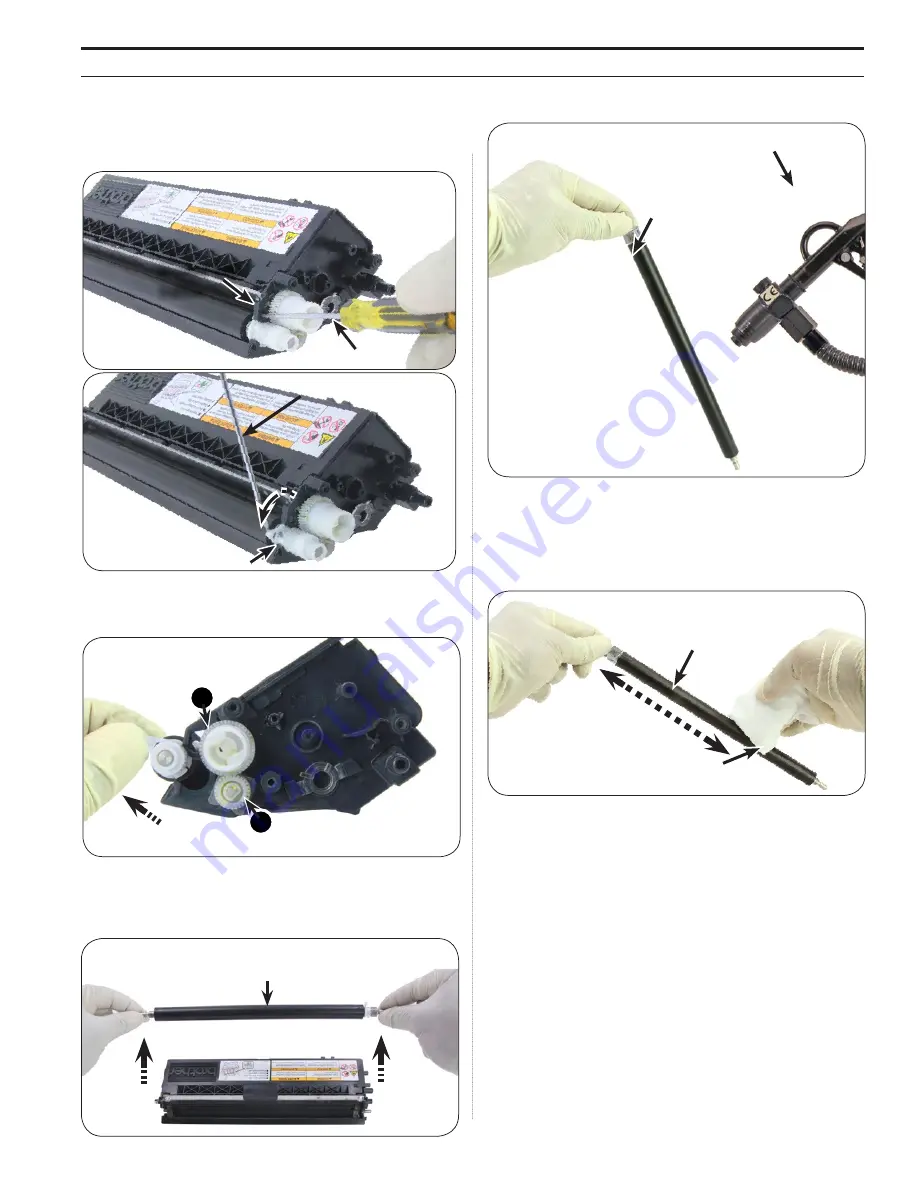
sss
™
1143
page
6
D
isassembling
The
C
arTriDge
7. Place a slotted screwdriver into the opening directly in front of the
developer roller stabilizer. Gently press on the stabilizer to release
(Figure 7a). Rotate the developer roller stabilizer out and down as
shown in Figure 7b.
Developer Roller
Stabilizer
Figure 7a
Slotted
Screwdriver
Figure 7b
Developer Roller Stabilizer
Slotted Screwdriver
8. Lift the developer roller slightly to remove the drive gear. Remove the
drive gear and toner adder roller gear in the order shown in Figure 8.
Figure 8
Toner Adder Roller Gear
Drive Gear
2
1
9. Remove the developer roller by grasping the ends of the roller and
pulling out and away from the cartridge as shown in
Figure 9.
Figure 9
Developer Roller
10. Blow with dry, filtered, ionized, compressed air (Figure 10).
Figure 10
Air Gun
Developer Roller
11. Using a lint-free cloth dampened with 91-99% isopropyl alcohol,
gently clean the developer roller using end-to-end strokes. Using
another lint-free cloth, dampened with de-ionized water, gently wipe
the developer roller as shown in Figure 11. Blow with dry, filtered,
ionized, compressed air.
Figure 11
Lint-Free Cloth
Developer Roller