessories.
Provided that the leads are securely attached to the rectifier no service or
adjustment should be required.
Contact Breaker and Stator Unit
To remove this, first take off the contact breaker cover plate which is held in position
by two screws. Remove the central screw holding the cam (A) Fig. 2, and pull the
cam out, then lift out the cam key. Then remove the three screws (D) holding the
contact breaker housing. The whole unit can then be lifted off with the housing.
Removal of Generator
This should not be attempted by the private owner unless B.S.A. service tool number
No. 61-3188 flywheel extractor is used as described below, otherwise serious damage
to the mainshaft is almost inevitable.
Before proceeding to extract the flywheel from the mainshaft, make sure that the
cam key has been removed from its keyway. Then remove the central nut and its
shakeproof washer. Screw the B.S.A. extractor on to the exposed thread
AS FAR AS
IT WILL GO
.
Finally, turn the central extractor bolt with a suitable spanner until the
flywheel is drawn from its taper.
Electric Horn
The horn is adjusted at the Works to give its best performance and will give a long
period of service without any attention. If it becomes uncertain in action, giving only
a choking sound, or does not vibrate, it does follow that it has broken down. First
ascertain that the trouble is not due to some outside source such as, a discharged
battery, or a loose connection or short-circuit in the wiring. If none of the previous
suggestions prove successful, the horn may be re-adjusted as follows:—
Remove the rubber plug in the horn body; this will expose the adjusting screw.
A slight turn to left or right while depressing the horn button will enable the best note
to be obtained. Finally replace the rubber plug.
If the horn still gives trouble it should be removed and returned to the
manufacturers.
Headlamp
The lamp front, together with the reflector and bulb assembly, is secured to the main
lamp casing by means of a slotted screw under the lamp. To replace a bulb (or
battery on direct lighting models) therefore, it is only necessary to loosen the screw
until the rim can be removed.
To replace the double filament bulb, the small tabs projecting from the base of
the reflector must be bent downwards so that the bulb assembly bracket can be
removed by a slight anti-clockwise rotation. When inserting this bulb the offset (dip)
filament should be uppermost (see Fig. 12).
29