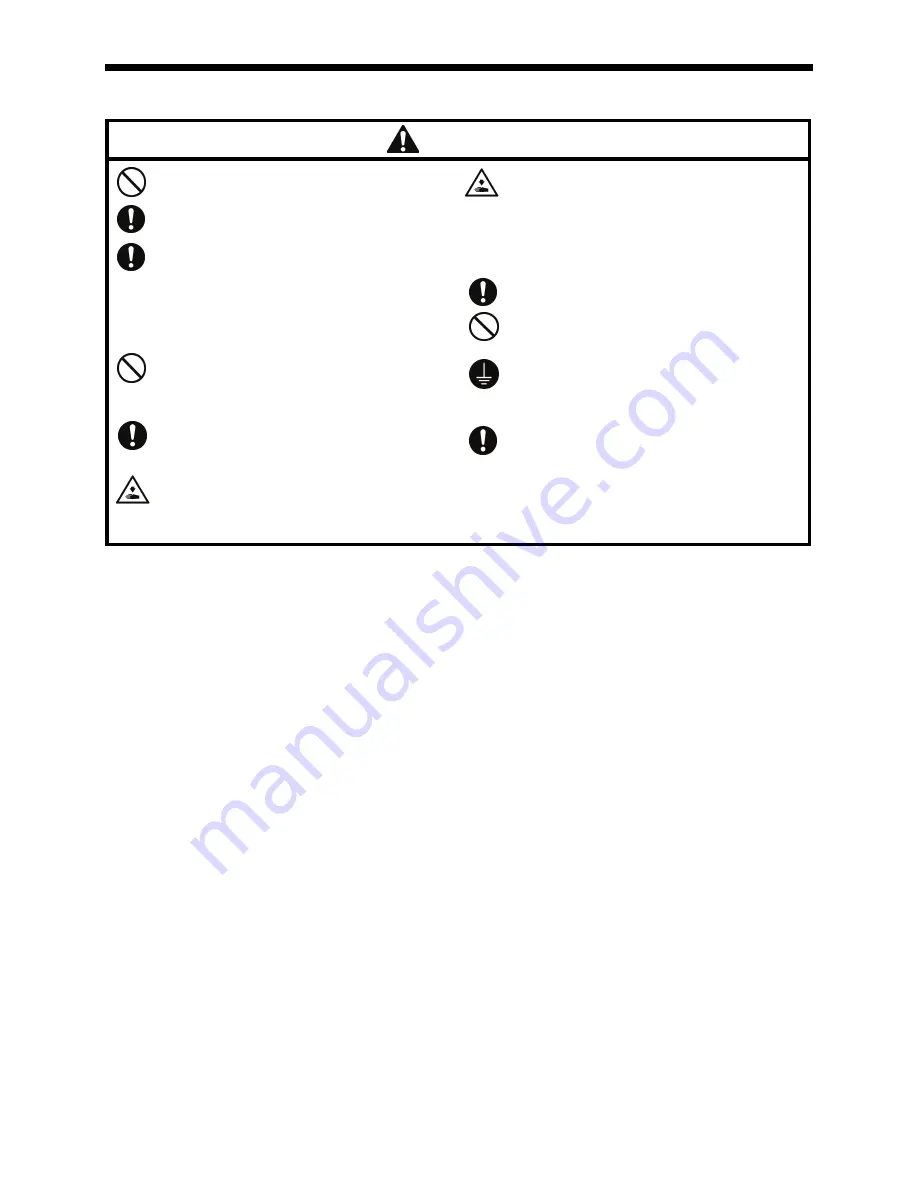
3. INSTALLATION
3
BAS-341H, BAS-342H
3. INSTALLATION
CAUTION
Machine installation should only be carried out by a
qualified technician.
Contact your Brother dealer or a qualified electrician
for any electrical work that may need to be done.
The sewing machine head weighs approximately 160
kg.
Use equipment such as a crane or hoist when
installing the machine head and adjusting the height of
the table.
If you try to lift the machine head yourself, it may cause
injuries such as back injury.
Do not connect the power cord until installation is
complete.
If the foot switch is depressed by mistake, the sewing
machine might start operating and injury could result.
If using a work table which has casters, the casters
should be secured in such a way so that they cannot
move.
Use a table with a height of 84 cm or less. If the table
is too high, the machine head may become
unbalanced and fall down, and serious injury or
damage to the sewing machine may result.
Hold the machine head with both hands when tilting it
back or returning it to its original position.
In addition, do not subject the machine head to extra
force while it is tilted back. If this is not observed, the
machine head may become unbalanced and fall down,
and serious injury or damage to the sewing machine
may result.
All cords should be secured at least 25 mm away from
any moving parts. Furthermore, do not excessively
bend the cords or secure them too firmly staples,
otherwise there is the danger that fire or electric
shocks could occur.
Be sure to connect the ground. If the ground
connection is not secure, you run a high risk of
receiving a serious electric shock, and problems with
correct operation may also occur.
Install the safety covers to the machine head and
motor.