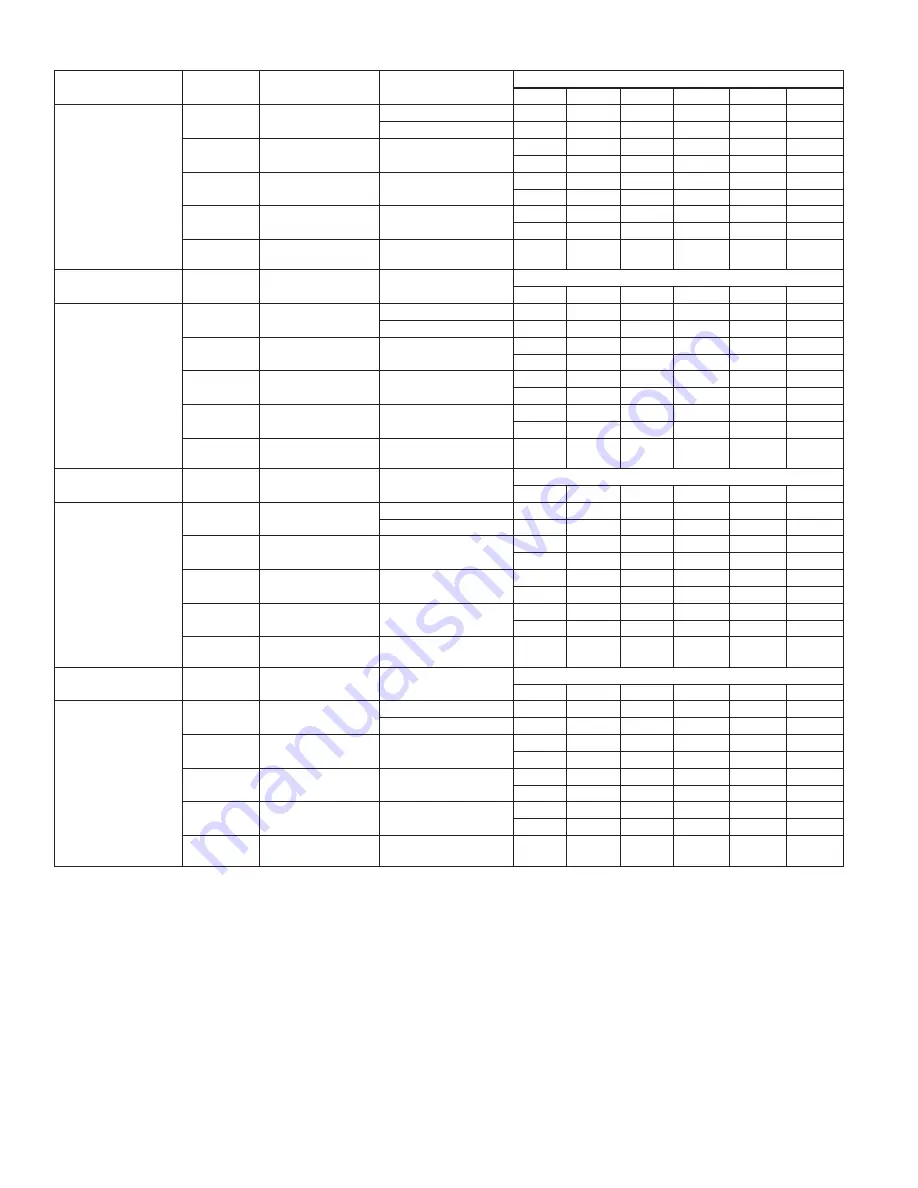
TABLE 7—MAXIMUM ALLOWABLE PIPE LENGTH (FT)
