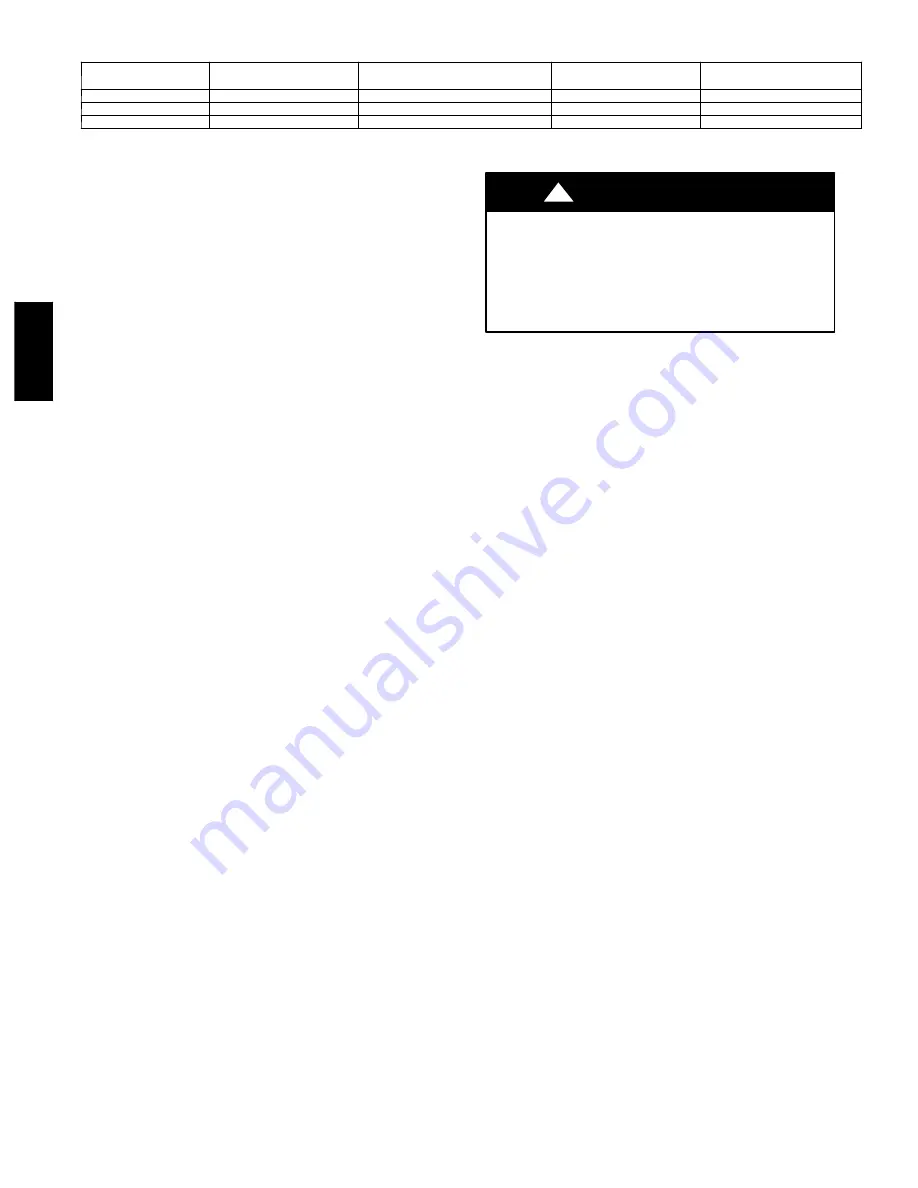
10
Table 4 – Recommended Minimum Chimney Sizes
FIRING RATE
(GPH)
CHIMNEY HEIGHT
(FT.)
NORMAL CHIMNEY AREA (IN.)
ROUND LINER INSIDE
DIAMETER (IN.)
SQUARE LINER INSIDE
DIMENSIONS (IN.)
0.60 to 1.30
15
8 X 8
6
6---3/4 X 6---3/4
1.31 to 1.80
15
8 X 8
7
6---3/4 X 6---3/4
1.81 to 2.00
20
8 X 8
8
6---3/4 X 6---3/4
---For elevations above 2000 ft. above sea level, add 3 ft. to chimney heights. (See figure 12.)
Chimney and Chimney Connection
Follow local codes.
