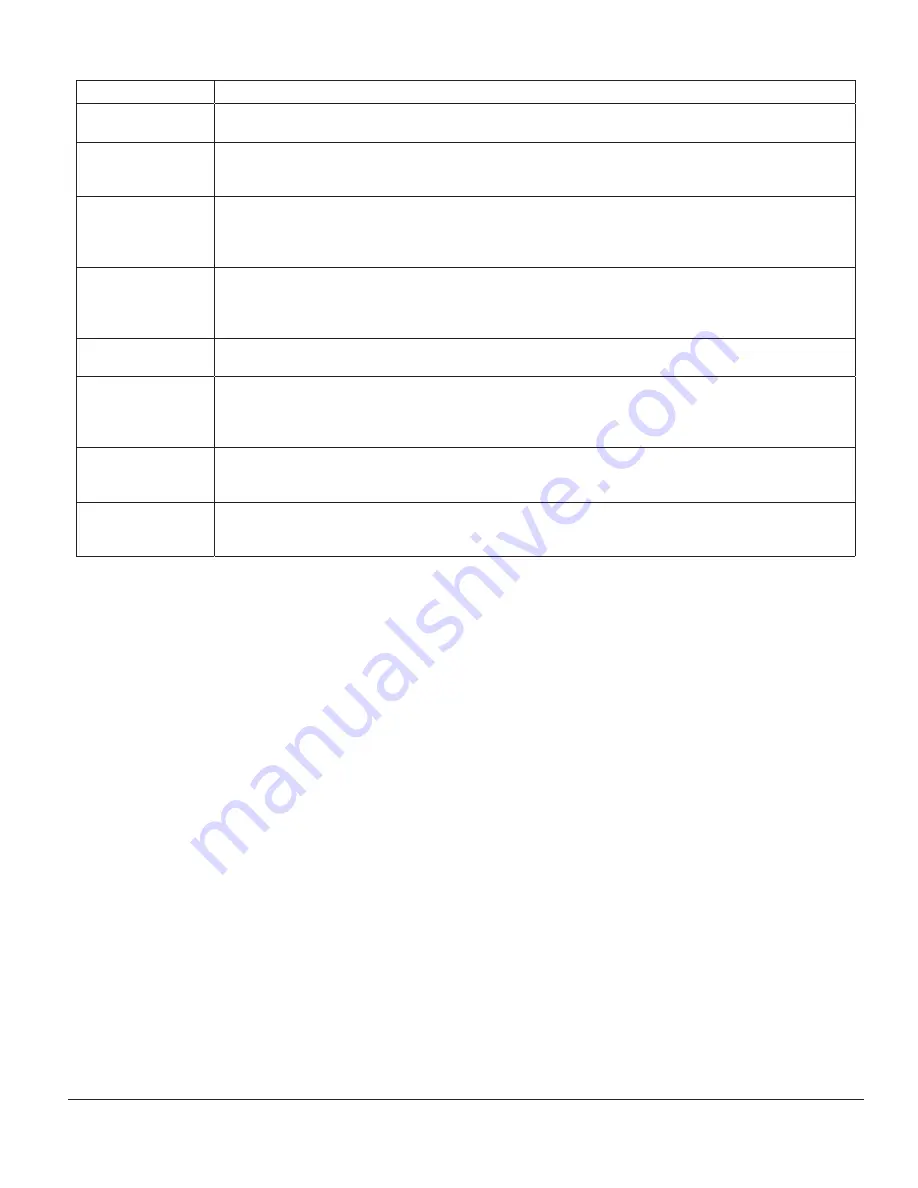
59
Bryan Steam, LLC
www.bryanboilers.com
Phone: 765-473-6651
783 N Chili Ave, Peru, IN 46970 [email protected]
Table 30: Safety and Operating Controls
Component
Function
Power Switch
If this switch is in the off position, power is interrupted to the control circuit of the boiler, which prevents the boil-
er from operating. If the switch is in the on position, power is supplied to the control circuit.
Automatic Reset Oper-
ating Aquastat
If the boiler water temperature exceeds the adjustable set point, power is interrupted to the control circuit of the
boiler, which prevents the boiler from operating. When the boiler water temperature drops below the set point
minus the adjustable differential setting, power is again supplied to the control circuit.
Manual Reset High
Limit Aquastat
If the boiler water temperature exceeds the adjustable set point, power is interrupted to the control circuit of the
boiler, which prevents the boiler from operating. Power is interrupted until the control is manually reset pressing
the control’s reset button. When the button is pressed, power will again be supplied to the control circuit, assum-
ing that the boiler water temperature has dropped below the setpoint minus the differential setting.
Water Flow Switch
If the water flow through the boiler drops below the fixed flow rate required to move the control’s paddle enough
to close the control’s contacts, power is interrupted to the control circuit, which prevents the boiler from oper-
ating. When the water flow rate increased, the paddle closes the control’s contacts and power is supplied to the
control circuit.
Pressure / Safety
Relief Valve
If the pressure inside the boiler exceeds the fixed set point, the valve opens mechanically and discharges water.
The valve remains open until the pressure inside the boiler drops below the set point.
High and Low Gas
Pressure Switches
If the gas pressure reaches a point above or below the adjustable set point, the contacts of the switch open and
power is interrupted to the control circuit that prevents the boiler from operating. Power is interrupted until gas
pressure is between the high and low gas pressure set points and the control is manually reset moving the switch
to the reset position. The switches will not reset until the gas pressure is within the set point parameters.
Minimum Air Pressure
Switch
If the differential air pressure drops below the fixed set point, the contacts of the switch open and power is inter-
rupted to the control circuit, which prevents the boiler from operating. Power is interrupted until air flow/pres-
sure increases so that contacts close.
Maximum Air Pres-
sure Switch
If the differential air pressure exceeds the fixed set point, the contacts of the switch open and power is interrupt-
ed to the control circuit, which prevents the boiler from operating. Power is interrupted until air flow/pressure
decreases below the setting so that the contacts close.
K.
Troubleshooting
Refer to the troubleshooting section in the Concert Boiler Control manual on how to navigate the Limit String
Status screen that shows an active safety limit status and for an in-depth guide to all the possible lockouts as
well as recommended corrective actions for restore boiler operation.
For High Turndown Free Flex 1500-6000 boilers display issues, contact you Sales Rep for the latest PLC and
Display updates. If you don't know who your sales rep is, call the number listed at the bottom of the page.