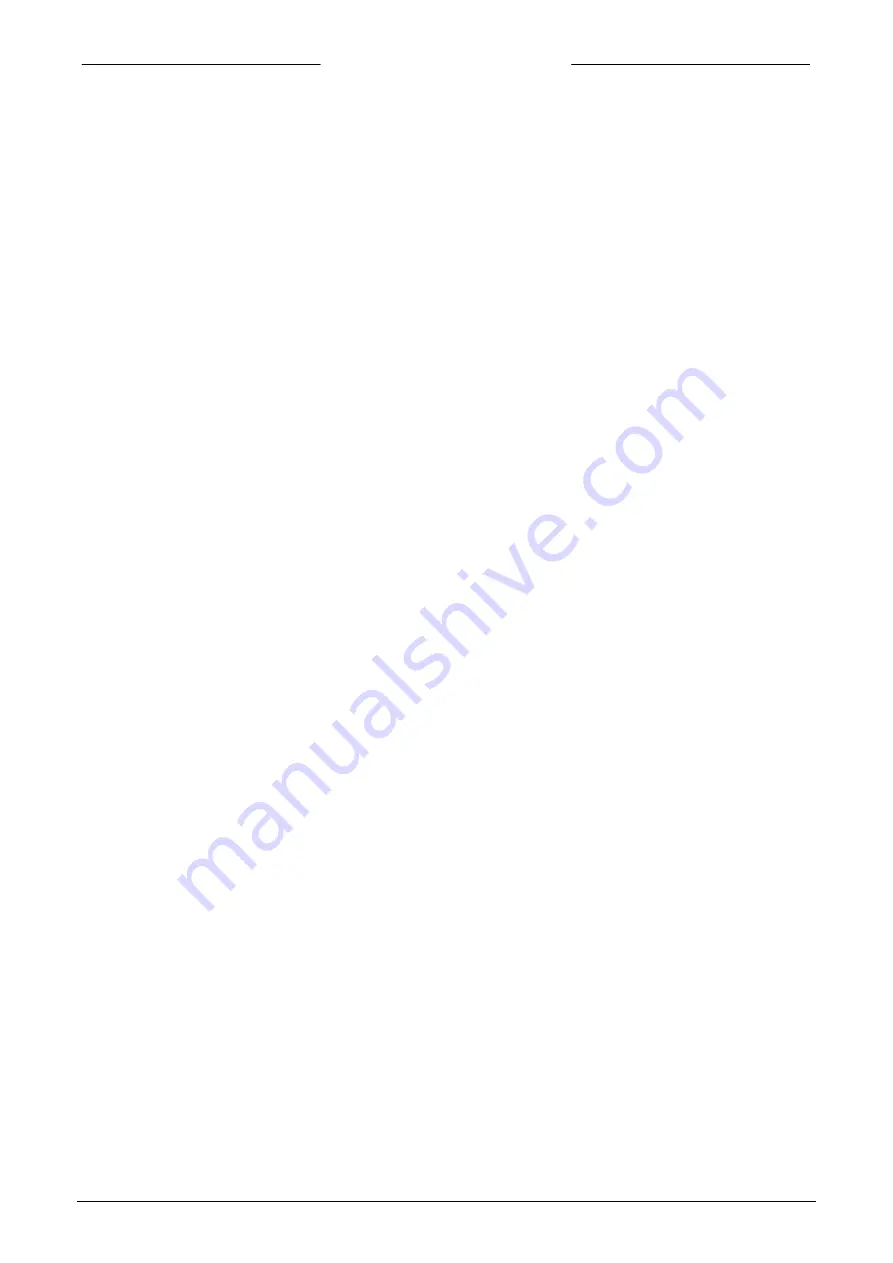
BRONKHORST HIGH-TECH B.V.
9.17.044
page 3
The information in this manual has been reviewed and is
believed to be wholly reliable. No responsibility, however, is
assumed for inaccuracies. The material in this manual is for
information purposes only, and is subject to change without
notice.
Bronkhorst
High-Tech
B.V.
February 2008
Warranty
The products of Bronkhorst High-Tech B.V. are warranteed
against defects in material and workmanship for a period of
three years from the date of shipment provided they are
used in accordance with the ordering specifications and not
subjected to abuse or physical damage. Products that do not
operated properly during this period may be repaired or
replaced at no charge. Repairs are normally warranteed for
one year or the balance of the original warranty, whichever is
the longer.
See also paragraph 9 of the Conditions of Sales.
The warranty includes all initial and latent defects, random
failures, and indeterminable internal causes.
It excludes failures and damage caused by the customer,
such as contamination, improper electrical hook-up, dropping
etc.
Re-conditioning of products primarily returned for warranty
service that is partly or wholly judged non-warranty may be
charged for.
Bronkhorst High-Tech B.V. prepays outgoing freight charges
when any part of the service is performed under warranty,
unless otherwise agreed upon beforehand, however, if the
product has been returned collect to Bronkhorst High-Tech
B.V., these costs are added to the repair invoice. Import
and/or export charges, foreign shipping methods/carriers are
paid for by the customer.