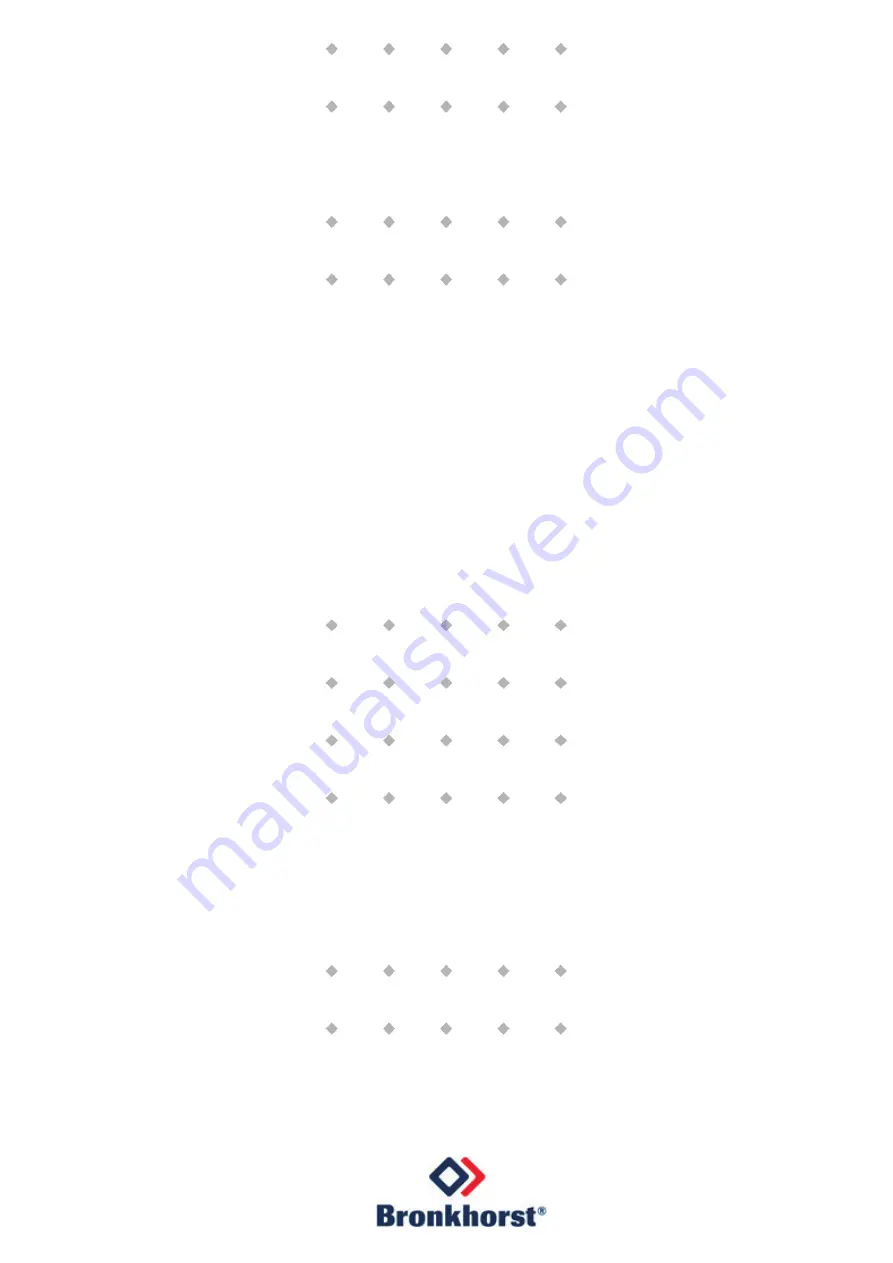
Instruction manual
Explosion proof
Flow Measurement and control
ATEX
Doc. no.: 9.17.028U Date: 25-06-2020
ATTENTION
Please read this instruction manual carefully before installing and operating the instrument.
Not following the guidelines could result in personal injury and/or damage to the equipment.
Related drawing.
No modifications permitted without
approval of the authorised person
.
Summary of Contents for F-112AX
Page 2: ...BRONKHORST ...
Page 6: ...BRONKHORST Appendices 1 Enclosures ...
Page 20: ...BRONKHORST page 20 9 17 028 ...