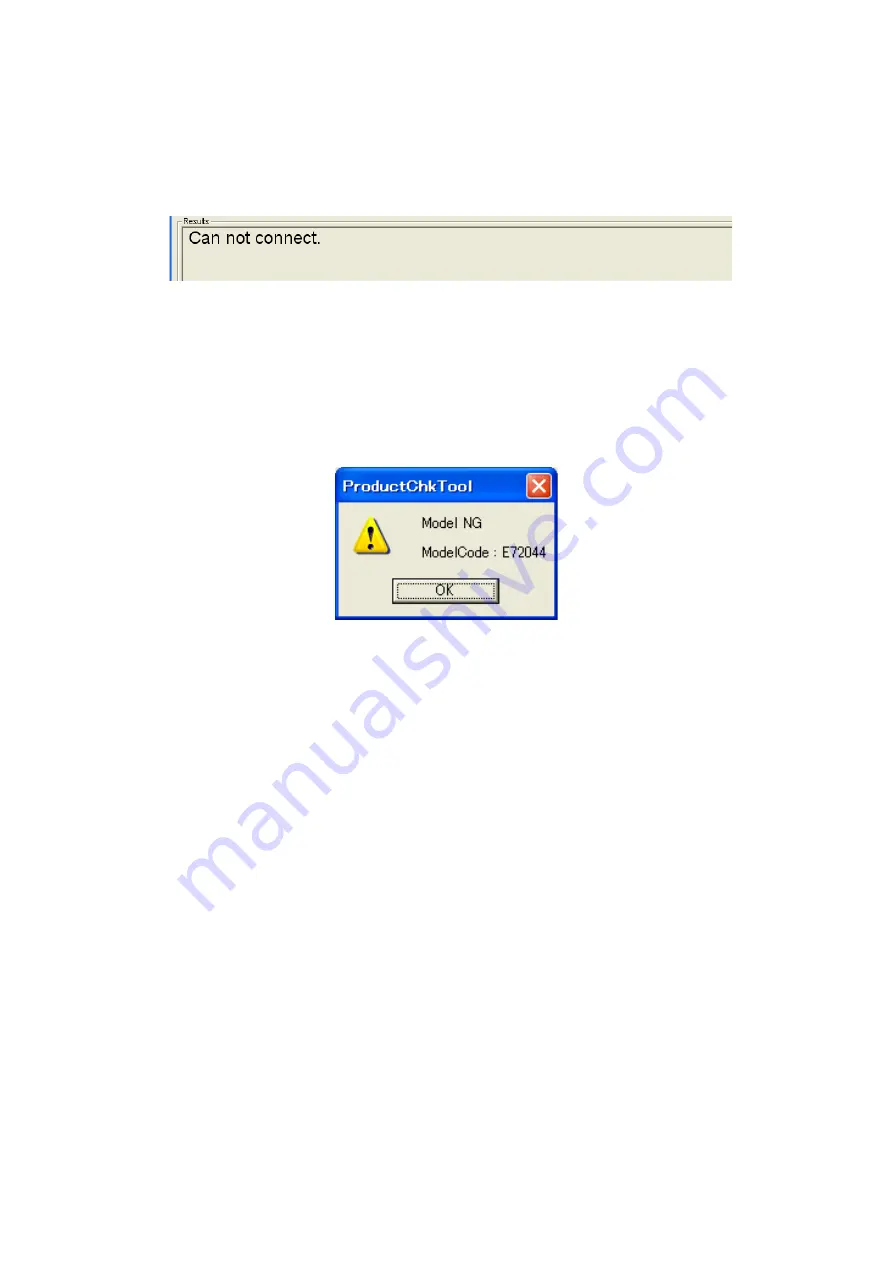
1 - 8
Inspection errors
• Can not connect.
The following error occurs when the machine is not connected with PC. Check that the
machine is connected to the PC properly and the machine is turned ON.
Figure 7. Can not connect.
• Model NG
Model code (first 6-digits) of the serial number is not for the relevant model.
→
The model may be wrong. Check the rating plate to see if it is the right model. Check if
the tool and inspected model is matched. Version displayed in the "Model Info" field may
be old. Check if the latest version of the Serviceman tool is being used.
Figure 8. Model NG
Summary of Contents for TD-2020
Page 1: ...SERVICE MANUAL MODEL TD 2020 2120N 2130N ...
Page 114: ...Feb 2013 SM PT056 5 ...