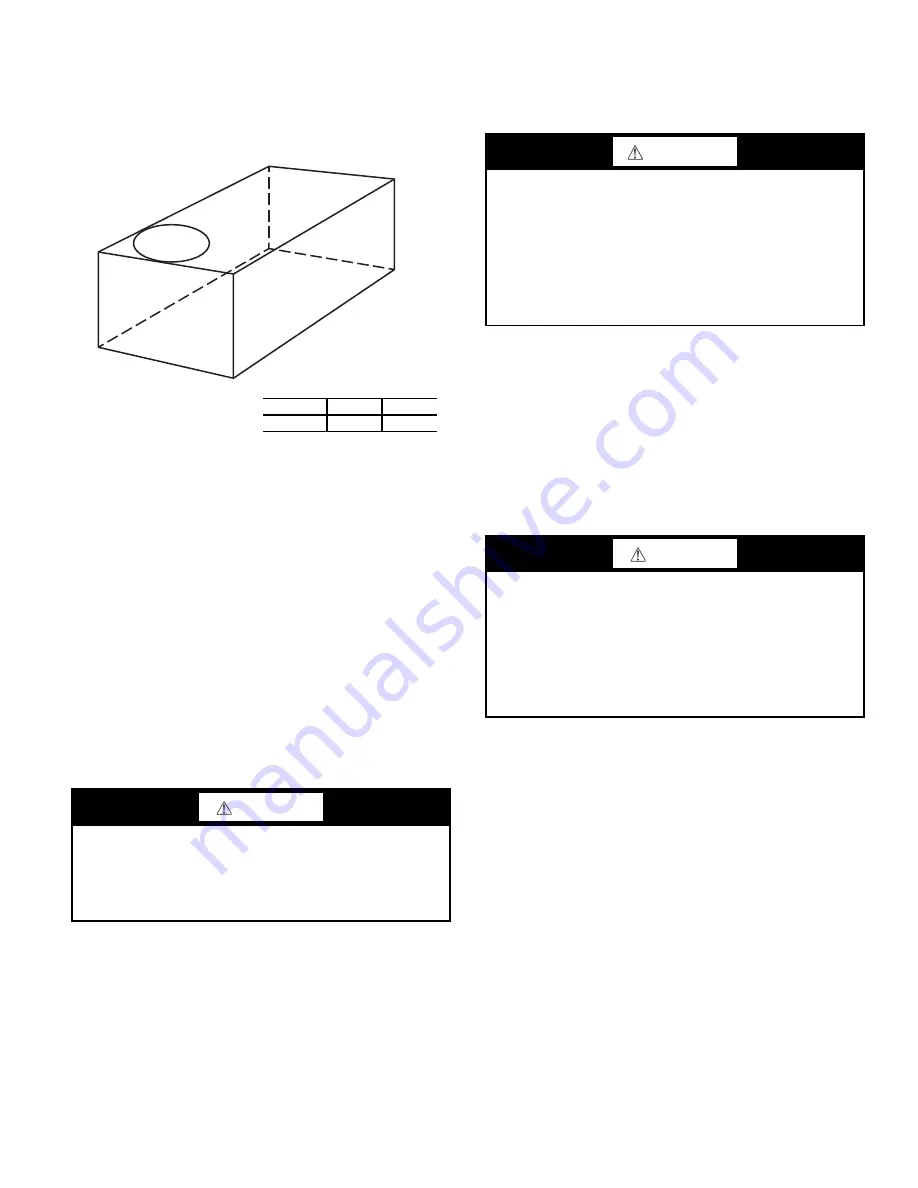
11
ALTERNATE UNIT SUPPORT (IN LIEU OF CURB OR
SLAB MOUNT)
A non-combustible sleeper rail can be used in the unit curb
support area. If sleeper rails cannot be used, support the long
sides of the unit with a minimum of 3 equally spaced 4-in. x
4-in. (102 mm x 102 mm) pads on each side.
Fig. 8 — Unit Leveling Tolerances
Step 5 — Field Fabricate Ductwork
Cabinet return-air static pressure (a negative condition) shall
not exceed 0.35 in. wg (87 Pa) with economizer or 0.45 in. wg
(112 Pa) without economizer.
For vertical ducted applications, secure all ducts to roof curb
and building structure.
Do not connect ductwork to unit.
