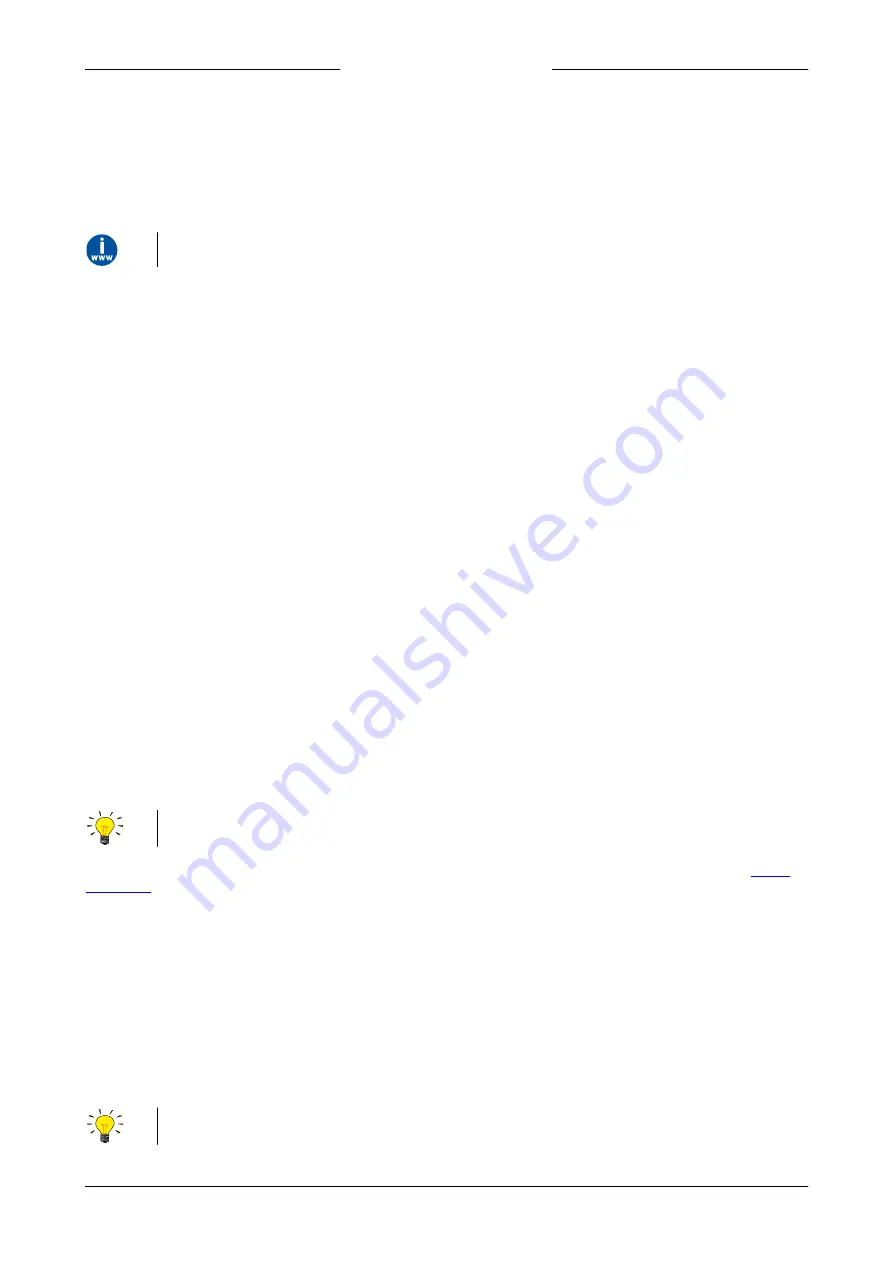
Bronkhorst®
Instruction Manual EL-FLOW® Select
9.17.099J
33
PROFINET
Instruments in a PROFINET system can be monitored and operated using third party software as a master device, such as TIA
Portal (by Siemens).
To configure a device, a so-called GSDML file (General Station Description Markup Language) can be loaded into the
software. The GSDML file contains all necessary information, in XML format, to operate the device in a PROFINET system,
including communication and network configuration, and all available operating parameters with their data types.
A GSDML file for Bronkhorst® instruments can be downloaded from the product pages on the Bronkhorst website:
3.7
Adjusting zero point
The zero point (the signal that corresponds to zero flow) of a Bronkhorst® flow meter/controller is factory adjusted at
approximately 20 °C and atmospheric pressure, with the instrument in an upright position. If the ambient conditions or
mounting position are significantly different, the instrument might detect a flow when actually there is none. In that case,
the instrument needs to be adapted to the new conditions by re-adjusting the zero point.
Before zeroing, prepare the instrument as follows:
1. Make sure the ambient conditions match those of the operating environment
2. Pressurize the instrument with the operational media according to the process conditions
3. Power up the instrument
4. Allow the instrument to warm up and stabilize for at least 30 minutes
5. Block the flow through the instrument, by closing a valve immediately after the instrument outlet and/or capping
outlet connectors
The zero point may be re-adjusted digitally (via RS232 or fieldbus) or manually, using the multifunctional switch. Regardless
of the preferred method, once started, the zeroing procedure itself takes approximately 10 seconds to complete (longer if
the output signal is unstable).
3.7.1
Using multifunctional switch
To start the autozero function with the multifunctional switch, follow these instructions:
1. Change the setpoint of the instrument to 0 (zero)
2. Press and hold the multifunctional switch. After 4 seconds, the red LED
l
will light up; another 4 seconds later the red
LED will extinguish and the green LED
l
will light up
3. At that moment (which is after 8 to 12 seconds), release the switch
The green LED will start to blink fast, indicating that the autozero function is in progress. After (successful) completion, the
green LED will light up continuously, while the output signal is 0 % (parameter
Measure
= 0).
3.7.2
Via digital communication
FlowPlot and FlowSuite provide an easy way to adjust the zero point of an instrument using RS-232 communication; the
Autozero
function automatically performs the procedure described here.
To adjust the zero point using digital communication, set parameter values in the following sequence (see section
for more information about instrument parameters):
Sequence #
Parameter
Value
Action
1
Setpoint
0
stop flow (close control valve)
2
Init Reset
64
unlock secured parameters
3
Control Mode
9
enable calibration mode
4
Calibration Mode
0
reset calibration mode
5
Calibration Mode
9
start zeroing
The green LED starts to blink fast, indicating that the zeroing procedure is in progress. On completion, the green LED will
glow continuously, while the output signal is 0% (parameter
Measure
= 0). At the same time, parameter
Control Mode
returns
to its initial value. If the procedure is successful, parameter
Calibration Mode
changes to 0 (idle). If the procedure fails,
Calibration Mode
changes to 255.
After performing the procedure, remember to set parameter
Init Reset
to value 0 to lock secured parameters.