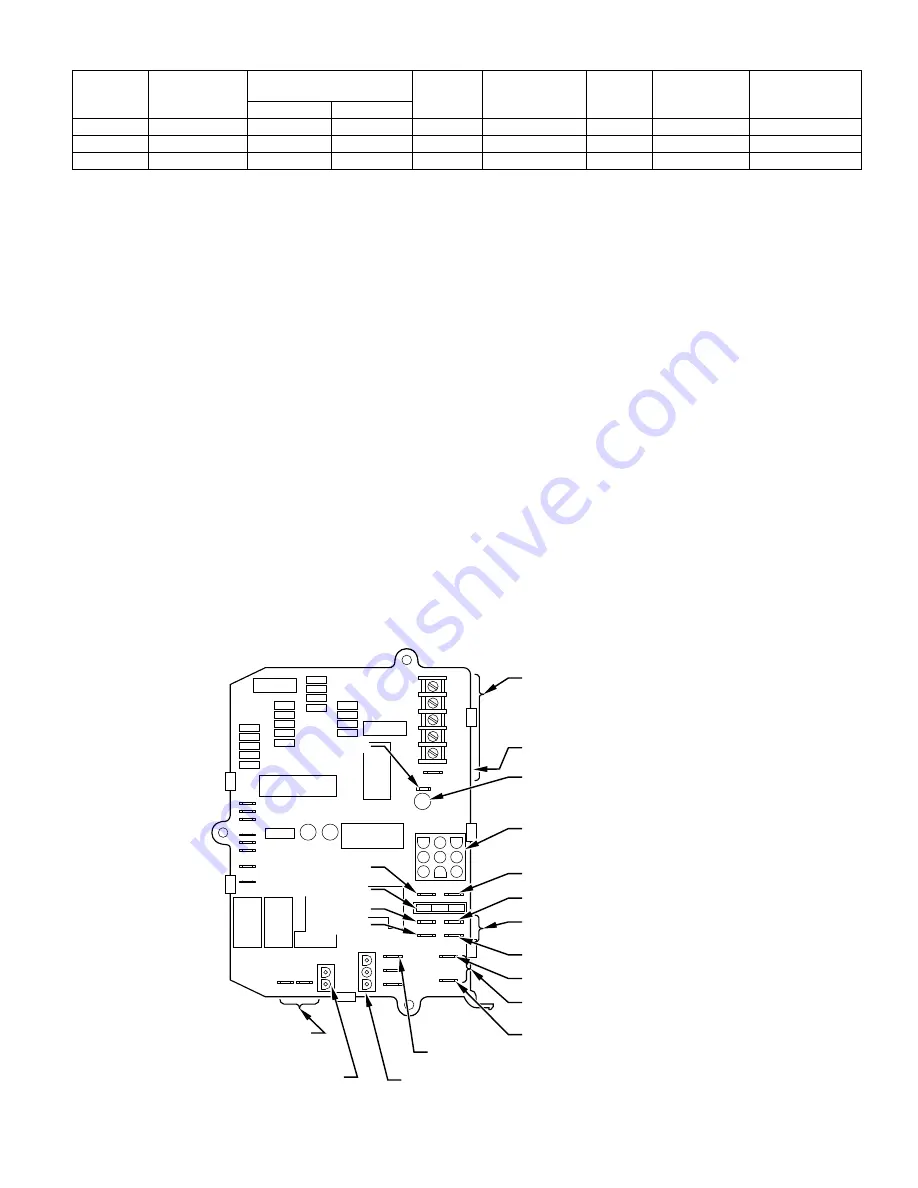
2. Inspect the venting system for proper size and horizontal
pitch as required in the National Fuel Gas Code, ANSI
Z223.1 or the CAN/CGA B149 Installation Codes and these
instructions. Determine that there is no blockage or restric-
tion, leakage, corrosion, and other deficiencies which could
cause an unsafe condition.