Fabricate supply ductwork so that the cross sectional dimen-
sions are equal to or greater than the unit supply duct opening
dimensions for the first 18-in. (458 mm) of duct length from
the unit basepan.
Insulate and weatherproof all external ductwork, joints, and
roof openings with counter flashing and mastic in accordance
with applicable codes.
Ducts passing through unconditioned spaces must be insulated
and covered with a vapor barrier.
If a plenum return is used on a vertical unit, the return should
be ducted through the roof deck to comply with applicable fire
codes.
UNITS WITH ACCESSORY ELECTRIC HEATERS
All installations require a minimum clearance to combustible
surfaces of 1-in. (25 mm) from duct for first 12 in. (305 mm)
away from unit.
Outlet grilles must not lie directly below unit discharge.
NOTE: A 90 degree elbow must be provided in the ductwork to
comply with UL (Underwriters Laboratories) code for use with
electric heat.
Step 6 — Rig and Place Unit
Keep unit upright and do not drop. Spreader bars are required.
Rollers may be used to move unit across a roof. Rigging mate-
rials under unit (cardboard or wood) must be removed PRIOR
to placing the unit on the roof curb. Level by using unit frame
as a reference. See Table 2 on page 9 and Fig. 9 for additional
information.
Lifting holes are provided in base rails as shown in Fig. 9. Re-
fer to rigging instructions on unit.
Before setting the unit onto the curb, recheck gasketing on
curb.
Position unit on roof curb so that the following clearances are
maintained:
1
/
4
-in. (6.4 mm) clearance between the roof curb
and the base rail inside the front and rear, 0.0-in. clearance be-
tween the roof curb and the base rail inside on the duct end of
the unit. This will result in the distance between the roof curb
and the base rail inside on the condenser end of the unit being
approximately
1
/
4
-in. (6.4 mm).
Although unit is weatherproof, guard against water from higher
level runoff and overhangs.
After unit is in position, remove the compressor access panel.
Holding the blocking between compressors with one hand, cut
the strapping. Carefully remove the blocking without damag-
ing tubing, wiring, or controls. Remove the strapping and re-
place the access panel.
After unit is in position, remove rigging skids and shipping
materials.
CAUTION
PROPERTY DAMAGE HAZARD
Failure to follow this caution may result in damage to roof-
ing materials.
Membrane roofs can be cut by sharp sheet metal edges. Be
careful when placing any sheet metal parts on such roof.
A
B
C
MAXIMUM ALLOWABLE
DIFFERENCE IN. (MM)
A-B
B-C
A-C
0.5 (13)
1.0 (25)
1.0 (25)
WARNING
PERSONAL INJURY HAZARD
Failure to follow this warning could cause personal injury.
For vertical supply and return units, tools or parts could drop
into ductwork and cause an injury. Install a 90 degree turn in
the return ductwork between the unit and the conditioned
space. If a 90 degree elbow cannot be installed, then a grille of
sufficient strength and density should be installed to prevent
objects from falling into the conditioned space. Due to electric
heater, supply duct will require 90 degree elbow.
CAUTION
UNIT DAMAGE HAZARD
Failure to follow this caution may result in equipment damage.
All panels must be in place when rigging. Unit is not designed
for handling by fork truck when packaging is removed.
If using top crate as spreader bar, once unit is set, carefully
lower wooden crate off building roof top to ground. Ensure
that no people or obstructions are below prior to lowering the
crate.
Summary of Contents for Preferred 549J 04
Page 4: ...4 Fig 2 549J 04 06 Units Built On and After 4 15 2019...
Page 5: ...5 Fig 3 549J 04 06 Units Built Prior to 4 15 2019...
Page 6: ...6 Fig 4 549J 04 06 Corner Weights and Clearances...
Page 7: ...7 Fig 5 549J 04 06 Base Rail Details...
Page 8: ...8 Fig 6 549J 04 06 Thru the Base Charts...
Page 23: ...23 Fig 41 Electro Mechanical Control Wiring 208 230v 460v...
Page 24: ...24 Fig 42 Electro Mechanical Control Wiring 575v...
Page 25: ...25 Fig 43 Electro Mechanical Power Wiring 208 230 1 60...
Page 26: ...26 Fig 44 Electro Mechanical Power Wiring 208 230 3 60...
Page 27: ...27 Fig 45 Electro Mechanical Power Wiring 460 3 60...
Page 28: ...28 Fig 46 Electro Mechanical Power Wiring 575 3 60...