Continued
ALTITUDE
UNIT
SIZE
TERMINATION
TYPE
PIPE DIAMETER
(IN.)*
NUMBER OF 90° ELBOWS
1
2
3
4
5
6
6001 to 7000‡
042040
2 Pipe or 2-In.
Concentric
1-1/2
35
30
25
20
15
10
2
70
70
68
67
66
64
042060
2 Pipe or 2-In.
Concentric
1-1/2
35
30
25
20
15
10
2
70
70
68
67
66
64
042080
060080
2 Pipe or 2-In.
Concentric
1-1/2
20
15
10
5
NA
NA
2
70
70
68
67
62
57
060100
2 Pipe or 2-In.
Concentric
2
31
26
21
16
11
6
2-1/2
70
70
68
67
66
64
060120
2 Pipe or 3-In.
Concentric
3†
49
48
47
45
44
43
Altitude
Unit
Size
Termination
Type
Pipe Diameter
(In.)*
Number of 90° Elbows
1
2
3
4
5
6
7001 to 8000‡
042040
2 Pipe or 2-In.
Concentric
1-1/2
32
27
22
17
12
7
2
66
65
63
62
60
59
042060
2 Pipe or 2-In.
Concentric
1-1/2
32
27
22
17
12
7
2
66
65
63
62
60
59
042080
060080
2 Pipe or 2-In.
Concentric
1-1/2
18
13
8
NA
NA
NA
2
66
65
63
62
57
52
060100
2 Pipe or 2-In.
Concentric
2
29
24
19
14
9
NA
2-1/2
66
65
63
62
60
59
060120
2 Pipe or 3-In.
Concentric
3†
46
44
43
41
40
38
Altitude
Unit
Size
Termination
Type
Pipe Diameter
(In.)*
Number of 90° Elbows
1
2
3
4
5
6
8001 to 9000‡
042040
2 Pipe or 2-In.
Concentric
1-1/2
30
25
20
15
10
5
2
62
60
58
56
55
53
042060
2 Pipe or 2-In.
Concentric
1-1/2
30
25
20
15
10
5
2
62
60
58
56
55
53
042080
060080
2 Pipe or 2-In.
Concentric
1-1/2
17
12
7
NA
NA
NA
2
62
60
58
56
51
46
060100
2 Pipe or 2-In.
Concentric
2
27
22
17
12
7
NA
2-1/2
62
60
58
56
55
53
060120
2 Pipe or 3-In.
Concentric
3†
43
41
39
37
35
34
Altitude
Unit
Size
Termination
Type
Pipe Diameter
(In.)*
Number of 90° Elbows
1
2
3
4
5
6
9001 to 10000‡
042040
2 Pipe or 2-In.
Concentric
1-1/2
27
22
17
12
7
NA
2
57
55
53
51
49
47
042060
2 Pipe or 2-In.
Concentric
1-1/2
27
22
17
12
7
NA
2
57
55
53
51
49
47
042080
060080
2 Pipe or 2-In.
Concentric
1-1/2
15
10
5
NA
NA
NA
2
57
55
53
51
46
41
060100
2 Pipe or 2-In.
Concentric
2
24
19
14
9
NA
NA
2-1/2
57
55
53
51
49
47
060120
2 Pipe or 3-In.
Concentric
3†
39
37
35
33
31
29
* Disk usage—Unless otherwise stated, use perforated disk assembly (factory-supplied in loose parts bag).
† Wide radius elbow.
‡ Vent sizing for Canadian installations over 4500 ft (1370m) above sea level are subject to acceptance by the local authorities having jurisdiction.
NA—Not Allowed; pressure switch will not make.
NOTES:
1. Do not use pipe size greater than those specified in table or incomplete combustion, flame disturbance, or flame sense lockout may occur.
2. Size both the combustion-air and vent pipe independently, determine the smallest diameter allowed by the table for each pipe, then use the larger diameter for both pipes.
3. Assume two 45° elbows equal one 90° elbow. Long radius elbows are desirable and may be required in some cases.
4. Elbows and pipe sections within the furnace casing and at the vent termination should not be included in vent length or elbow count.
5. The minimum pipe length is 5 ft for all applications.
—30—
Summary of Contents for CONDENSING GAS FURNACE 355MAV
Page 51: ... 51 ...