3. In so far as is practical, close all building doors and
windows and all doors between the space in which the
appliance(s) connected to the venting system are located
and other spaces of the building. Turn on clothes dryers and
any appliance not connected to the venting system. Turn on
any exhaust fans, such as range hoods and bathroom
exhausts, so they shall operate at maximum speed. Do not
operate a summer exhaust fan. Close fireplace dampers.
4. Follow the lighting instructions. Place the appliance being
inspected in operation. Adjust thermostat so appliance shall
operate continuously.
5. Test for draft hood equipped appliance spillage at the draft
hood relief opening after 5 minutes of main burner opera-
tion. Use the flame of a match or candle.
6. After it has been determined that each appliance connected
to the venting system properly vents when tested as outlined
above, return doors, windows, exhaust fans, fireplace damp-
ers, and any other gas-burning appliance to their previous
conditions of use.
7. If improper venting is observed during any of above tests,
the venting system must be corrected.
Vent system or vent connectors may need to be resized. For any
other appliances when resizing vent systems or vent connectors,
system or connector must be sized to approach minimum size as
determined using appropriate table found in the NFGC or NSC-
NGPIC.
II.
COMBUSTION-AIR AND VENT PIPING
A.
General
Combustion-air and vent pipe fittings must conform to American
National Standards Institute (ANSI) standards and American
Society for Testing and Materials (ASTM) standards D1785
(schedule-40 PVC), D2665 (PVC-DWV), D2241 (SDR-21 and
SDR-26 PVC), D2661 (ABS-DWV), F628 (schedule-40 ABS), or
F891 (PVC-DWV cellular core). Pipe cement and primer must
conform to ASTM standards D2564 (PVC) or D2235 (ABS). See
Table 7 for maximum pipe lengths and Fig. 22, 23, 24, 25, and 26
for exterior piping arrangements.
In Canada construct all combustion-air and vent pipes for this unit
of CSA or ULC certified schedule-40 PVC, PVC-DWV or
ABS-DWV pipe and pipe cement. SDR pipe is NOT approved in
Canada.
TABLE 5—ELECTRICAL DATA
UNIT
SIZE
VOLTS—
HERTZ—
PHASE
OPERATING
VOLTAGE RANGE
MAX
UNIT
AMPS
UNIT
AMPACITY†
MIN
WIRE
SIZE
MAX WIRE
LENGTH
(FT)‡
MAX FUSE
OR CKT BKR
AMPS**
Max*
Min*
036080
115—60—1
127
104
7.6
10.4
14
36
15
048080
115—60—1
127
104
10.0
13.4
14
28
15
060080
115—60—1
127
104
14.1
18.4
12
31
20
* Permissible limits of voltage range at which unit will operate satisfactorily.
† Unit ampacity = 125 percent of largest operating component’s full load amps plus 100 percent of all other potential operating components’ (EAC, humidifier, etc.) full load
amps.
‡ Length shown is as measured 1 way along wire path between unit and service panel for maximum 2 percent voltage drop.
** Time-delay type is recommended.
Fig. 17—Control Center
A95086
C
OM
24V
HUM
G
R
Y
W
3-AMP FUSE
HUMIDIFIER TERMINAL
(24-VAC 0.5 AMP MAX)
LED OPERATION &
DIAGNOSTIC LIGHT
HARNESS CONNECTOR
24-V TRANSFORMER SEC-2
SPARE-1
SPARE-2
EAC-1
EAC-ELECTRONIC AIR CLEANER
TERMINALS (115-VAC 1.5 AMP MAX)
EAC-2
115-VAC (L2) NEUTRAL
CONNECTION
24-V THERMOSTAT
TERMINALS
BLOWER SPEED
SELECTION TERMINALS
INDUCER MOTOR
CONNECTOR
115-VAC (L1)
POWER SUPPLY
HOT SURFACE
IGNITOR CONNECTOR
HEAT
COOL
SEC-1
TEST/TWIN
—15—
Summary of Contents for 351DAS
Page 35: ...35...