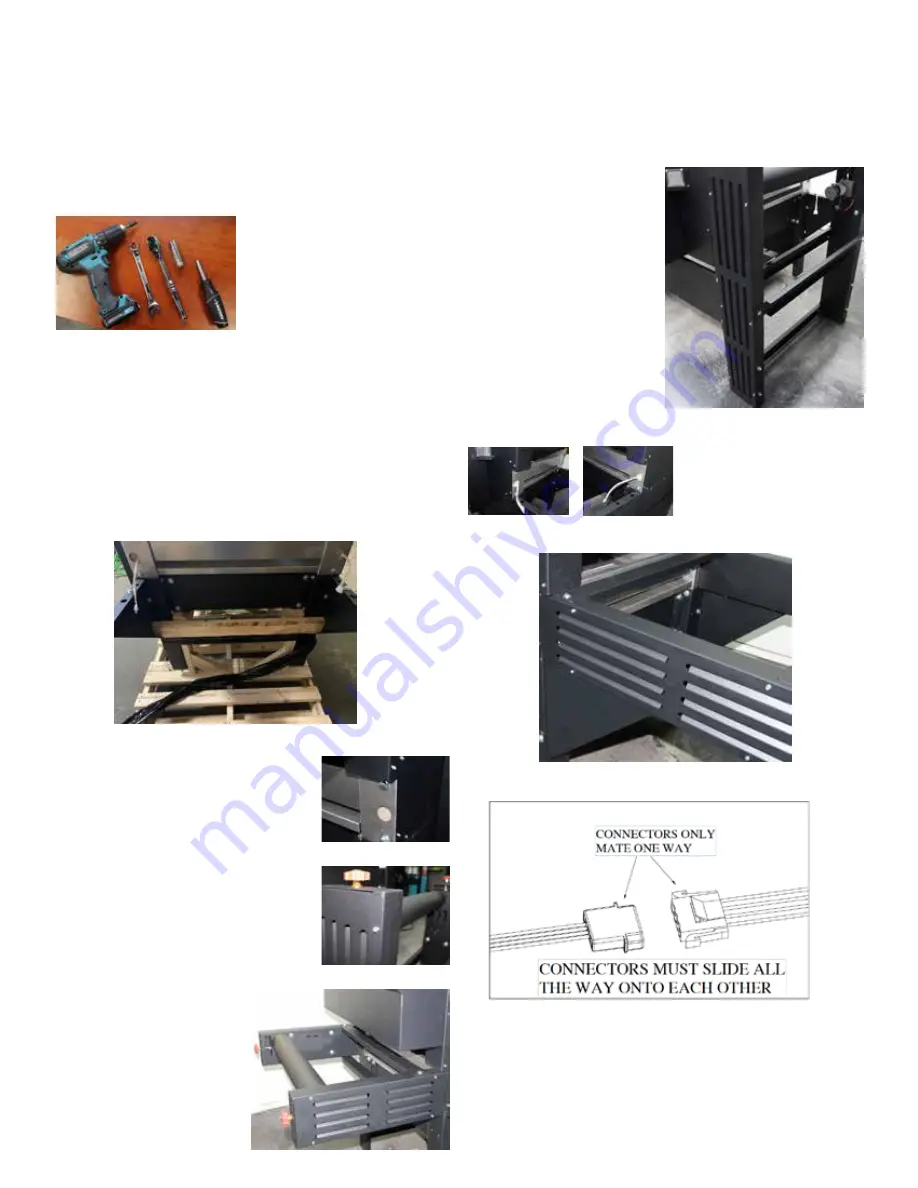
Step 6: Remove the cover plates from the feed extension
using a 1/4” nut driver. Remove the 3/8-16 nuts, washer
and bolts from the feed extension. Remove the 3/8-16 bolts
and washers the front end of the oven. There are triangular
trusses for supporting the
feed end of the oven. Sit
the extension on top of these
trusses.
Feed the motor and photoeye
wires through and connect
the ends. See Figure 2.
Use the hardware to secure
the feed end to both the
end of the oven andf to the
trusses. Secure with the
wrench.
Unpacking and Assembly
Tools needed
• 9/16 open end wrench or ratchet wrench
• 1/4” nut driver, manual or powered
• screwdriver bit
Step 1: Remove the feed end of the oven from the top of
the machine.
Step 2: Remove the exit extension from the crate under the
control panel.
Step 3: Remove the wooden securing board from undeer
the machine using a powered screwdriver. Remove the
main body from the skid and place into desired position.
Place the machine into a stable location.
Step 4: Remove the 3/8-16 hardware
from the exit end of the machine.
Step 5: Remove the cover plates
from the exit extension using a 1/4”
nut driver. Use the 3/8-16 bolts and
washers to attach the exit extension to
the end of the oven. The exit is to the
left of the control panel. Tighten with
a 9/16” wrench. Reattach the cover
plates.
Figure 2: Connecting belt sensor wires