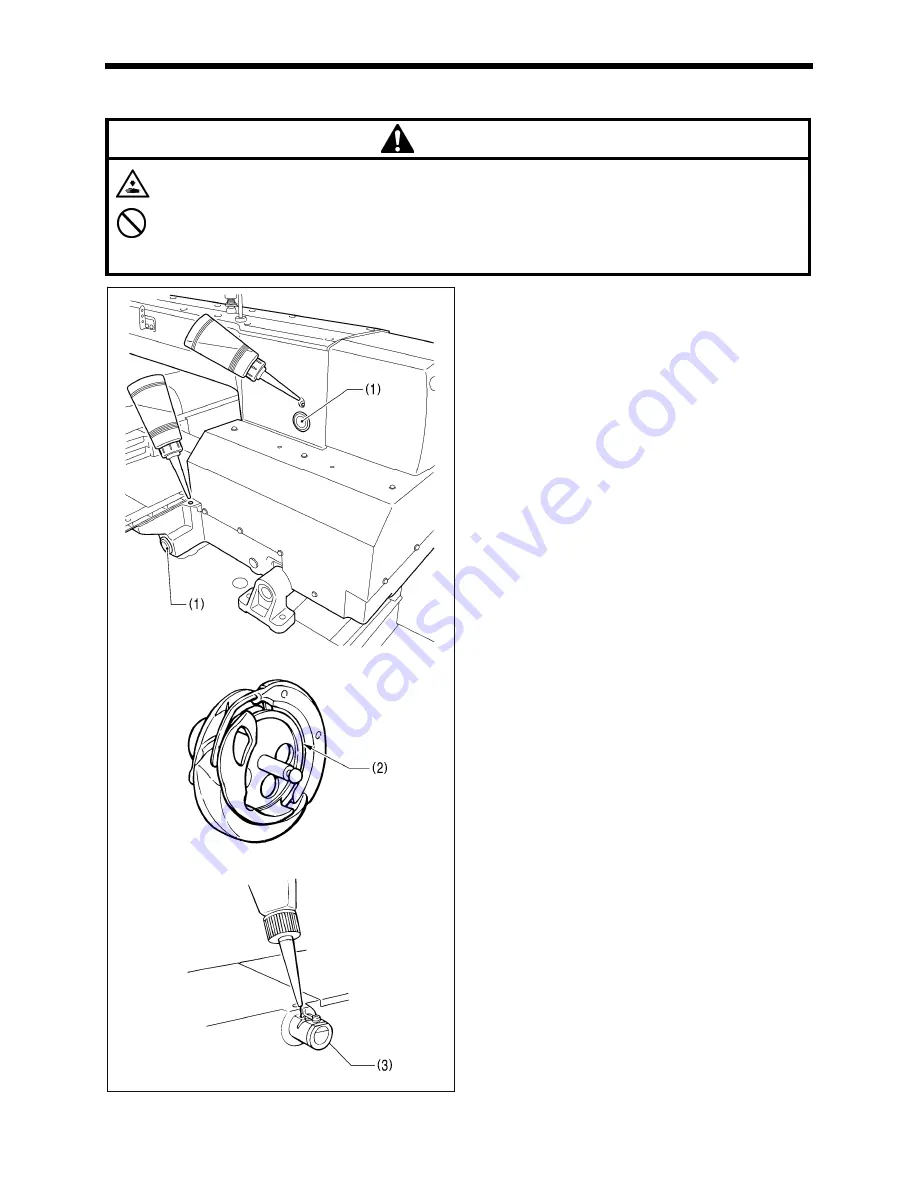
4. INSTALLATION
17
BAS-342G PS
4-18. Lubrication [13]
CAUTION
Do not connect the power cord until lubrication is complete.
If the foot switch is depressed by mistake, the sewing machine might start operating and injury could result.
Be sure to wear protective goggles and gloves when handling the lubricating oil and grease, so that they do not get into
your eyes or onto your skin. If the oil and grease get into your eyes or onto your skin, inflammation can result.
Furthermore, do not drink or eat the lubricating oil or grease. They may cause diarrhea or vomiting.
Keep the oil out of the reach of children.
•
The sewing machine should always be lubricated and the oil
supply replenished before it is used for the first time, and
also after long periods of non-use.
•
Use only the lubricating oil <JX Nippon Oil & Energy
Corporation Sewing Lube 10N; VG10> specified by Brother.
* If this type of lubricating oil is difficult to obtain, the recommended
oil to use is <Exxon Mobil Essotex SM10; VG10>.
1. Fill the arm oil tank and the bed oil tank with oil.
NOTE:
Be sure to add more oil when the oil level drops down
to about one-third full in the oil gauge window (1). If the
oil drops below the one-third full level in the oil gauge
window (1), there is the danger that the sewing
machine may seize during operation.
2. Remove the bobbin case and add 2-3 drops of oil to the
rotary hook race (2).
3. If using the needle cooler (3), fill it with silicon oil (100
mm
2
/s).
(Refer to "5-3. Threading the upper thread" for details on
using the needle cooler (3).)
2752B
2753B
3986M
Summary of Contents for BAS-342G PS
Page 85: ...MEMO 76 BAS 342G PS ...