In the absence of local codes, follow
ANSI/NFPA 31 Installation of Oil Burning Equipment, latest
revision.
A. Checking Chimney
The chimney is a very important part of the heating system. No
boiler, however efficient its design, can perform satisfactorily if
the chimney serving it is inadequate. Check chimney to make
certain it is the right size, properly constructed, and in sound
condition.
B. Chimney Connector and Draft Regulator
Boiler requires 6--in. diameter chimney connector pipe. The draft
regulator shipped with boiler must also be used. When properly
installed, the regulator controls the draft automatically. It is best to
install it in a horizontal section of the pipe, but it may be in an
angled or vertical section. Make certain that the “top” is at top and
that the short pipe section which holds vane is horizontal. Install
it as close as practicable to boiler. (See Fig. 12.)
Install chimney connector as follows:
1. Start at boiler with a vertical pipe, at least 1 foot tall, and
then an elbow.
2. Install draft regulator making it horizontal.
3. When regulator is in place, start at chimney and work back
to regulator.
4. Join the 2 sections with a drawband. The horizontal pipe
must slope up toward chimney at least 1/4--in. per ft.. It
must not leak and must be firmly supported.
5. Join sections with at least 3 sheet metal screws. Space
evenly around the pipe.
6. Support every 5 feet with metal straps or stove pipe wire.
C. Minimum Vent Pipe Clearance
Wood and other combustible materials must not be closer than
18--in. from any surface of vent pipe.
Electrical Wiring
See Fig. 14 for wiring diagrams for the various models.
A. Installing Thermostat (Not Provided)
The 24--v thermostat location has an important effect on
operation of boiler system. BE SURE TO FOLLOW
INSTRUCTIONS INCLUDED WITH THERMOSTAT.
B. Grounding
Permanently ground boiler according to local codes and the
current edition of The National Electrical Code. Run a 14 gage or
heavier copper wire from boiler to a grounded connection in
service panel or a properly driven and electrically grounded
ground rod.
C. Electrical Power Supply
ELECTRICAL SHOCK HAZARD
Failure to follow this warning could result in personal
injury or death.
Turn off electric power at fuse box before making any line
voltage connections. Follow local electric codes
!
WARNING
All electrical work must conform to local codes as well as the
National Electrical Code. If not familiar with wiring and codes in
general, have a competent electrician do this job.
Boiler controls are all wired at the factory. All that is required is
to connect a 115--v electric supply and thermostat wires to
aquastat relay.
Run a separate circuit from a separate overcurrent protective
device in electrical service entrance panel. This should be a
15--amp circuit. Locate a shutoff switch at boiler. It must be
turned OFF during any maintenance. Solder and tape or securely
fasten these connections with wire nuts.
D. Connecting 115--V Electrical Wiring to Boiler
Connect 115--v electric supply wires to terminals L1 and L2 on
aquastat relay. (See Fig. 14.)
E. Thermostat Connections
The 2 wires from thermostat connect to terminals T and T on
L8148A and L8124C aquastat relay (See Fig. 14.)
F. Thermostat Heat Anticipator Adjustment
Set heat anticipator at 0.2 amps. Measure the AMP draw of the
thermostat circuit and adjust the anticipator setting if necessary.
Equipment and Optional
Accessories
A. Relief Valve (Required, Provided)
Each low--pressure hot water heating boiler is provided with a
relief valve for over--pressure protection of boiler and heating
system. The relief valve opens when pressure in boiler rises to 30
psig. Each relief valve is provided with a lifting device for testing
and should be tested monthly during heating season. Escape
piping should be provided from discharge side of relief valve so
as to prevent scalding or other hazardous situations. The escape
piping must remain full size and end at a safe point of discharge.
B. Expansion Tank (Not Provided)
In a properly assembled system, expanding water flows into an
expansion tank. This tank should be of the correct size.
The tank is filled with air. As the water expands, it compresses the
air in tank to form an air pressure cushion. This “spring--like”
cushion serves s to maintain correct operating water pressure
regardless of water temperature. This assures a “full measure” of
water even in the highest radiation unit of system. It also prevents
blowing off the relief valve.
The air in tank in the beginning (with system filled with cold
water) is sufficient for proper operation. The tank also serves as a
trap for excess s air in system. This air would cause gurgling in
pipes and inefficient circulation in radiators if left in system.
BW
4
/BW
5